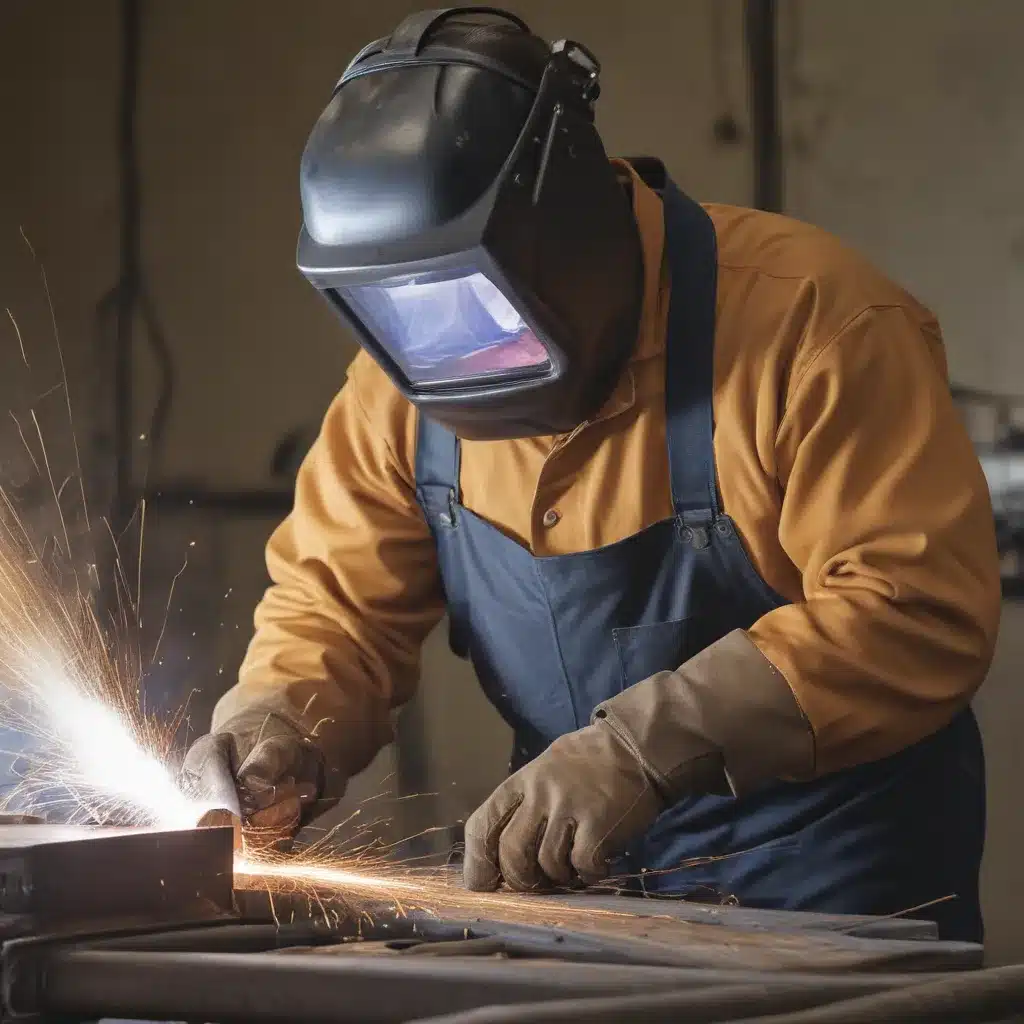
The Importance of Employee Engagement in Welding Safety
As the owner of a thriving welding services company, I can’t emphasize enough the crucial role that employee involvement plays in maintaining a safe work environment. Welding is an inherently hazardous profession, with a range of potential dangers lurking around every corner – from intense heat and blinding sparks to noxious fumes and the ever-present risk of electrocution. That’s why it’s so important for us, as business leaders, to foster a culture of safety awareness and empower our employees to take an active role in identifying and mitigating these risks.
You see, safety isn’t just the responsibility of management – it’s something that has to be embraced and prioritized by everyone on the shop floor. After all, who knows the intricacies of the welding process better than the skilled technicians performing the work day in and day out? They’re the ones who can spot potential hazards that might slip under the radar of an outside observer. And when they feel empowered to speak up, report unsafe conditions, and suggest improvements, that’s when the real magic happens.
