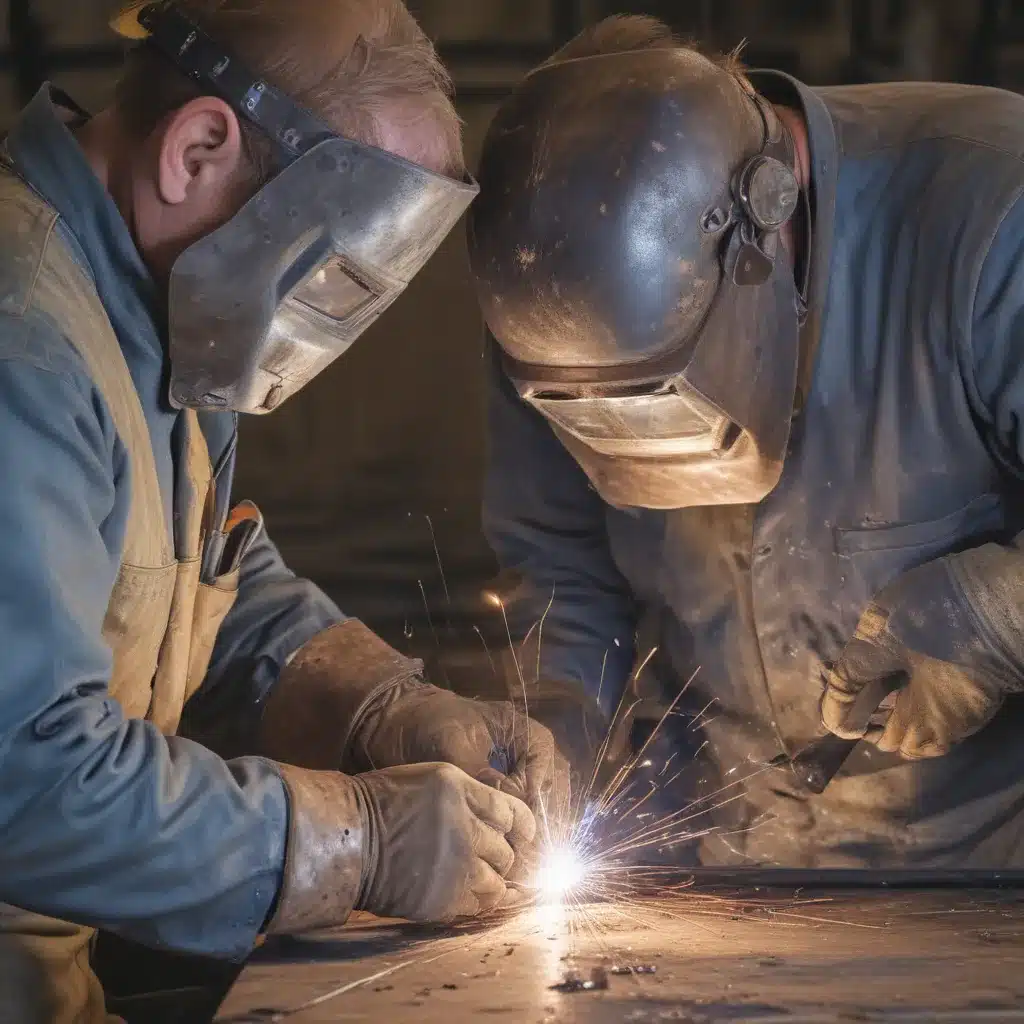
Uncovering the Hidden Challenges of Welding
As a seasoned welder with years of experience under my belt, I’ve seen my fair share of weld defects. These pesky imperfections can be a real thorn in the side, causing all sorts of headaches for both the welding professional and the end-user. But fret not, my fellow welding enthusiasts! In this comprehensive guide, I’ll take you on a journey of discovery, where we’ll delve into the world of weld defect identification and correction.
Let’s start by addressing the elephant in the room – why do weld defects even occur in the first place? Well, my friends, it’s a complex web of factors that can contribute to these unwelcome blemishes. From improper equipment setup and poor welding technique to inadequate material preparation and environmental conditions, the list goes on. But fear not, for I have the inside scoop on how to tackle these challenges head-on.
Mastering the Art of Weld Defect Identification
Ah, the art of weld defect identification – a skill that separates the welding pros from the amateurs. It’s like a high-stakes game of “Spot the Difference,” except the stakes are a bit higher than a cheap carnival prize. But fear not, my fellow welding enthusiasts, for I’m here to guide you through the process.
One of the key things to remember is that weld defects can manifest in a multitude of ways, from unsightly porosity to dreaded lack of fusion. And let me tell you, these little buggers can be as elusive as a chameleon in a kaleidoscope. But fear not, for with a keen eye and a thorough understanding of the various defect types, you’ll be able to sniff them out like a bloodhound on the trail of a juicy bone.
So, let’s dive in, shall we? Picture this: you’re carefully inspecting a freshly completed weld, and suddenly, you spot a peculiar-looking blemish. Is it a case of surface crack, or is it merely a harmless surface irregularity? Fear not, my friend, for I have the answers you seek. By carefully analyzing the size, shape, and location of the defect, you’ll be able to pinpoint the culprit and take the necessary steps to rectify the issue.
