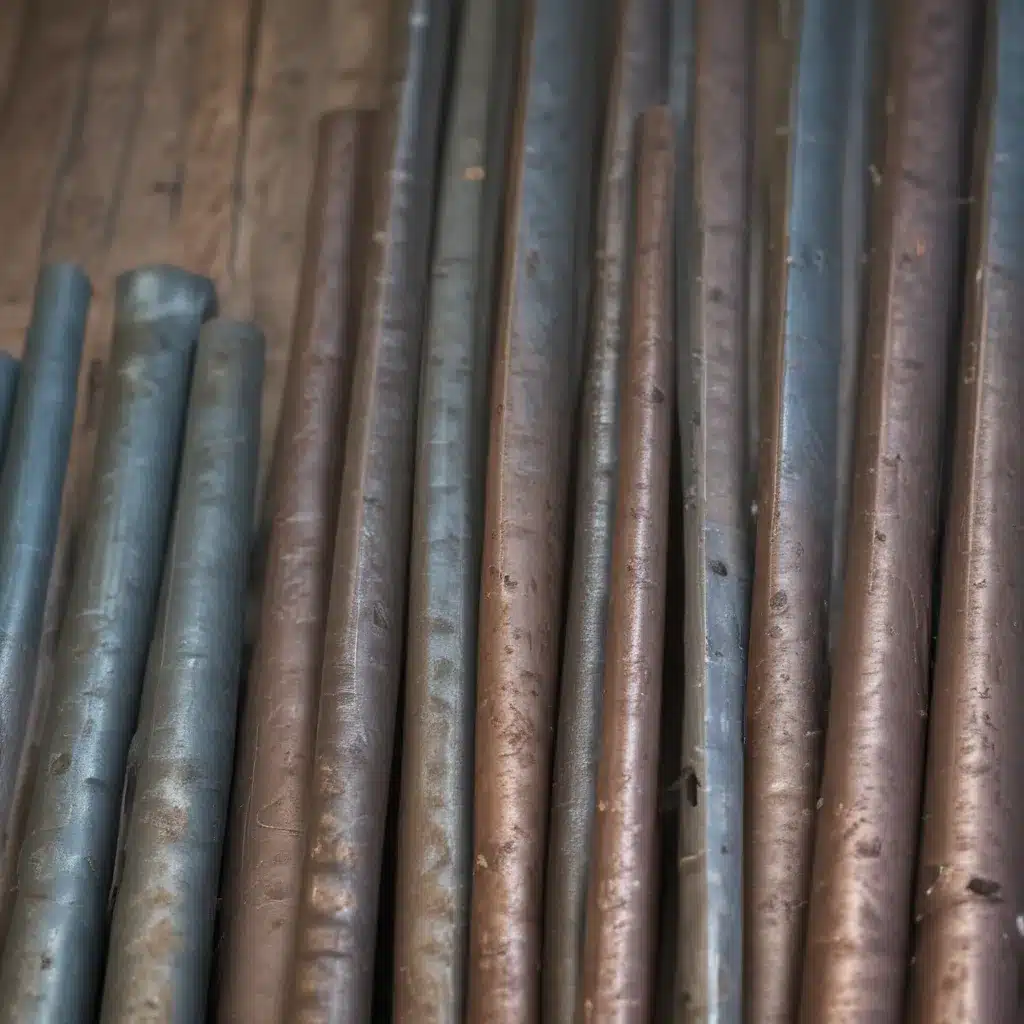
The Fundamentals of Welding Rods and Electrodes
As a seasoned welder, I’ve come to appreciate the intricate dance between the tools of my trade and the magic that unfolds when metal meets flame. And when it comes to the most essential players in this symphony of sparks, welding rods and electrodes reign supreme.
You see, the right choice of welding consumables can make all the difference between a flawless weld and a disastrous disaster. It’s like trying to bake the perfect cake with the wrong ingredients – the end result just won’t be up to snuff. That’s why I’m here to share my hard-earned wisdom on how to navigate the vast world of welding rods and electrodes, so you can wield your torch with confidence and precision.
Let’s start with the basics, shall we? At their core, welding rods and electrodes are the materials that provide the filler metal for your weld joint. They come in a dizzying array of compositions, each tailored to specific applications and metal types. And let me tell you, the wrong rod or electrode can turn your welding project into a hot, molten mess faster than you can say “flux-cored arc welding.”
But fear not, my fellow welding enthusiasts! I’m here to guide you through the ins and outs of choosing the right welding consumables for your needs. From understanding the importance of AWS classifications to mastering the art of electrode selection, we’ll cover it all. So, grab your safety gear and let’s dive in!
