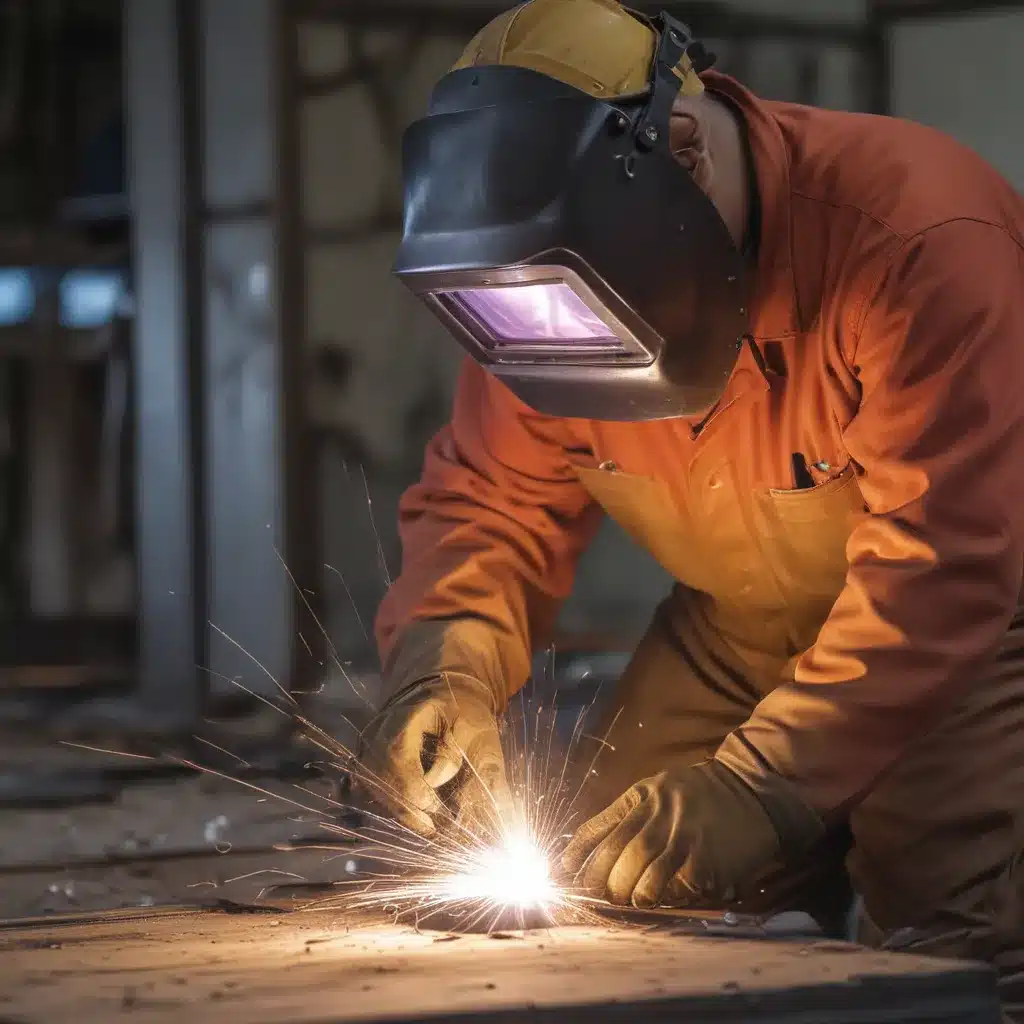
The Importance of Being Prepared
As a welder or fabricator, I know that our line of work can be unpredictable and downright chaotic at times. One minute, we’re meticulously crafting intricate metal components, and the next, we’re dealing with a power outage, a broken-down machine, or a natural disaster that throws a wrench in our plans. But you know what they say – the best defense is a good offense. That’s why emergency preparedness is so crucial for those of us in the welding and fabrication industries.
You see, when the unexpected happens, the difference between a minor inconvenience and a full-blown crisis often comes down to how well we’ve planned and prepared. It’s like that old saying, “Failing to prepare is preparing to fail.” And trust me, in our line of work, failure is simply not an option. Whether we’re talking about keeping our team safe, protecting our equipment and facilities, or ensuring the continuity of our operations, being proactive and having a solid emergency plan in place can make all the difference.
But where do we even start? Well, that’s what this article is all about. I’m going to dive deep into the ins and outs of emergency preparedness for welders and fabricators, covering everything from risk assessment and contingency planning to emergency response protocols and disaster recovery strategies. By the time we’re done, you’ll be equipped with the knowledge and tools you need to keep your business running smoothly, no matter what curveballs life throws your way.
Assessing Risks and Vulnerabilities
The first step in any effective emergency preparedness plan is to take a long, hard look at the risks and vulnerabilities that your welding or fabrication operation faces. This means carefully analyzing the potential threats, both natural and man-made, that could disrupt your business, and then developing strategies to mitigate those risks.
One of the key things I always recommend to my fellow welders and fabricators is to conduct a comprehensive risk assessment. This involves identifying all the potential hazards and threats that could impact your operations, such as:
- Natural disasters (e.g., hurricanes, earthquakes, floods, wildfires)
- Equipment failures or malfunctions
- Power outages or utility disruptions
- Cyber attacks or data breaches
- Supply chain disruptions
- Human-caused incidents (e.g., accidents, vandalism, terrorism)
Once you’ve identified these potential risks, the next step is to assess the likelihood and potential impact of each one. This will help you prioritize your preparedness efforts and focus on the areas that pose the greatest threats to your business.
