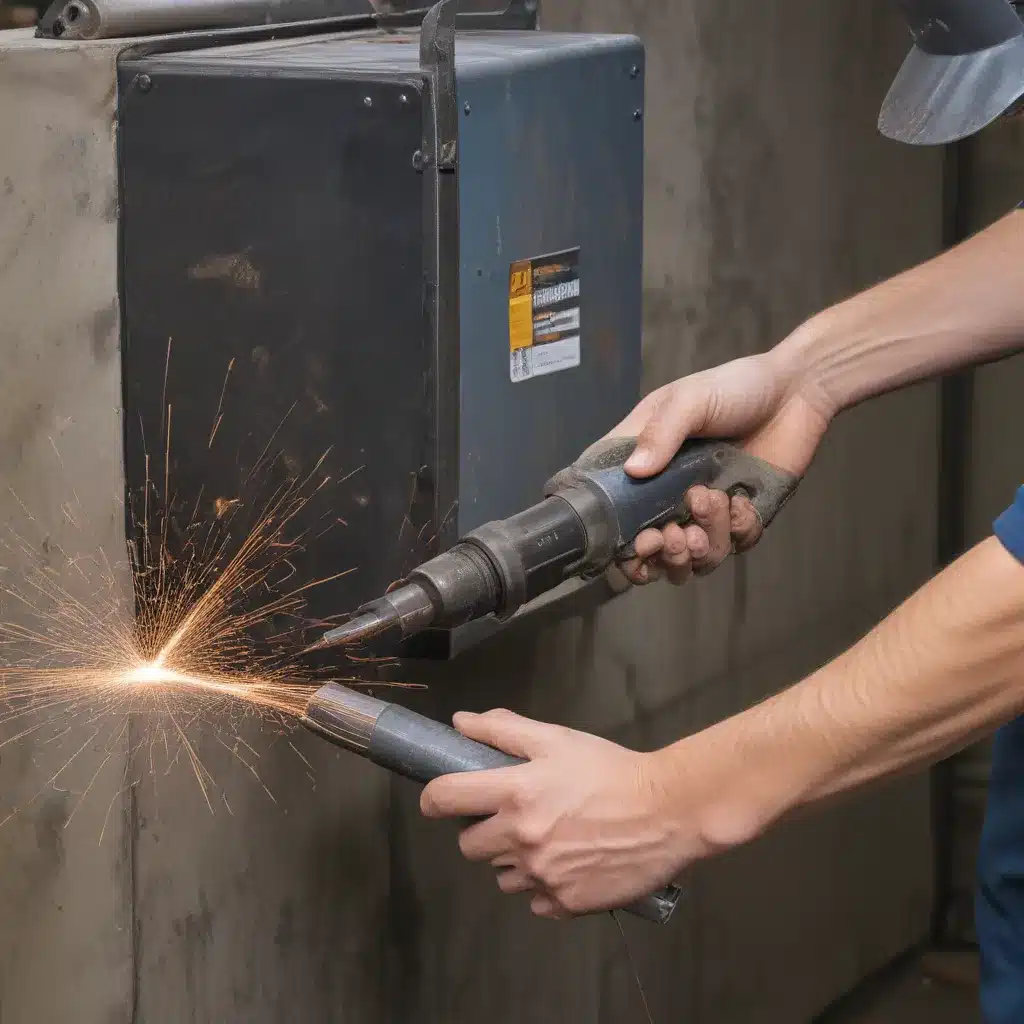
The Art of Spatter-Free Welding
As a seasoned welder, I’ve seen my fair share of welding projects, from intricate custom fabrications to large-scale metal cutting and precision welding services. Throughout my career, I’ve come to appreciate the importance of achieving clean, spatter-free welds – not only for the aesthetic appeal but also for the overall quality and durability of the final product.
In this in-depth article, I’ll share my tried-and-true tips and techniques for producing flawless, spatter-free welds using a spool gun. We’ll dive into the science behind weld spatter, explore the key factors that contribute to its formation, and uncover the secrets to mastering the art of clean welding. Whether you’re a beginner eager to hone your skills or a seasoned pro looking to refine your techniques, this guide has got you covered.
So, let’s get started on our journey to conquering weld spatter and unlocking the true potential of your spool gun!
Understanding the Causes of Weld Spatter
To effectively address the issue of weld spatter, we must first understand the underlying causes. Spatter, the pesky little beads of molten metal that scatter during the welding process, can be a real pain to deal with – both in terms of appearance and the potential for damage to surrounding areas.