I’ll never forget the time one of our welders, let’s call him Steve, approached me with a brilliant idea to redesign our ventilation system. He’d noticed that the fumes from a particular welding operation were building up in a corner of the workshop, putting the nearby workers at risk of respiratory issues. With his keen eye for detail and deep understanding of the workflow, Steve was able to devise a simple yet effective solution that significantly improved air quality and employee health.
Moments like that are the reason why I’m such a big proponent of employee involvement in safety. When you create an environment where people feel comfortable raising concerns and contributing their expertise, you unlock a wellspring of innovative thinking that can truly transform your operations. And the best part is, it doesn’t have to be complicated or resource-intensive – sometimes, the most impactful ideas come from the most unexpected places.
Strategies for Fostering a Culture of Safety Engagement
So, how exactly do you go about cultivating that kind of participatory safety culture? Well, in my experience, it all comes down to a few key strategies:
Open Communication and Feedback Loops
The foundation of any successful safety program is clear, two-way communication. You need to make sure your employees feel heard and valued, and that their feedback is being actively incorporated into your safety protocols.
One simple way to do this is by holding regular safety meetings, where you can discuss emerging risks, review incident reports, and solicit input from the team. These sessions should be collaborative and judgment-free, encouraging everyone to speak up without fear of repercussions. And don’t just limit it to formal meetings – make a habit of regularly checking in with your welders, asking them what’s working, what’s not, and what could be improved.
Another great tool is an anonymous suggestion box, where employees can submit ideas for enhancing safety without having to worry about potential backlash. I’ve found that this can be especially helpful for more introverted team members who might be hesitant to voice their concerns in a group setting. Just make sure you follow up on those suggestions and let your employees know that their input is being taken seriously.
Training and Empowerment
Of course, open communication is just the first step. To truly unlock the safety potential of your workforce, you need to invest in robust training programs that equip your welders with the knowledge and skills to identify and address hazards.
This goes beyond the basic safety certifications and onboarding sessions. Think about specialized courses on topics like welding fume control, personal protective equipment (PPE) selection, and ergonomic workstation design. The more informed and empowered your employees are, the more proactive they’ll be in spotting and mitigating risks.
But it’s not enough to just provide the training – you also need to create an environment where people feel empowered to put that knowledge into practice. Encourage your welders to conduct regular safety audits, to experiment with new tools and techniques, and to speak up whenever they notice something that could be improved. And be sure to celebrate their successes, whether it’s a clever solution to a persistent problem or a near-miss incident that was averted thanks to their vigilance.
Incentives and Recognition
Of course, sometimes a little carrot can go a long way, too. By implementing a robust system of incentives and recognition, you can further motivate your employees to stay engaged in safety efforts.
This could take the form of safety bonuses, awards for exemplary safety practices, or even just public acknowledgment and praise during team meetings. The key is to make it clear that safety isn’t just an abstract concept, but something that’s actively valued and rewarded within your organization.
You could also consider incorporating safety metrics into your overall performance evaluation process. That way, your welders know that their commitment to safety will be a key factor in their career advancement and compensation. Just be sure to strike the right balance – you don’t want safety to become solely about hitting numbers, at the expense of genuine engagement.
The Ripple Effects of Employee-Driven Safety
When you get all of these elements working in harmony – open communication, comprehensive training, and meaningful incentives – the results can be truly transformative. Not only will you see a marked improvement in your overall safety metrics, but you’ll also witness a shift in the culture and mindset of your organization.
Suddenly, your welders aren’t just passive participants in a safety program – they’re active stewards of their own well-being, and the well-being of their colleagues. They’re scanning the workshop with a critical eye, anticipating potential hazards and devising creative solutions. They’re not just following the rules, but truly internalizing the importance of safe practices and advocating for them at every turn.
And the best part? This mindset shift has a way of rippling out beyond the confines of the welding shop. I’ve seen our safety-conscious employees become ambassadors for safe practices in their personal lives, sharing their knowledge and best practices with friends and family. They’re more attuned to potential risks, more proactive about mitigating them, and more vocal about the importance of prioritizing safety.
