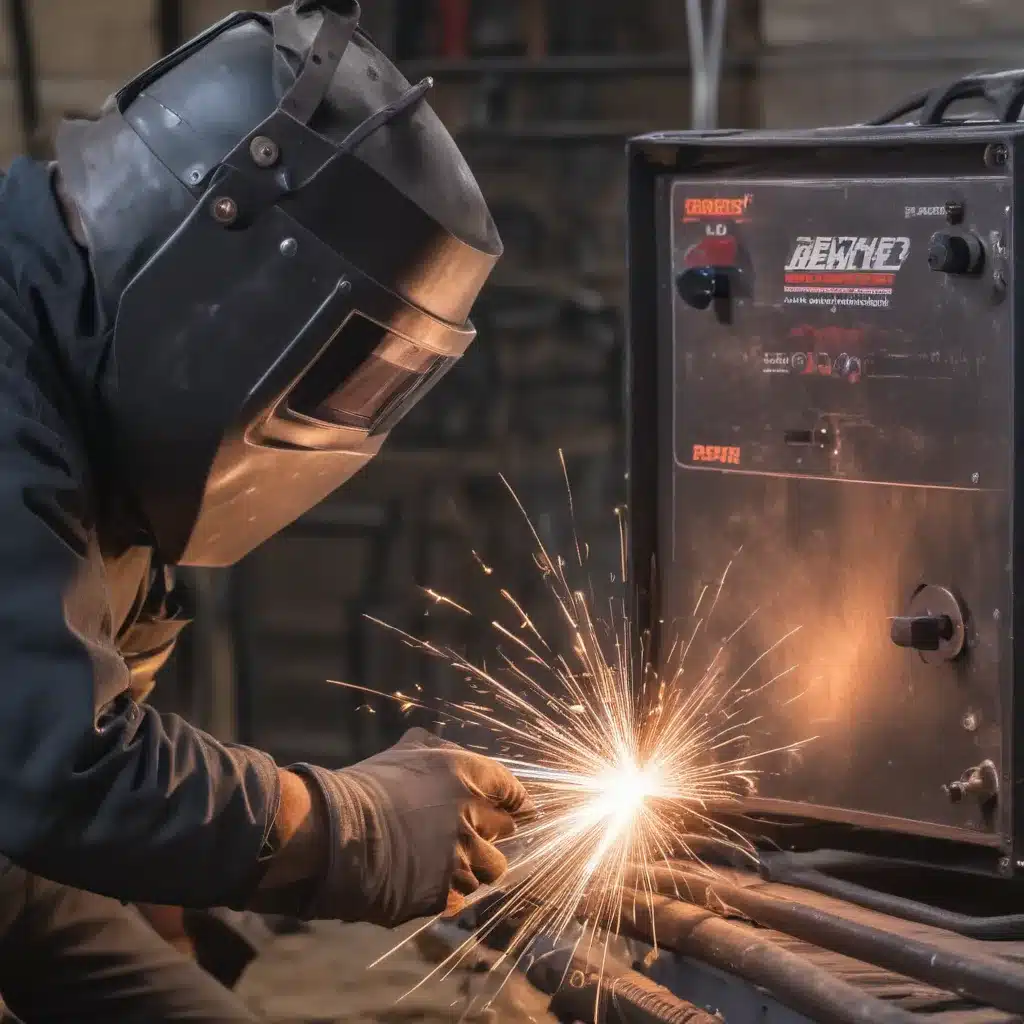
Unleashing the Power of Heat Control: A Welding Journey for Newbies
Ahh, the world of welding – where sparks fly, metal sings, and the art of joining materials becomes a symphony of precision. If you’re a beginner in the welding realm, you’ve probably experienced the thrill and the… well, not-so-thrilling moments. But fear not, my friends! I’m here to share with you the secrets of controlling heat input for better, more consistent welds.
Let’s start with a little analogy, shall we? Imagine you’re a chef, and you’re trying to perfectly sear a steak. You don’t want it to be a charred, unappetizing mess, nor do you want it to be a cold, flabby disappointment. Nope, you want that golden-brown crust, that juicy, tender interior – and that’s exactly what we’re going for with our welds.