The formation of weld spatter is a complex interplay of various factors, including the welding process, the characteristics of the base metal, and the settings on your spool gun. Let’s dive into each of these contributing elements:
The Welding Process
The type of welding process you’re using plays a significant role in the amount of spatter generated. For example, gas metal arc welding (GMAW), commonly known as MIG welding, is generally more prone to spatter than other welding techniques, such as shielded metal arc welding (SMAW) or flux-cored arc welding (FCAW). This is due to the inherent nature of the GMAW process, which utilizes a continuous wire feed and a shielding gas to protect the weld pool.
The settings on your spool gun, such as the wire feed speed, voltage, and gas flow rate, can also greatly impact the amount of spatter produced. Finding the right balance of these parameters is crucial for minimizing spatter and achieving clean, professional-looking welds.
The Base Metal
The composition and characteristics of the base metal you’re working with can also influence the formation of weld spatter. Metals with higher carbon content, such as certain types of steel, tend to be more susceptible to spatter. Additionally, the surface condition of the base metal, including any contaminants or oxides, can contribute to the spatter problem.
The Welding Technique
Your welding technique, including your stance, torch angle, and travel speed, can also play a role in the amount of spatter generated. Improper technique, such as a too-steep torch angle or an erratic travel speed, can disrupt the weld pool and lead to increased spatter.
Understanding these key factors that contribute to weld spatter is the first step in developing effective strategies to combat this common welding challenge.
Mastering the Spool Gun for Spatter-Free Welds
Now that we’ve explored the underlying causes of weld spatter, let’s dive into the specific techniques and best practices for using a spool gun to achieve clean, spatter-free welds.
Choosing the Right Spool Gun
The first step in your spatter-free welding journey is selecting the right spool gun for the job. Not all spool guns are created equal, and the one you choose can have a significant impact on the quality of your welds.
When shopping for a spool gun, look for features that are tailored to minimizing spatter, such as a smooth wire feed system, adjustable gas flow, and a well-designed contact tip. Investing in a high-quality spool gun from a reputable manufacturer can make a world of difference in your welding results.
Proper Spool Gun Setup and Maintenance
Ensuring your spool gun is properly set up and well-maintained is crucial for achieving spatter-free welds. Take the time to carefully adjust the wire feed tension, gas flow, and other settings to find the perfect balance for your specific welding application.
Regular maintenance, such as cleaning the contact tip, checking for wire feed issues, and replacing any worn components, can also go a long way in keeping your spool gun in top-notch condition and reducing the risk of weld spatter.
Perfecting Your Welding Technique
As we discussed earlier, your welding technique plays a significant role in the amount of spatter produced. When using a spool gun, focus on maintaining a consistent torch angle, travel speed, and weld pool control to minimize disruptions that can lead to spatter.
Experiment with different welding techniques, such as the “stickout” method, where you maintain a consistent distance between the contact tip and the base metal. This can help stabilize the weld pool and reduce spatter. Additionally, pay close attention to your body positioning and stance to ensure smooth, controlled movements throughout the welding process.
Shielding Gas Selection and Optimization
The type and flow rate of the shielding gas used in your spool gun welding setup can have a significant impact on spatter formation. Different gas mixtures, such as argon-based or carbon dioxide-based blends, can affect the weld pool fluidity and the overall stability of the arc.
Experiment with various gas options and flow rates to find the ideal combination that minimizes spatter and provides consistent, high-quality welds. Keep in mind that factors like base metal composition and welding position may also influence the optimal shielding gas setup.
Proper Cleaning and Preparation of Base Metal
As we mentioned earlier, the condition of the base metal can also contribute to weld spatter. Ensure that the surfaces you’re welding are thoroughly cleaned and free of any contaminants, such as rust, oil, or paint.
Take the time to properly prepare the base metal by grinding, brushing, or using a chemical cleaner to remove any surface impurities. This will help create a clean, uniform surface that is less prone to spatter during the welding process.
By mastering these spool gun-specific techniques and best practices, you’ll be well on your way to achieving consistently clean, spatter-free welds that will impress your clients and enhance the overall quality of your welding projects.
Troubleshooting Weld Spatter: Common Issues and Solutions
Even with the best techniques and preparation, you may still encounter the occasional bout of weld spatter. When this happens, it’s important to have a solid troubleshooting process in place to identify and address the root cause of the issue.
Excessive Wire Feed Speed
One of the most common culprits of weld spatter is an excessively high wire feed speed. When the wire is being fed into the weld pool too quickly, it can disrupt the stability of the arc and lead to spatter formation.
To remedy this, start by gradually reducing the wire feed speed and observe the results. Find the sweet spot where the wire feed is fast enough to maintain a stable arc without causing excessive spatter.
