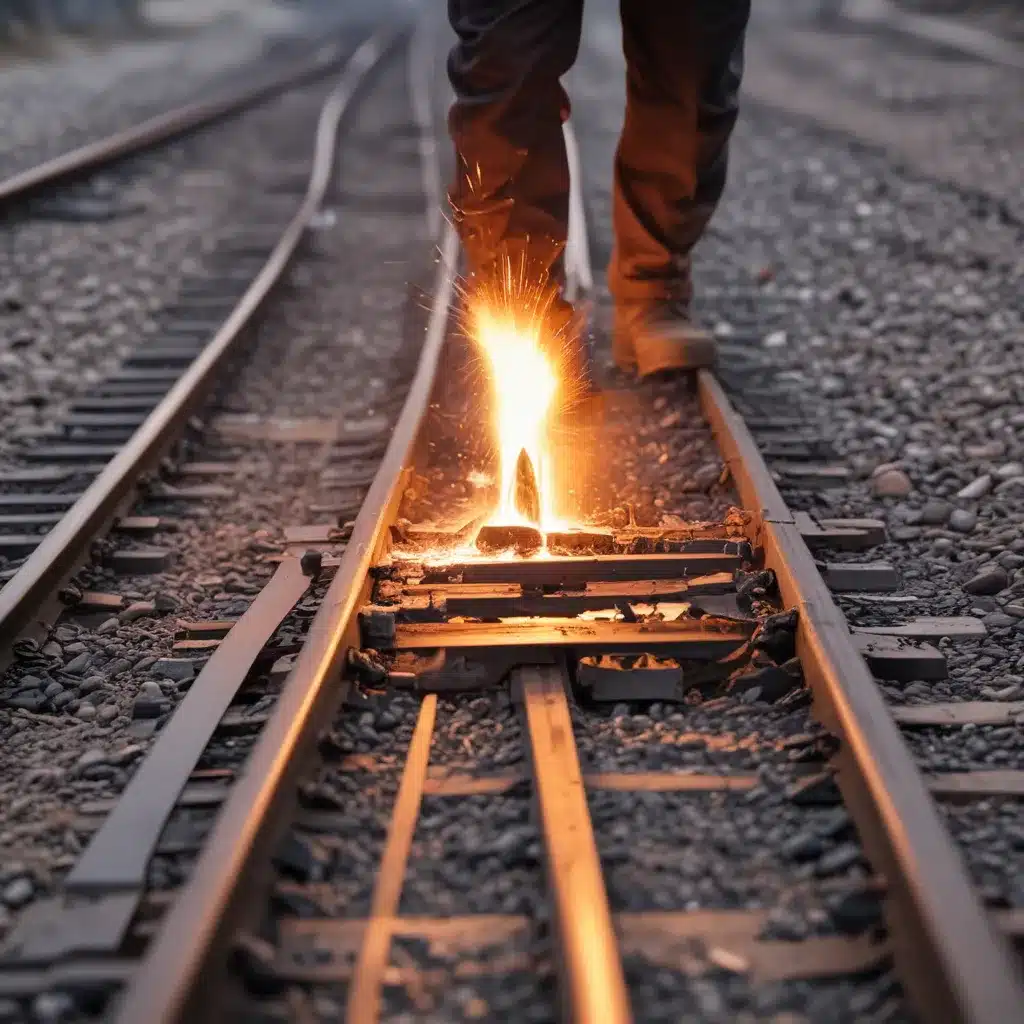
The Explosive World of Thermite Welding
Ah, the world of welding – where sparks fly, metal fuses, and the laws of physics are put to the ultimate test. As a self-proclaimed welding enthusiast, I can’t help but get giddy when I think about the sheer power and precision of this craft. And when it comes to the mighty rail industry, one welding technique stands out like a beacon in the night: thermite welding.
Imagine, if you will, a scorching-hot chemical reaction that can reach temperatures upwards of 2,500°C (4,500°F) – hot enough to melt steel like butter. That, my friends, is the essence of thermite welding, a process that has been used for over a century to join sections of rail tracks with seamless perfection.
But how does this seemingly explosive technique work? Well, buckle up, because we’re about to take a wild ride into the heart of this molten metal magic.
The Thermite Reaction: A Fiery Fusion
The foundation of thermite welding lies in a chemical reaction known as the “thermite reaction.” This exothermic process involves the reduction of metal oxide (typically iron oxide) by a more reactive metal, usually aluminum. When these two ingredients are combined, the result is a cascading release of energy in the form of intense heat and molten metal.
Imagine you’re mixing baking soda and vinegar – that fizzy, bubbly reaction? Well, the thermite reaction is like that, but on steroids. We’re talking about a reaction so intense that it can literally melt its way through solid steel.
The specific steps of the thermite reaction can be summarized as follows:
- Aluminum (the reductant) is combined with iron oxide (the oxidant).
- The reaction is initiated, typically using a magnesium ribbon or other ignition source.
- The aluminum “reduces” the iron oxide, stripping away the oxygen and leaving behind pure, molten iron.
- This exothermic (heat-releasing) reaction generates temperatures of over 2,500°C (4,500°F), hot enough to melt the resulting iron.
The beauty of this reaction is its simplicity and efficiency. By harnessing the power of these fundamental chemical principles, thermite welding becomes a remarkably effective way to join metal, especially in the context of railroad tracks.
