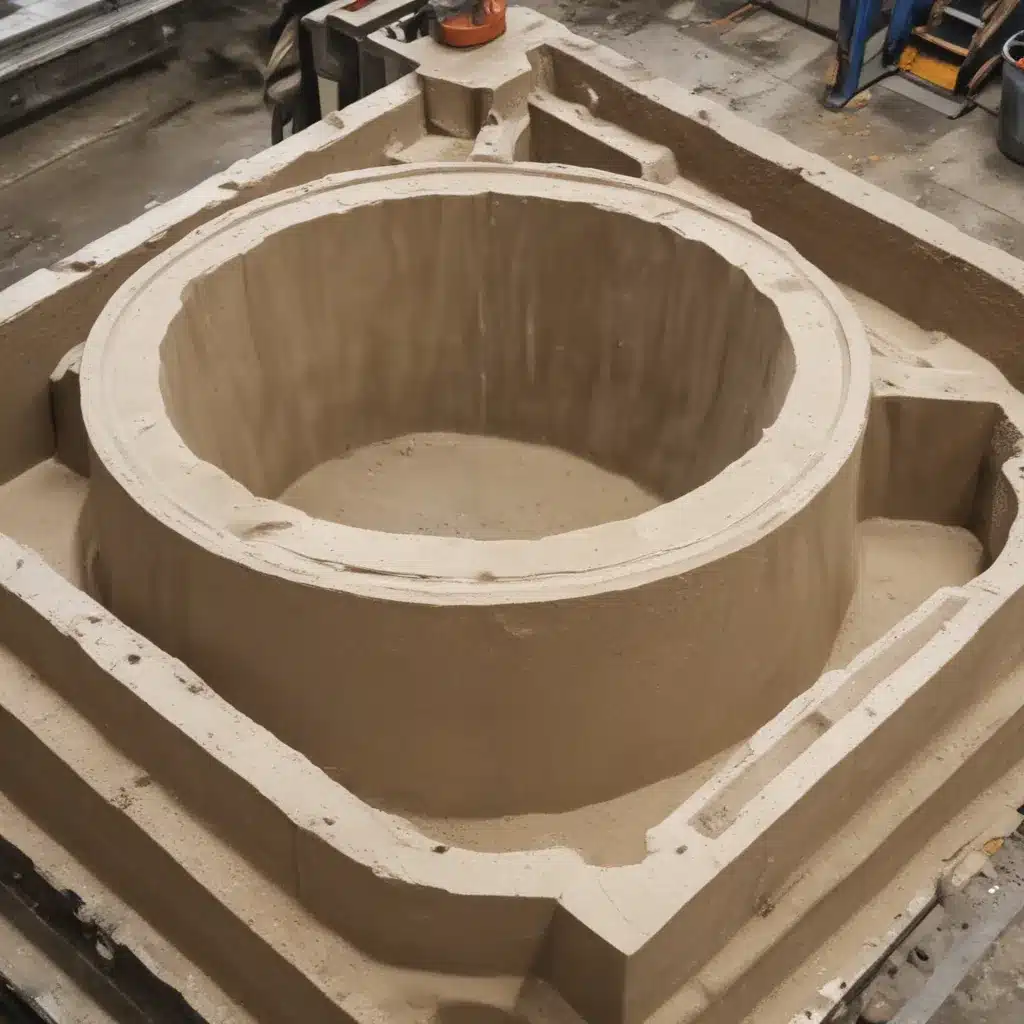
The Humble Beginnings of Sand Casting
Ah, sand casting – the unsung hero of the metal fabrication world. It may not have the flashy appeal of modern 3D printing or the precision of CNC machining, but this time-honored technique has been shaping the world around us for centuries. Let me take you on a journey through the evolution of sand casting, from its humble beginnings to the cutting-edge advancements that are revolutionizing the industry.
Picture this: it’s the dawn of civilization, and our enterprising ancestors are tinkering with primitive metal-working techniques. They stumble upon the wonders of sand casting, a method that allows them to create intricate shapes and forms by pouring molten metal into a mold carved out of sand. Sure, it may have been a bit rough around the edges, but this simple yet ingenious process laid the foundation for countless innovations to come.
