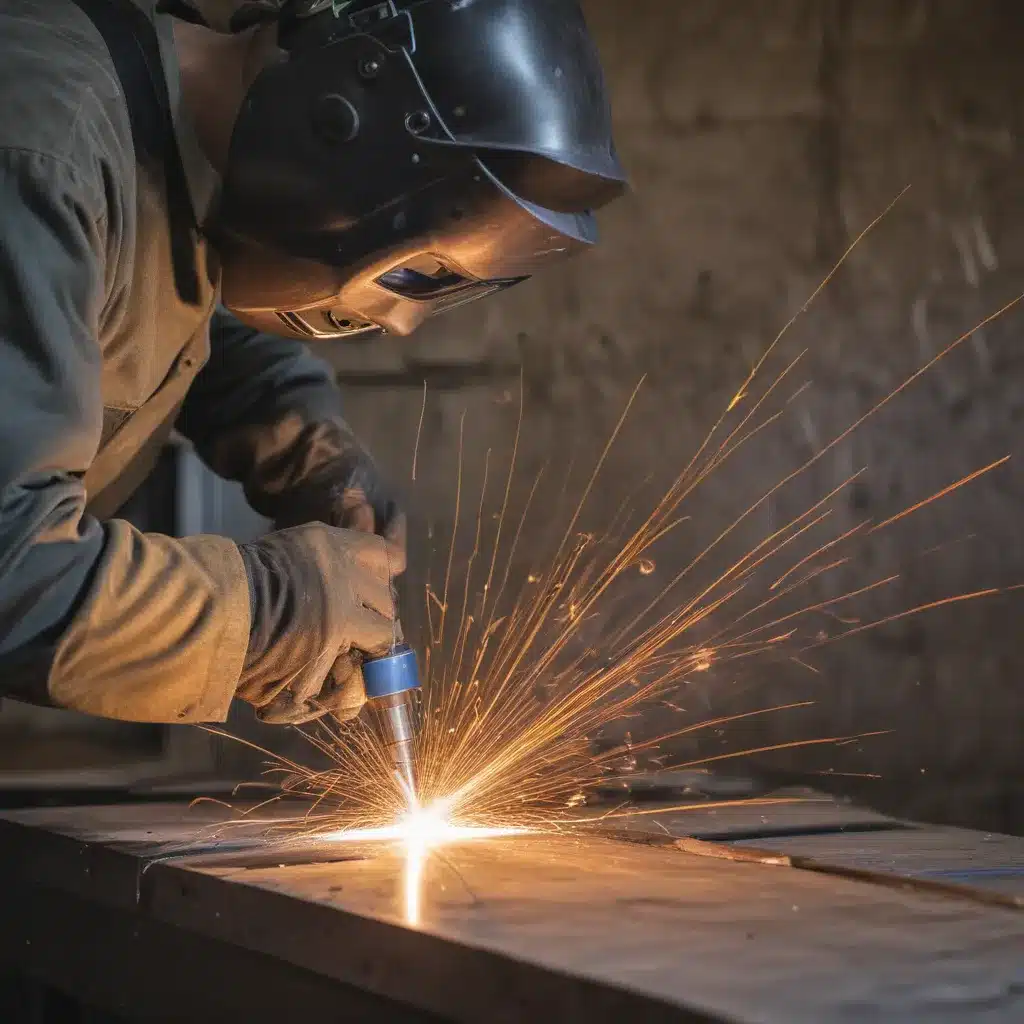
Ah, the world of welding – a realm where sparks fly, metals meld, and the very boundaries of what’s possible are constantly being pushed. As the owner of a welding services company, I’ve had the privilege of witnessing some of the most captivating and cutting-edge welding techniques firsthand. And let me tell you, the future of this industry is nothing short of mind-blowing.
Mastering the Art of Friction Stir Welding
Let’s start with the fascinating technique of friction stir welding. This process, which was initially developed by the Welding Institute in the UK, is a solid-state joining method that doesn’t rely on the melting of the materials being joined. Instead, it uses the heat generated by the friction between a rotating, non-consumable tool and the workpiece to plasticize the materials, allowing them to be joined without ever reaching their melting point.
The benefits of this approach are numerous. For one, it allows us to weld materials that are traditionally challenging to join using conventional arc welding methods, such as aluminum, magnesium, and even some steels. Plus, the lack of melting means that we can minimize the formation of brittle intermetallic compounds, which can compromise the structural integrity of the joint.
But the real magic happens when we start delving into the specific applications of friction stir welding. I’ve had the privilege of working on a project for a leading aerospace manufacturer, where we used this technique to seamlessly join the fuselage sections of their latest commercial aircraft. The resulting welds were not only incredibly strong but also perfectly smooth, with no visible distortion or warping. It was a true testament to the precision and control that friction stir welding can provide.