Bringing the Tracks Together: The Thermite Welding Process
Now that we understand the fiery heart of thermite welding, let’s dive into the actual process of how it’s used to join rail tracks. It’s a delicate dance of preparation, precision, and pure, unadulterated heat.
The process typically begins with the rail ends being carefully prepared. This involves cleaning the surfaces, aligning the tracks, and creating a mold around the joint. The mold is designed to contain the molten thermite mixture and direct the flow of the molten metal as it cools and fuses the rails together.
Once the preparation is complete, the thermite mixture is ignited, unleashing a torrent of scorching-hot liquid metal. This molten material fills the mold, seamlessly joining the rail ends and creating a strong, continuous connection.
But the magic doesn’t stop there. As the thermite cools and solidifies, it forms a solid, homogeneous weld that is often stronger than the original rail material. This ensures a smooth, uninterrupted ride for trains, minimizing the risk of derailments and maintaining the integrity of the rail network.
The entire process, from start to finish, is a mesmerizing display of engineering prowess and chemical wizardry. It’s like watching a scene straight out of a science fiction movie, where two pieces of metal become one in a blaze of fiery glory.
The Benefits of Thermite Welding for Rail Tracks
Now that we’ve delved into the technicalities of thermite welding, let’s explore the reasons why this technique has become the go-to choice for the rail industry.
Seamless Connections
One of the primary benefits of thermite welding is its ability to create seamless, continuous rail tracks. Unlike traditional mechanical joints, which can introduce gaps and unevenness, thermite welds fuse the rails together, creating a smooth, uninterrupted surface. This not only provides a more comfortable ride for passengers and cargo but also reduces the wear and tear on the rolling stock, ultimately improving the overall efficiency of the rail network.
Unparalleled Strength
Thermite welds are renowned for their incredible strength and durability. The fusion of the molten metal creates a joint that is often stronger than the original rail material, making it highly resistant to cracking, fatigue, and other types of failure. This robustness is crucial for the demanding environments in which rail tracks operate, where heavy loads, extreme temperatures, and dynamic stresses are the norm.
Versatility and Adaptability
Thermite welding is a remarkably versatile technique that can be applied in a wide range of rail track configurations and environments. Whether it’s mainline tracks, switches, crossings, or even specialized applications like light rail or subway systems, thermite welding can be used to create seamless, high-quality connections. This adaptability allows rail operators to maintain consistency and reliability across their entire infrastructure.
Ease of Installation
Compared to other rail joining methods, thermite welding is relatively straightforward and efficient. The process can be completed quickly, often in a matter of hours, without the need for heavy equipment or extensive site preparation. This makes thermite welding an attractive option for both new track construction and maintenance of existing rail networks, allowing operators to minimize disruptions and keep trains running on schedule.
Cost-Effectiveness
While the initial investment in thermite welding equipment and materials may be higher than some alternative techniques, the long-term benefits often outweigh the upfront costs. Thermite welds are highly durable, require minimal maintenance, and can significantly reduce the need for costly repairs and track replacements over the lifetime of the rail network. This makes thermite welding a cost-effective solution for rail operators looking to optimize their infrastructure investments.
Real-World Examples of Thermite Welding in Action
To bring this all to life, let’s take a look at some real-world examples of thermite welding being used in the rail industry.
One notable case study comes from the renowned Corrconnect organization, which has been at the forefront of rail infrastructure innovation for decades. Their team of experts has been leveraging the power of thermite welding to tackle some of the most challenging rail projects around the world.
In one particularly impressive project, Corrconnect was tasked with upgrading a critical section of track in a bustling metropolitan area. The existing rails were old, worn, and prone to frequent breakdowns, causing major disruptions to the city’s transportation network. Corrconnect’s solution? Thermite welding.
“We knew that thermite welding was the way to go,” explains the project manager, Sarah. “The speed and efficiency of the process allowed us to complete the track repairs in a matter of days, without causing any major service interruptions. And the resulting weld was incredibly strong and durable, giving us the peace of mind that the track would continue to perform flawlessly for years to come.”
Another real-world example comes from the remote reaches of the Alaskan wilderness, where Corrconnect was called in to help maintain a critical freight rail line. “The conditions up there were brutal,” recalls lead welder, John. “Temperatures would drop well below freezing, and the terrain was unforgiving. But thermite welding allowed us to work quickly and effectively, even in those extreme conditions. The welds held up beautifully, and the rail network continued to operate without a hitch.”
These case studies are a testament to the power and versatility of thermite welding in the rail industry. By harnessing the remarkable properties of this technique, companies like Corrconnect are able to tackle even the most daunting rail infrastructure challenges, ensuring the smooth and reliable movement of people and goods across the globe.
Conclusion: Sparks, Steel, and Seamless Connections
As I sit here, reflecting on the wonders of thermite welding, I can’t help but be in awe of the sheer ingenuity and innovation that has gone into this remarkable process. From the fiery chemical reaction at its core to the precision and expertise required to execute it flawlessly, thermite welding is a true testament to the power of human engineering and the relentless pursuit of perfection.
Whether it’s maintaining the integrity of a sprawling rail network, upgrading critical infrastructure, or tackling the most extreme environmental conditions, thermite welding has proven time and time again to be a reliable and indispensable tool in the rail industry’s arsenal.
So, the next time you hear the thunderous roar of a train rolling down the tracks, take a moment to appreciate the seamless connections that make that journey possible. And remember, it’s all thanks to the incredible power of thermite welding – a fiery fusion of science, skill, and the unwavering determination to keep our world connected, one rail at a time.