As the centuries passed, sand casting continued to evolve, adapting to the changing needs of industry and technology. Craftsmen honed their skills, experimenting with different sand compositions and mold-making techniques to produce ever-more complex and precise castings. The introduction of mechanized equipment revolutionized the process, allowing for larger and more sophisticated parts to be produced with greater efficiency.
The Modern Sand Casting Landscape
Today, sand casting remains a crucial part of the global manufacturing landscape. From automotive components to architectural fixtures, this versatile technique is used to create a wide variety of products that shape our everyday lives. But what makes sand casting so indispensable in the modern era? Let’s dive deeper into the advantages and advancements that have cemented its place in the industry.
One of the key benefits of sand casting is its ability to handle a diverse range of materials. Whether you’re working with aluminum, steel, or even exotic alloys, the sand casting process can be adapted to accommodate a variety of metal compositions. This flexibility allows manufacturers to tackle a wide range of projects, from high-volume production to custom one-off pieces.
But it’s not just the material selection that makes sand casting a powerhouse – it’s the sheer complexity of the parts that can be produced. With the help of advanced computer-aided design (CAD) software and 3D printing technology, sand casting molds can now be created with unprecedented levels of detail and intricate geometries. This opens up a world of possibilities for designers and engineers, who can now bring their most ambitious visions to life.
The Rise of Precision Sand Casting
As the demand for high-quality, precision-engineered components continues to grow, the sand casting industry has responded with a wave of cutting-edge advancements. Enter the realm of precision sand casting, where the traditional process has been refined and optimized to meet the stringent requirements of modern manufacturing.
One of the standout developments in this area is the use of advanced simulation software. By modeling the entire sand casting process, from mold filling to solidification, these powerful tools allow manufacturers to identify and address potential issues before a single part is ever produced. This not only improves the overall quality and consistency of the castings, but it also dramatically reduces the time and resources required to bring a new product to market.
But the innovations don’t stop there. Sand casting facilities have also invested heavily in state-of-the-art equipment and quality control measures to ensure the highest levels of accuracy and repeatability. Advanced mold-making techniques, such as the use of 3D-printed patterns and robotic automation, have further streamlined the production process, while rigorous testing and inspection protocols guarantee that every casting meets the most stringent specifications.
Precision Welding: The Perfect Complement to Sand Casting
As the sand casting industry continues to push the boundaries of what’s possible, it has found a natural ally in the world of precision welding. By seamlessly integrating these two complementary processes, manufacturers are able to unlock a new level of versatility and capability in their operations.
Precision welding, with its unparalleled control and repeatability, is the ideal partner for high-quality sand castings. Whether it’s joining complex components, repairing defects, or adding specialized features, the skilled application of welding techniques can transform a good casting into a truly exceptional product.
At [Company Name], we’ve harnessed the power of precision welding to elevate our sand casting services to new heights. Our team of experienced welding professionals work hand-in-hand with our casting experts to ensure that every project, from custom fabrication to intricate architectural elements, meets the most demanding standards of quality and performance.
Pushing the Boundaries of Possibility
As I reflect on the evolution of sand casting, I’m struck by the sheer ingenuity and determination of the individuals who have driven this industry forward. From the early pioneers who first experimented with molten metal and sand, to the modern-day innovators who are redefining the boundaries of what’s possible, the story of sand casting is one of resilience, innovation, and a relentless pursuit of excellence.
And the journey is far from over. As the world continues to demand more complex, high-performance components, the sand casting industry is rising to the challenge with a host of exciting new developments. Advancements in materials science, automation, and quality control are paving the way for unprecedented levels of precision and efficiency.
At [Company Name], we’re proud to be at the forefront of this revolution. Our state-of-the-art sand casting facilities, equipped with the latest technology and staffed by a team of skilled professionals, are redefining what’s possible in the world of metal fabrication. Whether you’re in need of custom-engineered parts, precision-welded assemblies, or complex architectural features, we have the expertise and the resources to bring your vision to life.
So, what’s next for the world of sand casting? The possibilities are truly limitless. As we continue to push the boundaries of what’s possible, I can’t help but feel a sense of excitement and wonder at the incredible feats that lie ahead. The future is bright, and it’s all coming together at the core of sand casting.