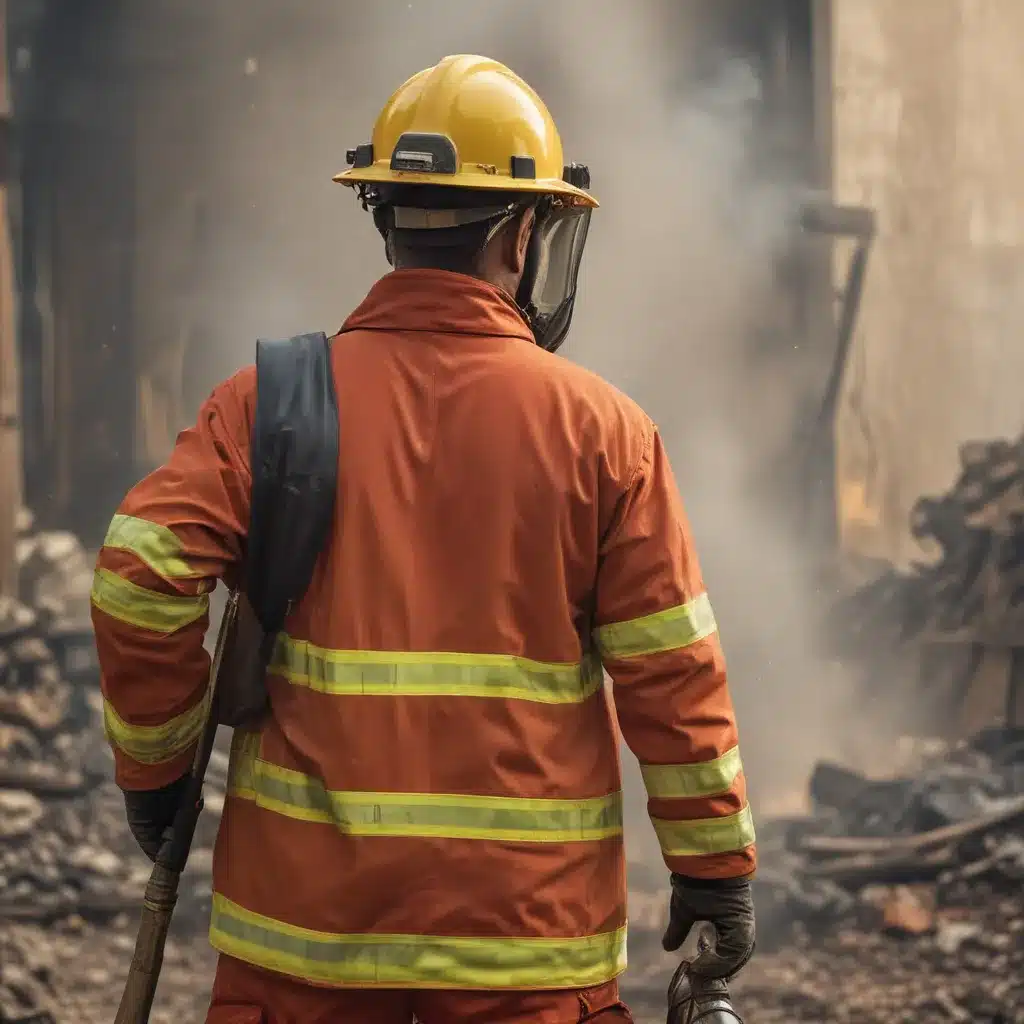
The Sizzling Scourge of Sparks and Flames
You know, I’ve always been fascinated by the sheer power of fire – that mesmerizing dance of flames, the hypnotic crackle of the hearth. But when it comes to our line of work, fire is no laughing matter. As a welding and metal fabrication professional, I’ve seen my fair share of close calls with those pesky little sparks and rogue embers. That’s why understanding the importance of hot work permits is absolutely crucial for keeping our operations – and our team – safe and sound.
Let me paint you a picture: You’re in the middle of a big custom fabrication project, sparks flying left and right as your welder works its magic on a giant steel frame. Everything is going smoothly, and then suddenly, you spot a wisp of smoke drifting up from a dark corner of the workshop. Your heart drops – a fire? Oh no, not on my watch! Cue the mad dash for the fire extinguisher and the mad scramble to evacuate the area. Talk about a heart-pounding moment, am I right?
Luckily, that particular incident ended without any major damage, but I’ll never forget the sheer panic and adrenaline rush. That’s why, from that day on, I made it my mission to really dive deep into the world of hot work permits and fire prevention. After all, an ounce of prevention is worth a pound of cure, as they say. And let me tell you, what I’ve learned has been absolutely invaluable for keeping our welding and fabrication business running smoothly and safely.
Understanding the Importance of Hot Work Permits
So, what exactly is a hot work permit, you ask? In the simplest terms, it’s a document that outlines the safety precautions and procedures that must be followed when performing any type of “hot work” – activities that involve open flames, sparks, or other heat sources that could potentially ignite a fire. This includes everything from welding and cutting to soldering, brazing, and even some types of grinding and abrasive work.