It’s a virtuous cycle that just keeps building momentum. As our welders become more invested in safety, they inspire their peers to do the same. And as our overall safety culture grows stronger, it attracts new talent who are drawn to the idea of working in a truly safe and empowered environment.
In the end, it’s not just about compliance or accident prevention – it’s about cultivating a workforce that is engaged, empowered, and genuinely committed to their own well-being and the well-being of the entire team. And that, to me, is the true measure of a successful safety program.
Putting It All into Practice: Real-World Examples
Of course, all of this is well and good in theory, but the real test is in the execution. So let me share a few real-world examples of how we’ve put these employee involvement strategies into practice at our welding company, and the tangible results we’ve seen.
One of our most successful initiatives was the implementation of a comprehensive “safety champion” program. We identified a group of our most safety-conscious and influential welders, and empowered them to become safety advocates within their respective work teams. These champions received specialized training on hazard identification, incident investigation, and effective communication. They were then tasked with conducting regular safety audits, leading toolbox talks, and serving as the go-to resources for any safety-related questions or concerns.
The impact was immediate and substantial. Our safety champions became the eyes and ears of our safety program, spotting issues that our management team might have missed. They also played a crucial role in breaking down any lingering resistance to safety protocols, using their credibility and rapport with their colleagues to drive buy-in and participation.
Another initiative that’s been hugely successful is our ongoing “Idea of the Month” contest. Every month, we invite our welders to submit their ideas for improving safety, efficiency, or overall operations. The winning submission is then implemented, with the employee who suggested it receiving a cash bonus and public recognition at our monthly safety meeting.
The level of creativity and innovation that’s been unlocked through this program has been truly remarkable. We’ve seen everything from simple workflow tweaks that eliminate ergonomic strain, to complex equipment modifications that enhance collision avoidance. And the best part is, these ideas are coming straight from the people who know the job best – our welders on the front lines.
Perhaps one of the most powerful examples, though, is the story of our welder, Steve, that I mentioned earlier. You see, Steve had been with us for years, quietly going about his work and keeping his head down. But one day, he approached me with a detailed proposal to redesign our ventilation system, based on his observations of how the fumes were accumulating in certain areas of the shop.
I’ll admit, I was a bit skeptical at first. After all, I’m the owner – I should be the one coming up with these big, strategic ideas, right? But Steve was so passionate and convincing in his pitch that I couldn’t help but give it serious consideration. And when we implemented his plan, the results were nothing short of remarkable. Our workers’ respiratory health improved dramatically, and we even saw a noticeable uptick in productivity as people were no longer distracted by poor air quality.
Most importantly, though, Steve’s initiative sent a powerful message to the rest of the team: their voices and ideas truly matter. It showed them that they’re not just cogs in a machine, but valuable contributors who can shape the very fabric of our organization. And that, in turn, has cultivated an unprecedented level of engagement and ownership around safety throughout our company.
Conclusion: Embracing the Power of Employee Involvement
At the end of the day, I firmly believe that the key to sustained success in the welding industry is harnessing the collective wisdom and expertise of our employees. They’re the ones who live and breathe this work every single day, and they have an unparalleled understanding of the unique challenges and risks involved.
By creating a culture that empowers them to speak up, contribute ideas, and take an active role in shaping our safety protocols, we’re not only enhancing the wellbeing of our team, but also strengthening the long-term viability and competitiveness of our business. It’s a win-win scenario that I would encourage any welding services provider to embrace.
So, if you’re looking to take your safety performance to the next level, I urge you to start by engaging your employees. Listen to their concerns, implement their solutions, and celebrate their successes. Because when it comes to creating a truly safe and innovative welding operation, there’s no substitute for the invaluable insights and dedication of the people who make it all happen, day in and day out.
And if you’re ever in the market for top-notch welding services, be sure to check out Corr Connect – we pride ourselves on being a safety-first, employee-driven organization that delivers unparalleled quality and precision in everything we do. I’d be more than happy to chat with you about our approach and how we can help take your welding projects to new heights.