Deciphering the AWS Classification System
Alright, let’s start with the foundation of all things welding – the AWS (American Welding Society) classification system. This isn’t just some arbitrary alphabet soup; it’s a meticulously crafted code that holds the key to unlocking the perfect welding rod or electrode for your project.
Each welding consumable is assigned a unique AWS designation that provides a wealth of information about its chemical composition, mechanical properties, and intended use. It’s like a secret language that us welders have to learn, but trust me, once you crack the code, it’ll be a game-changer.
For example, let’s take a look at the AWS classification for a common mild steel electrode: E6010. The “E” stands for “electrode,” the “60” indicates the minimum tensile strength of the weld deposit in ksi (thousands of pounds per square inch), and the “10” denotes the electrode’s penetration and position capabilities.
But that’s just the tip of the iceberg! The AWS system goes much deeper, with additional digits and letters that provide even more detailed information about the electrode’s characteristics. It’s a veritable treasure trove of welding knowledge, and understanding how to decipher it is crucial for making the right choice.
So, next time you’re strolling down the welding supply aisle, don’t just grab the first rod or electrode that catches your eye. Take a moment to study the AWS classification and let it guide you to the perfect match for your project. Trust me, your welds will thank you.
Mastering Electrode Selection
Alright, now that we’ve got the AWS classification system under our belts, let’s dive deeper into the art of electrode selection. Because, let’s be real, with all the different types of electrodes out there, it can be a real head-scratcher trying to figure out which one to use.
First and foremost, you need to consider the base metal you’ll be working with. Are you welding mild steel, stainless steel, or something more exotic like aluminum or titanium? Each metal type has its own unique welding requirements, and the wrong electrode can lead to subpar results or even complete failure.
For example, if you’re working with mild steel, you’ll want to choose a low-hydrogen electrode, like the E7018, to minimize the risk of cracking and porosity. On the other hand, if you’re tackling stainless steel, you’ll need an electrode that can handle the higher heat input and provide corrosion resistance, like the E308 or E316.
But it’s not just the base metal that matters – the position of the weld is also a crucial factor. Are you welding in the flat, horizontal, or overhead position? Each weld position has its own set of challenges, and the electrode you choose needs to be able to handle the unique stresses and requirements.
Take the E6010 electrode I mentioned earlier. It’s a great all-arounder for welding in the flat and horizontal positions, but it might struggle with overhead welds due to its higher penetration and tendency to produce a more fluid weld pool. In that case, you might want to consider a lower-penetration electrode, like the E7018, to prevent the molten metal from sagging or dripping.
And let’s not forget about the coating on the electrode! The type of flux coating can have a significant impact on the welding characteristics, from the arc stability and penetration to the weld bead appearance and overall quality. It’s a veritable rabbit hole of options, but with a little practice and a lot of trial and error, you’ll be able to navigate the electrode maze like a pro.
So, the next time you’re faced with a welding project, don’t just grab the nearest electrode and hope for the best. Take the time to carefully consider the base metal, weld position, and the unique characteristics of each electrode type. It may take a bit of extra effort, but trust me, your welds will be all the better for it.
Exploring Specialized Welding Rods and Electrodes
Now, let’s venture into the realm of specialized welding rods and electrodes. Because, let’s be honest, sometimes the standard fare just won’t cut it. Whether you’re tackling a tricky material, a challenging weld joint, or a project that requires a certain level of precision, you might need to reach for something a little more, well, specialized.
Take, for example, the world of stainless steel welding. While the standard E308 and E316 electrodes are perfectly capable for most stainless steel applications, there are times when you might need something a bit more exotic. Maybe you’re working with a high-nickel alloy that requires a specific filler metal to maintain its corrosion resistance. Or perhaps you’re dealing with a thin-gauge stainless sheet that needs an electrode with a lower heat input to avoid distortion.
That’s where the specialized electrodes come into play. These babies are formulated to tackle the most demanding welding tasks, from exotic alloys to precision work. And let me tell you, they’re not your run-of-the-mill welding consumables.
Take the E312-16 electrode, for instance. This bad boy is designed for welding high-strength, high-alloy steels, like chrome-moly and nickel-chromium alloys. It’s got a special flux coating that helps it resist cracking and porosity, even in the most challenging weld positions. And the weld metal it produces? Stronger than a bodybuilder on steroids.