The purpose of a hot work permit is to identify and mitigate the fire hazards associated with these high-risk activities. By requiring workers to obtain a permit before starting a job, it ensures that they’ve taken the necessary steps to assess the work area, remove or protect combustible materials, and have the proper fire extinguishing equipment on hand. It’s essentially a way to put a safety net in place and prevent those small sparks from turning into a raging inferno.
But why is this so important, you might be wondering? Well, the statistics speak for themselves. According to the National Fire Protection Association (NFPA), hot work activities are responsible for a significant percentage of all reported structure fires in the United States each year. And these aren’t just small, contained incidents – we’re talking about major blazes that can cause extensive damage, disrupt operations, and even result in serious injuries or loss of life.
Just imagine the nightmare scenario: You’re in the middle of a critical welding project, and suddenly, the workshop is engulfed in flames. Hundreds of thousands of dollars’ worth of equipment and inventory gone up in smoke, not to mention the potential for catastrophic harm to your employees and the surrounding community. It’s a sobering thought, but one that underscores the vital importance of hot work permits and fire prevention protocols.
Navigating the Hot Work Permit Process
Okay, so we’ve established that hot work permits are a non-negotiable when it comes to keeping our welding and fabrication operations safe and secure. But what exactly does the process involve? Let me break it down for you.
First and foremost, it’s crucial to understand the specific requirements and regulations in your local area. Hot work permit protocols can vary widely depending on your geographic location, industry, and the nature of your business. Some jurisdictions may have strict permitting requirements, while others may have more lax guidelines. It’s your responsibility as the business owner or manager to familiarize yourself with the applicable rules and ensure your team is fully compliant.
In general, though, the hot work permit process typically involves the following key steps:
-
Hazard Assessment: Before any hot work can commence, a thorough inspection of the work area must be conducted to identify potential fire hazards. This includes checking for the presence of flammable materials, combustible dust, or any other conditions that could fuel a fire.
-
Preparation and Protection: Based on the findings of the hazard assessment, appropriate steps must be taken to remove or protect any combustible items in the vicinity. This may involve moving or covering up materials, installing fire-resistant barriers, or implementing other control measures.
-
Fire Watch: Throughout the duration of the hot work, a dedicated fire watch must be in place to monitor the area and be ready to respond quickly in the event of an incident. This individual is responsible for having the proper fire extinguishing equipment on hand and being trained in its use.
-
Permit Approval: Once all the necessary precautions have been taken, the hot work permit can be issued by the designated authority – typically a facilities manager, safety coordinator, or fire marshal. This document outlines the specific work to be performed, the required safety measures, and the time frame for which the permit is valid.
-
Ongoing Monitoring: Even after the hot work is completed, the area must be continuously monitored for at least 30 minutes (and sometimes longer) to ensure there are no lingering fire risks. This is a critical step, as many fires can take time to develop and may not be immediately visible.
Now, I know what you’re thinking – that’s a lot of hoops to jump through, right? And you’d be absolutely right. Navigating the hot work permit process can be a logistical nightmare, especially for smaller welding and fabrication shops that may not have dedicated safety personnel or extensive resources.
But let me tell you, it’s a small price to pay for the peace of mind and protection it provides. And trust me, it’s a lot less stressful than dealing with the aftermath of a full-blown fire. As the old saying goes, an ounce of prevention is worth a pound of cure. And when it comes to hot work and fire safety, that couldn’t be more true.
Real-World Lessons: Case Studies in Hot Work Permit Compliance
Of course, the importance of hot work permits isn’t just some abstract concept – it’s a very real, tangible issue that businesses in our industry face every single day. And to really drive the point home, let me share a couple of real-world case studies that illustrate just how crucial it is to have a robust hot work permit system in place.
Case Study #1: The Welding Workshop Inferno
A few years back, I heard about a devastating fire that tore through a small welding and metal fabrication shop in a neighboring town. The details were truly harrowing – the blaze started when a welder accidentally ignited some nearby combustible materials, and it quickly spread out of control, engulfing the entire building in flames.
By the time the firefighters arrived, the workshop was already a total loss. Tens of thousands of dollars’ worth of equipment, tooling, and finished products were reduced to smoldering piles of twisted metal and ash. But the real tragedy was the human toll – two workers suffered severe burns, and one didn’t make it. The business owner was absolutely devastated, not just by the financial implications, but by the lives lost due to a preventable incident.
The subsequent investigation revealed that the company had been operating without a proper hot work permit system in place. There were no designated fire watches, no fire extinguishers readily available, and no clear protocols for assessing and mitigating fire hazards. It was a disaster waiting to happen, and unfortunately, it did.