Incorrect Voltage Settings
Just as an overly high wire feed speed can contribute to spatter, improper voltage settings on your spool gun can also be a contributing factor. If the voltage is too low, the weld pool may become unstable, resulting in spatter. Conversely, if the voltage is too high, the arc may become erratic and cause spatter.
Experiment with adjusting the voltage, in small increments, to find the optimal setting for your specific welding application and base metal. Use a voltmeter to ensure you’re accurately measuring and adjusting the voltage.
Inadequate Shielding Gas Coverage
Insufficient or uneven shielding gas coverage can also lead to the formation of weld spatter. If the gas flow is too low or the gas coverage is disrupted, the weld pool may become exposed to the atmosphere, leading to oxidation and spatter.
Carefully monitor the gas flow rate and ensure that the gas coverage is consistent and uninterrupted throughout the welding process. Consider using a gas lens or adjusting the gas nozzle position to optimize the shielding gas coverage.
Contaminated Base Metal
As we discussed earlier, the condition of the base metal can have a significant impact on weld spatter. If the surface of the base metal is contaminated with oil, rust, or other impurities, it can disrupt the weld pool and lead to increased spatter.
Thoroughly clean and prepare the base metal before welding, using the appropriate methods for the specific contaminants present. This will help create a clean, uniform surface that is less prone to spatter.
Improper Welding Technique
Finally, issues with your welding technique, such as an inconsistent travel speed, erratic torch angle, or poor weld pool control, can also contribute to weld spatter.
Revisit the best practices for spool gun welding technique and make adjustments as needed. Practice your movements and focus on maintaining a consistent, controlled approach to the welding process.
By methodically working through these common spatter-related problems and implementing the appropriate solutions, you’ll be well on your way to achieving clean, spatter-free welds with your spool gun.
Case Study: Conquering Weld Spatter for a Complex Fabrication Project
To bring these principles to life, let’s explore a real-world case study that showcases how I used the techniques and strategies discussed in this article to tackle a challenging welding project with a notorious spatter problem.
The project in question involved the custom fabrication of a intricate stainless steel sculpture for a high-end art gallery. The client had very specific requirements, including a flawless, mirror-like finish on the welds – a tall order given the complex design and the inherent tendency of stainless steel to produce excessive spatter during welding.
When I first took on this project, I knew I would need to pull out all the stops to achieve the desired results. I began by carefully selecting a top-of-the-line spool gun that was specifically designed to minimize spatter, with features like a smooth wire feed system and an adjustable gas nozzle.
Next, I meticulously set up the spool gun, spending time fine-tuning the wire feed tension, voltage, and gas flow rate to find the perfect combination for the stainless steel base material. I also made sure to thoroughly clean and prepare the surfaces to be welded, removing any traces of contaminants that could contribute to spatter.
During the actual welding process, I focused on maintaining a steady, controlled technique. I experimented with different torch angles and travel speeds, ultimately settling on a “stickout” method that allowed me to keep the weld pool stable and prevent disruptions that could lead to spatter.
To my delight, the results were nothing short of spectacular. The welds were clean, uniform, and virtually free of any visible spatter – a testament to the effectiveness of the techniques I had mastered. The client was thrilled with the final product, and the sculpture was a resounding success at the gallery opening.
This case study serves as a prime example of how a deep understanding of the causes of weld spatter, combined with the right spool gun setup and welding techniques, can help you overcome even the most daunting welding challenges. By applying these principles to your own work, you too can elevate your welding skills and deliver flawless, spatter-free results.
Conclusion: Embrace the Spatter-Free Welding Lifestyle
As I reflect on my journey as a welder, I can confidently say that the ability to produce clean, spatter-free welds has been a game-changer in my career. Not only does it elevate the overall quality and appearance of my work, but it also saves me countless hours of post-weld cleanup and rework.
By mastering the techniques and strategies outlined in this comprehensive guide, you too can join the ranks of welders who have embraced the spatter-free welding lifestyle. Whether you’re tackling a complex custom fabrication project or performing routine metal cutting and precision welding services, the principles you’ve learned here will serve you well in consistently achieving exceptional results.
Remember, the key to success lies in understanding the underlying causes of weld spatter, selecting the right spool gun for the job, and honing your welding techniques to perfection. With patience, practice, and a commitment to continual improvement, you’ll be well on your way to becoming a master of spatter-free welding.
So, what are you waiting for? Grab your spool gun, put on your welding gear, and get ready to unlock the true potential of your welding skills. The path to clean, professional-looking welds starts here. Let’s get to work!