Or how about the E410NiMo-15 electrode? This stainless steel superstar is perfect for welding duplex and super-duplex stainless steels, which are becoming increasingly popular in industries like oil and gas, desalination, and chemical processing. The unique chemical composition of the weld metal helps to maintain the corrosion resistance and mechanical properties of these tricky-to-weld materials.
And let’s not forget about the specialized welding rods, either. These handy little guys come in a wide range of materials, from copper and aluminum to exotic alloys like titanium and inconel. They’re perfect for custom fabrication, precision welding, and other specialized applications where you need a filler metal that’s tailored to the task at hand.
So, the next time you’re faced with a welding challenge that has you scratching your head, don’t be afraid to venture into the world of specialized welding rods and electrodes. They may cost a little more, but the peace of mind and top-notch results they can provide are well worth the investment.
The Art of Precision Welding
Alright, let’s talk about the crème de la crème of welding – precision welding. Because, let’s face it, sometimes a little bit of slop just won’t cut it. Whether you’re working on a high-end fabrication project, repairing delicate machinery, or creating a work of art, precision welding is the name of the game.
And when it comes to precision welding, the choice of welding consumables is absolutely critical. You can’t just grab any old electrode and expect to achieve the level of control and accuracy you need. Nope, you’ve gotta dig deep into the welding consumables toolbox and pull out the big guns.
Enter the world of low-hydrogen, high-alloy electrodes. These babies are specifically designed to deliver precise, high-quality welds with minimal distortion and maximum control. We’re talking electrodes with a tightly controlled chemical composition, a meticulously engineered flux coating, and the ability to deliver a stable, smooth arc that’s a joy to behold.
Take the E308L-16 electrode, for example. This stainless steel superstar is perfect for precision welding applications where you need to maintain the integrity of the base metal. The low-carbon content in the weld metal helps to minimize the risk of sensitization and corrosion, while the carefully selected alloying elements ensure a strong, ductile weld that can stand up to the toughest of conditions.
But it’s not just the electrode composition that matters – the welding technique is equally important. Precision welding often requires a steady hand, a keen eye, and a deep understanding of the nuances of arc control. It’s a delicate dance, where the welder must carefully manipulate the arc length, travel speed, and electrode angle to achieve the perfect weld.
And let’s not forget about the importance of preheating and post-weld heat treatment. These crucial steps can mean the difference between a precision masterpiece and a hot, molten mess. Proper heat management is essential for minimizing distortion, maintaining the desired microstructure, and ensuring the weld’s long-term performance.
So, if you’re tackling a precision welding project, don’t go in half-cocked. Take the time to carefully select the right welding consumables, master the art of arc control, and pay close attention to the heat treatment process. It may take a bit more effort, but the end result will be a weld that’s as precise and beautiful as a Swiss watch.
Putting It All Together: Choosing the Right Welding Rods and Electrodes
Alright, folks, we’ve covered a lot of ground when it comes to welding rods and electrodes. From the fundamentals of the AWS classification system to the intricacies of specialized and precision welding, we’ve explored the ins and outs of these essential welding consumables.
But now, the big question – how do you actually choose the right welding rods and electrodes for your project? Well, my friends, it all comes down to a little thing I like to call the “Welding Consumables Tango.”
First, you’ve got to assess the base metal you’ll be working with. Is it mild steel, stainless steel, aluminum, or something more exotic? This is the foundation upon which you’ll build your welding consumables strategy.
Next, consider the weld joint and position. Are you working in the flat, horizontal, or overhead position? This will help you narrow down the electrodes that can handle the unique challenges of each weld orientation.
Then, take a close look at the AWS classification of the welding rods and electrodes. Decode that secret language and let it guide you to the perfect match for your project. Remember, the right AWS designation can mean the difference between a flawless weld and a hot mess.
But wait, there’s more! If you’re tackling a specialized or precision welding application, you may need to reach for the big guns – those high-performance, low-hydrogen, and high-alloy welding consumables. They may cost a little more, but the results they can deliver are well worth the investment.
And let’s not forget about the importance of proper heat management. Preheating and post-weld heat treatment can be crucial for maintaining the integrity of the weld and the surrounding base metal. It’s a delicate dance, but one that’s well worth mastering.
So, there you have it, folks – the secret to choosing the right welding rods and electrodes. It may seem like a lot to remember, but trust me, once you get the hang of it, it’ll become second nature. And the results? Well, let’s just say your welds will be the stuff of legend.
Now, go forth and wield your torch with confidence, my fellow welding enthusiasts! And if you ever need a little extra help or guidance, you know where to find me. Happy welding!