Harnessing the Power of Laser Beam Welding
Now, let’s talk about the dazzling world of laser beam welding. This technique, which utilizes the intense heat and focused energy of a laser beam, has revolutionized the way we approach welding in a wide range of industries.
One of the key advantages of laser beam welding is its ability to produce extremely narrow and deep welds, allowing us to precisely join even the most intricate components. This makes it an ideal choice for applications where access is limited or where weight and size constraints are critical, such as in the automotive and aerospace sectors.
But the real showstopper is the sheer speed at which laser beam welding can be performed. I recently had the opportunity to collaborate with a team of engineers on a project for a major automaker, where we used this technique to dramatically increase the production line’s throughput. The seamless integration of laser beam welding into their manufacturing process not only boosted efficiency but also enhanced the overall quality and consistency of the final product.
Exploring the Versatility of Plasma Arc Welding
While friction stir and laser beam welding may steal the spotlight, we can’t forget about the trusty and versatile plasma arc welding process. This technique, which uses a high-energy plasma arc to melt and join metals, has been a staple in the welding industry for decades.
One of the standout features of plasma arc welding is its ability to precisely control the heat input and penetration depth of the weld. This makes it an invaluable tool for applications where consistent and uniform welds are critical, such as in the manufacturing of high-pressure vessels and nuclear components.
But what really excites me about plasma arc welding is its versatility. I’ve used this technique to tackle everything from thin-gauge stainless steel fabrication to the heavy-duty joining of exotic alloys like titanium and inconel. And with the continuous advancements in plasma technology, I’m confident that we’ll continue to push the boundaries of what’s possible with this powerful welding method.
Embracing the Future with Hybrid Welding
As if the dazzling array of welding techniques we’ve already explored wasn’t enough, the industry is now abuzz with the revolutionary concept of hybrid welding. This innovative approach combines the strengths of two or more welding processes, creating a synergistic effect that transcends the capabilities of any individual technique.
One particularly intriguing example of hybrid welding is the fusion of laser and arc welding. By harnessing the precision and speed of laser beam welding alongside the flexibility and versatility of traditional arc welding, we can produce high-quality welds faster and more efficiently than ever before.
I’ve had the privilege of implementing this cutting-edge technology firsthand in a project for a leading automotive manufacturer. The results were truly astounding – we were able to achieve exceptionally deep and narrow welds while minimizing the heat-affected zone, ensuring the structural integrity of the final product.
Unlocking the Potential of Custom Fabrication
While exotic welding techniques may steal the spotlight, it’s important to remember that custom fabrication is the backbone of our industry. Whether it’s designing and building one-of-a-kind machinery, creating intricate metal structures, or tackling complex engineering challenges, the ability to provide custom fabrication services is crucial to the success of any welding company.
At our company, we take great pride in our custom fabrication capabilities. Our skilled team of engineers, designers, and fabricators work closely with our clients to understand their unique needs and translate them into tangible, high-quality solutions.
Whether it’s creating intricate metal sculptures for public art installations, designing and building custom industrial machinery for specialized applications, or tackling complex structural engineering projects, our team approaches each challenge with the same level of dedication, innovation, and attention to detail.
Elevating Precision Welding Services
Of course, no discussion of welding services would be complete without touching on the critical importance of precision welding.
Whether it’s producing intricate aerospace components, fabricating high-pressure vessels, or joining delicate electronic parts, the ability to deliver consistently flawless welds is essential to the success of any project.
At our company, we pride ourselves on our unwavering commitment to precision. Our team of highly skilled welders and technicians utilize the latest technologies and techniques to ensure that every weld we produce meets the most exacting standards.
From implementing advanced quality control measures to investing in state-of-the-art welding equipment, we leave nothing to chance when it comes to delivering precision welding services. Our clients can rest assured that their projects are in the hands of true experts.
Conclusion: Embracing the Future of Welding
As you can see, the world of welding is a constantly evolving and fascinating landscape. From the cutting-edge techniques of friction stir and laser beam welding to the versatility of plasma arc welding and the revolutionary potential of hybrid welding, the possibilities are truly endless.
And at the heart of it all is the unwavering commitment to custom fabrication and precision welding services that sets our company apart. We are constantly pushing the boundaries of what’s possible, driven by a passion for innovation and a deep respect for the art of welding.
So, if you’re looking to explore the cutting-edge of welding technology or in need of world-class custom fabrication and precision welding services, I invite you to visit us at https://www.corrconnect.org/. Let’s embark on an exciting journey together and push the limits of what’s possible in the world of welding.