For example, if you’re located in a region that’s prone to severe storms, you might want to prioritize emergency planning for power outages and flooding. On the other hand, if your facility is in a relatively stable area, you might need to devote more attention to cyber security or supply chain resilience.
The key here is to be as thorough and objective as possible in your risk assessment. Don’t just focus on the obvious threats – dig deep and consider all the potential points of failure in your operations. After all, the more prepared you are, the better equipped you’ll be to weather any storm that comes your way.
Developing a Comprehensive Emergency Plan
Now that you’ve identified the risks and vulnerabilities facing your welding or fabrication business, it’s time to start developing a comprehensive emergency plan. This plan should serve as a roadmap for how you and your team will respond to and recover from a crisis or disaster.
One of the most important elements of an effective emergency plan is clear and detailed contingency planning. This means identifying the specific actions you’ll take in the event of a particular emergency, and then outlining the roles and responsibilities of your team members.
For example, your contingency plan for a power outage might include:
- Procedures for safely shutting down and securing your welding equipment and other machinery
- Protocols for maintaining communication with your team and your customers
- A list of backup power sources (e.g., generators, battery backups) and their locations
- Instructions for safely evacuating your facility, if necessary
Similarly, your plan for a cyber attack might include:
- Steps for isolating your systems and preventing the spread of malware
- Procedures for backing up and restoring your critical data
- Contact information for your IT support team and any external cybersecurity experts
- A communication plan for informing your team and your customers about the incident
The key here is to be as comprehensive and detailed as possible in your planning. Don’t just create a generic “emergency plan” – instead, develop specific, actionable strategies for addressing the unique challenges and risks that your welding or fabrication operation faces.
And remember, your emergency plan shouldn’t just sit on a shelf gathering dust. It needs to be regularly reviewed, tested, and updated to ensure that it remains relevant and effective in the face of changing circumstances and evolving threats.
Equipping Your Team for Success
Of course, having a well-crafted emergency plan is only half the battle. The other crucial component of effective emergency preparedness is ensuring that your team is trained, equipped, and empowered to respond effectively when the proverbial hits the fan.
One of the key things I always stress to my fellow welders and fabricators is the importance of ongoing training and education. Your team needs to be intimately familiar with your emergency protocols and procedures, and they need to be regularly drilled and tested on their response capabilities.
This might involve things like:
- Hands-on training on the use of emergency equipment and supplies
- Tabletop exercises and simulations that walk your team through various crisis scenarios
- Regular safety and emergency response refresher courses
- Cross-training and skills development to ensure that your team has a diverse set of capabilities
But it’s not just about technical know-how – it’s also about fostering a culture of preparedness and resilience within your organization. Your team needs to feel empowered and confident in their ability to respond effectively to emergencies, and they need to know that they have the full support of their leadership.
This means clearly communicating your emergency protocols and procedures, and ensuring that everyone understands their roles and responsibilities. It also means providing the necessary resources, equipment, and supplies to keep your team safe and secure in the event of a crisis.
And let’s not forget about the psychological and emotional aspects of emergency preparedness. Dealing with a crisis can be incredibly stressful and overwhelming, so it’s important to have a plan in place for supporting your team’s mental and emotional well-being. This might include things like access to counseling services, employee assistance programs, and regular check-ins and debriefings.
Maintaining Business Continuity and Resilience
Okay, so you’ve conducted a thorough risk assessment, developed a comprehensive emergency plan, and equipped your team for success. But what happens after the immediate crisis has passed? How do you ensure that your welding or fabrication business can bounce back and continue operating in the aftermath of a disaster?
This is where the concept of business continuity and resilience comes into play. It’s all about putting the necessary systems and processes in place to ensure that your operations can continue, even in the face of disruption.
One of the key elements of business continuity planning is having a solid backup and recovery strategy for your critical data and systems. This might involve things like:
- Regularly backing up your data to offsite or cloud-based storage
- Maintaining redundant systems and infrastructure to ensure that your operations can continue even if one component fails
- Developing a clear plan for how you’ll restore your systems and data in the event of a disaster
But it’s not just about technology – it’s also about having a plan in place for maintaining your supply chain, managing your workforce, and communicating with your customers and stakeholders.
For example, your business continuity plan might include:
- Strategies for sourcing alternative suppliers or materials in the event of a supply chain disruption
- Protocols for quickly transitioning to remote or decentralized work arrangements, if necessary
- A communication plan for keeping your customers informed and reassured during a crisis
The key here is to think holistically about your business operations and to identify all the potential points of failure or disruption. By taking a proactive, systematic approach to business continuity planning, you’ll be better equipped to weather any storm and come out the other side stronger and more resilient.
Conclusion: Embracing a Culture of Preparedness
At the end of the day, emergency preparedness isn’t just about having a binder full of protocols and procedures – it’s about cultivating a culture of preparedness and resilience within your welding or fabrication organization.
It’s about instilling a sense of ownership and accountability in your team, and empowering them to be proactive in identifying and addressing potential risks. It’s about fostering open communication, collaboration, and a shared commitment to keeping your business and your people safe.
And it’s about continuously learning, adapting, and improving your emergency preparedness efforts, based on the lessons you learn and the evolving threats you face.
So, my fellow welders and fabricators, I encourage you to embrace this culture of preparedness with open arms. Because when the unexpected happens – and trust me, it will – you’ll be glad you took the time to get your ducks in a row.
Remember, the https://www.corrconnect.org/ team is always here to support you in your emergency preparedness efforts, whether it’s through our wide range of welding and fabrication services or our expert guidance and resources. Together, we can weather any storm and emerge even stronger than before.