You see, the heat input in welding is like the temperature of your stovetop. Too much, and you’ll end up with a brittle, distorted mess. Too little, and your weld won’t even stick. But find that sweet spot, and you’ll be rewarded with a strong, beautiful joint that’ll make even the most experienced welders jealous.
Mastering the Fundamentals: Understanding Heat Input
Alright, let’s dive a little deeper. Heat input in welding is the amount of energy that’s transferred to the workpiece during the welding process. This, my friends, is the key to unlocking the secrets of consistent, high-quality welds.
But how do we actually measure heat input, you ask? Well, it’s all about the magic formula:
Heat Input (kJ/in) = Voltage (V) x Amperage (A) x 60 / Travel Speed (in/min)
Don’t worry, I know it looks like a bunch of gobbledygook, but stick with me. The voltage and amperage are the power settings on your welding machine, and the travel speed is how fast you’re moving the electrode or torch along the joint.
Now, the tricky part is finding the right balance. Too much heat input, and you’ll end up with a wide, shallow weld that’s prone to distortion and cracking. Too little, and you’ll end up with a skinny, underpenetrated mess that’s weaker than a kitten’s meow.
So, how do you find that sweet spot? Well, that’s where the real fun begins.
Dialing in the Perfect Heat Input: Techniques and Tips
Alright, now that we’ve got the basics down, let’s talk about some practical tips and techniques for controlling that heat input like a pro.
First and foremost, pay attention to your welding parameters. Experiment with different voltage and amperage settings, and find the combination that gives you the perfect bead profile – not too wide, not too narrow. Remember, higher voltage and amperage mean more heat input, so adjust accordingly.
Next, let’s talk about travel speed. This is where a lot of beginners struggle, but it’s a crucial part of the equation. The faster you move, the less heat input you’ll have. Slow down too much, and you’ll end up with too much heat, leading to distortion and other nasty problems.
But wait, there’s more! Don’t forget about the angle of your torch or electrode. A steeper angle will concentrate the heat, while a more shallow angle will spread it out. Play around with this and see how it affects your weld quality.
Oh, and let’s not forget about those pesky joint designs. Different joint types, like butt joints, lap joints, and T-joints, will require different heat input levels to achieve the perfect weld. Do your research, experiment, and find what works best for the job at hand.
Real-World Examples: Putting Heat Control into Practice
Now, let’s take a look at some real-world examples of how heat input control can make a difference in the quality of your welds.
Take, for instance, the case of our good friend, Bob. Bob was trying to weld some thin-gauge sheet metal, and he was struggling to get a decent bead. He was cranking up the heat, trying to make it happen, but all he ended up with was a warped, brittle mess.
After a quick chat with the welding experts at Corrconnect, Bob learned that he needed to lower his heat input to avoid distortion. He dialed back the voltage and amperage, increased his travel speed, and voila – perfect welds that looked like they were done by a pro.
Or how about the time when our pal, Jill, was working on a heavy-duty steel fabrication project? She was getting frustrated because her welds were taking forever to cool down, and the distortion was driving her crazy. Turns out, she was using way too much heat input for the job.
With a few adjustments to her welding parameters, Jill was able to find the sweet spot and crank out those welds like a seasoned veteran. The final product was a thing of beauty, and Jill was the talk of the shop.
The Welding Wizard’s Parting Words
Ah, the joys of welding – where the perfect balance of heat, speed, and technique can transform a humble piece of metal into a work of art. And let me tell you, the journey to mastering heat input control is one that’s well worth the effort.
So, my fellow welding enthusiasts, remember: keep experimenting, stay curious, and never be afraid to ask for help. With a little practice and a whole lot of perseverance, you’ll be wielding that heat input like a true pro in no time.
And if you ever find yourself in need of some expert welding services, be sure to check out the team at Corrconnect. They’re the real deal when it comes to precision welding, custom fabrication, and all things metal-related.
Happy welding, my friends! May your beads be beautiful, your heat input be just right, and your skills continue to grow with each and every weld.