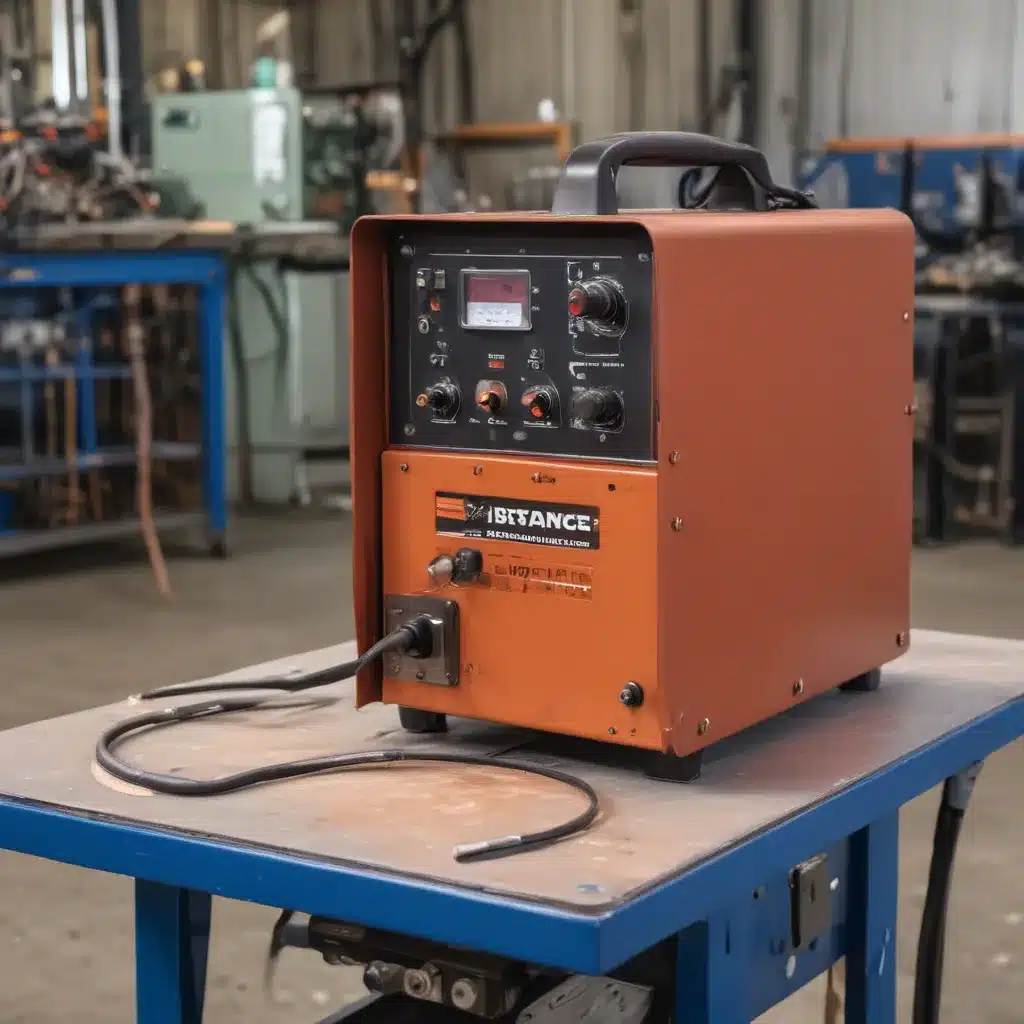
Understanding the Principles of Resistance Spot Welding
Ah, the mysterious world of resistance spot welding! It’s like a secret handshake that only the metal-bending, spark-flying, spartan warriors among us can truly appreciate. But fear not, my friends, for today I’m going to pull back the curtain and reveal the inner workings of these fascinating machines.
Let’s start with the basics, shall we? Resistance spot welding is a joining technique where two or more metal sheets are fused together by the heat generated from the electrical resistance between the parts. It’s a bit like rubbing your hands together really fast – the friction creates heat, and before you know it, you’ve got a toasty little bond going on.
The Key Components of a Resistance Spot Welding Machine
Now, to really understand how these machines work, we need to dive into the key components that make the magic happen. First and foremost, you’ve got your electrodes – these are the metal tips that come into direct contact with the workpieces, delivering the electrical current that’s the lifeblood of the process.
Next up, we have the transformer, which is responsible for stepping down the high-voltage, low-current electrical supply into a low-voltage, high-current output that’s perfect for the welding process. Think of it like a superhero sidekick, taking the raw power and making it just right for the job at hand.
And let’s not forget the control system, the brains of the operation that regulates the timing, current, and force of the welding cycle. It’s like the conductor of the orchestra, making sure each instrument (or component) plays its part in perfect harmony.
The Welding Cycle in Action
Now that we’ve got the key players introduced, let’s dive into the nitty-gritty of how the welding cycle actually works. It all starts with the electrodes clamping down on the metal sheets, applying a carefully controlled force to ensure a solid, even contact.
As the current flows through the electrodes and into the workpieces, the resistance between the metal layers causes the temperature to skyrocket – we’re talking up to 2,500°C (4,500°F) in just a few milliseconds! This intense heat is localized to the area between the electrodes, creating a molten pool that fuses the layers together.
But the fun doesn’t stop there, oh no. The control system then cuts off the current, allowing the molten metal to solidify and form a strong, permanent bond. And just like that, you’ve got yourself a shiny new spot weld, ready to stand the test of time (or at least the rigors of your latest metalworking project).
Optimizing the Welding Process
Of course, as with any complex process, there are countless variables to consider when it comes to getting the perfect resistance spot weld. Things like the thickness and type of metal, the electrode geometry, the clamping force, and the timing of the current application can all have a major impact on the final result.
That’s why the best welding professionals are true alchemists, constantly experimenting and fine-tuning their techniques to achieve the optimal balance of strength, aesthetics, and efficiency. It’s a delicate dance, but when you nail it, the results can be nothing short of engineering poetry.
Take, for example, the case of our friends over at Corr Connect. They’ve been honing their resistance spot welding skills for years, tackling everything from thin-gauge automotive parts to heavy-duty industrial components. And let me tell you, the way they can coax a beautiful, high-quality weld out of even the most stubborn materials is nothing short of magical.
The Future of Resistance Spot Welding
But the story doesn’t end there, my friends. As with any technology, resistance spot welding is constantly evolving, with researchers and engineers pushing the boundaries of what’s possible. From the development of new electrode materials to the integration of advanced control systems, the future of this joining technique is looking brighter than ever.
Imagine a world where robots can effortlessly weld complex assemblies with lightning-fast precision, or where AI-powered systems can optimize the welding parameters in real-time to ensure consistent, high-quality results. It’s a future that’s already starting to take shape, and I can’t wait to see what the next generation of welding wizards will come up with.
So, there you have it – the inner workings of the mighty resistance spot welding machine, laid bare for all to see. Whether you’re a seasoned pro or a curious newcomer to the world of metalworking, I hope this deep dive has given you a newfound appreciation for the science and art of this essential joining technique.
Now, if you’ll excuse me, I’ve got some sparks to chase and some metals to fuse. It’s all in a day’s work for this welding warrior!