Case Study #2: The Precision Welding Scare
On the flip side, I’ve also witnessed firsthand the importance of hot work permits in preventing disastrous fires. A few years ago, our precision welding team was working on a high-stakes project for a major aerospace client. The tolerances were razor-thin, and the stakes were sky-high – we couldn’t afford even the slightest mistake or mishap.
As part of our standard operating procedures, we had a comprehensive hot work permit system in place. Before the welding even began, our safety coordinator conducted a thorough inspection of the work area, identified all potential fire risks, and implemented the necessary control measures. We had fire extinguishers at the ready, a dedicated fire watch on duty, and a clear evacuation plan in case of emergency.
Thankfully, we didn’t end up needing to put those emergency protocols into action. But during one particularly intense welding session, a small spark did manage to land on a nearby workbench, igniting a small pile of cardboard. Our vigilant fire watch immediately sprang into action, quickly extinguishing the flames before they could spread. Thanks to our hot work permit system, we were able to nip that potential disaster in the bud and keep the project on track without any interruptions.
The contrast between these two case studies is stark, but it really hammers home the importance of hot work permits and fire prevention measures. In the first scenario, the lack of proper protocols resulted in a devastating outcome. In the second, our proactive approach allowed us to avert a crisis and keep our operations running smoothly. It’s a testament to the power of preparation and the simple fact that an ounce of prevention is indeed worth a pound of cure.
Putting Hot Work Permits into Practice: Tips and Strategies
Okay, so we’ve covered the why – now let’s dive into the how. As a welding and fabrication professional, how can you effectively implement a hot work permit system in your own business? Here are a few key tips and strategies to consider:
Establish Clear Policies and Procedures
The foundation of any successful hot work permit program is a set of well-defined, comprehensive policies and procedures. These should cover everything from the specific steps for obtaining a permit to the roles and responsibilities of key personnel. Make sure these guidelines are easily accessible and understood by your entire team.
Invest in Proper Training
Speaking of your team, it’s crucial that everyone involved in hot work activities is properly trained on the hot work permit process and fire safety protocols. This includes not just your welders and fabricators, but also your supervisors, facilities managers, and even office staff who may need to be involved in the permitting process.
Designate Responsible Parties
Identify the specific individuals within your organization who will be responsible for overseeing the hot work permit system. This might include a safety coordinator, a facilities manager, or even a designated “fire watch” who will be solely responsible for monitoring the work area during high-risk activities.
Conduct Regular Audits and Inspections
Don’t just set it and forget it – make sure to regularly review and update your hot work permit policies and procedures. Conduct periodic audits of your work sites, assess the effectiveness of your control measures, and make any necessary adjustments to keep your team and your business safe.
Leverage Technology and Automation
In today’s digital age, there are all sorts of tools and technologies that can help streamline and optimize the hot work permit process. Consider investing in software or online platforms that can automate aspects of the paperwork, tracking, and record-keeping involved.
Foster a Culture of Safety
At the end of the day, the success of your hot work permit system ultimately comes down to the attitudes and behaviors of your team. Foster a strong culture of safety and fire prevention, where everyone understands the importance of following proper protocols and looking out for potential hazards.
Remember, when it comes to hot work and fire safety, there’s no room for complacency. It’s a constant, vigilant effort that requires the full commitment and participation of your entire organization. But trust me, the peace of mind and protection it provides is more than worth the investment.
Conclusion: Embracing Hot Work Permits for a Safer, Stronger Business
As I reflect on my journey in the welding and fabrication industry, I can honestly say that mastering the world of hot work permits has been one of the most impactful and rewarding experiences of my career. It’s a topic that may not be the most glamorous or exciting, but its importance simply can’t be overstated.
Think about it – the ability to proactively identify and mitigate fire hazards, to have a plan in place for responding to emergencies, and to cultivate a culture of safety and vigilance within your organization. That’s the kind of competitive edge that can truly set your business apart and help you thrive in this fast-paced, high-stakes industry.
And let’s be real – the alternative is just not worth thinking about. The threat of a devastating fire, the potential for catastrophic damage and disruption, the unthinkable human toll. It’s enough to keep any business owner up at night. But with a robust hot work permit system in place, you can rest easy, knowing that you’ve done everything in your power to protect your team, your assets, and your hard-earned reputation.
So, my fellow welding and fabrication professionals, I urge you – don’t wait until it’s too late. Dive headfirst into the world of hot work permits, learn the ropes, and make it a cornerstone of your overall safety and risk management strategy. Trust me, your future self (and your insurance provider) will thank you.
Remember, we’re not just building metal masterpieces here – we’re crafting the very foundations of our communities, one weld and one custom fabrication at a time. And with hot work permits as our trusty sidekick, we can do it all while keeping our teams and our businesses safe, secure, and poised for long-term success.
So, let’s embrace the sizzle and the spark, my friends. But let’s do it smartly, strategically, and with the utmost care and attention to fire prevention. After all, the only thing hotter than our welding torches should be our passion for keeping our operations and our people out of harm’s way.