But wait, there’s more! Weld defects can also manifest in the internal structure of the joint, hidden from plain sight. This is where the power of non-destructive testing (NDT) comes into play. From penetrant testing to radiographic inspection, these cutting-edge techniques will allow you to peer beneath the surface and uncover any unseen imperfections. Trust me, it’s like having an X-ray vision for your welds!
Tackling Weld Defects: Strategies for Correction
Now that we’ve mastered the art of weld defect identification, it’s time to roll up our sleeves and tackle the task of correction. And let me tell you, it’s not always a straightforward process. In fact, it can be a bit like solving a Rubik’s Cube while blindfolded – a true test of your welding prowess.
But fear not, my fellow welding enthusiasts, for I have a few tricks up my sleeve. Whether it’s a case of porosity, lack of fusion, or an unsightly undercut, I’ll guide you through the necessary steps to get your welds back on track.
First and foremost, it’s crucial to address the root cause of the defect. Is it a problem with the equipment setup? An issue with the material prep? Or perhaps a flaw in your welding technique? By pinpointing the underlying cause, you’ll be able to implement targeted corrective measures and prevent the same problem from rearing its ugly head in the future.
But let’s not forget the importance of proper repair techniques. From grinding and chipping to rewelding and post-weld heat treatment, the options are vast and varied. And let me tell you, each approach has its own unique quirks and challenges. But fear not, for with a keen eye, a steady hand, and a deep understanding of the process, you’ll be able to turn those unsightly defects into a thing of the past.
Embracing Preventive Measures: The Key to Consistent Weld Quality
Now, as much as we love tackling those tricky weld defects, the true mark of a welding master is the ability to prevent them altogether. It’s like the old saying goes, “An ounce of prevention is worth a pound of cure.” And let me tell you, when it comes to welding, this couldn’t be more true.
So, what’s the secret to achieving consistently high-quality welds, you ask? Well, my friends, it all comes down to a comprehensive preventive maintenance program. From meticulous equipment inspections to rigorous operator training, the key is to stay one step ahead of those pesky defects.
But don’t just take my word for it. Let’s consider a real-life example: [Company Name] has been a trusted name in the welding industry for decades, and their success can be largely attributed to their commitment to preventive measures. By investing in state-of-the-art equipment, regularly calibrating their tools, and providing their team with top-notch training, they’ve been able to consistently deliver impeccable welding services to their clients.
And let me tell you, the results speak for themselves. Their customers rave about the exceptional quality of their work, and the [Company Name] team takes great pride in their ability to tackle even the most complex welding challenges with ease. It’s a testament to the power of preventive maintenance and the relentless pursuit of welding excellence.
So, my fellow welding enthusiasts, the next time you’re faced with a pesky weld defect, remember to take a step back and consider the bigger picture. By embracing a proactive approach to weld quality, you’ll not only save yourself countless headaches but also elevate your welding prowess to new heights. Trust me, it’s a game-changer that’s well worth the investment.
Unlocking the Secrets of Precision Welding
As a seasoned welding professional, I can tell you that the art of precision welding is a true testament to the skill and expertise of the welder. It’s not just about laying down a pretty bead – it’s about creating a flawless, structurally sound joint that can withstand the harshest of environments.
And let me tell you, achieving that level of precision is no easy feat. It requires a deep understanding of the welding process, a keen eye for detail, and a steady hand that can navigate the most intricate of workpieces. But fear not, my fellow welding enthusiasts, for I’m here to share the secrets of this elusive craft.
One of the key elements of precision welding is the careful selection and preparation of the materials. From the chemical composition of the base metal to the purity of the filler wire, every detail must be meticulously considered. And let’s not forget the importance of proper joint design – the shape and fit of the components can make all the difference in achieving a seamless, high-quality weld.
But the real magic happens when the welding torch meets the metal. It’s a delicate dance, where the welder must precisely control the heat input, the travel speed, and the arc length to ensure a consistent, uniform weld bead. And let me tell you, it’s not just about the technical aspects – it’s also about the welder’s intuition and experience, their ability to read the metal and respond accordingly.
And let’s not forget the importance of post-weld inspection and quality control. It’s not enough to just lay down a pretty bead – the weld must be rigorously tested to ensure it meets the strictest of standards. From non-destructive testing to destructive analysis, the [Company Name] team leaves no stone unturned in their pursuit of precision welding excellence.
But the real reward, my friends, is the satisfaction of seeing a flawless, structurally sound weld that stands the test of time. It’s a testament to the welder’s skill and dedication, a work of art that can withstand the harshest of conditions and deliver unparalleled performance.
Embracing the Cutting Edge: Advancements in Welding Technology
As a welding professional, I can tell you that the world of welding is constantly evolving, with new technologies and techniques emerging all the time. And let me tell you, it’s an exciting time to be in the industry!
From the advent of innovative welding processes like laser welding and friction stir welding to the integration of advanced computer-controlled systems, the welding landscape is undergoing a remarkable transformation. And the [Company Name] team is at the forefront of these advancements, embracing the latest and greatest in welding technology to deliver unparalleled results for our clients.
Take, for instance, the integration of robotic welding systems. These cutting-edge machines have the ability to perform complex welding tasks with unprecedented precision and consistency, significantly reducing the risk of weld defects and improving overall productivity. And the best part? The [Company Name] team has mastered the art of programming and operating these sophisticated systems, ensuring that our clients reap the full benefits of this transformative technology.
But the advancements don’t stop there, my friends. We’ve also seen a remarkable evolution in the field of non-destructive testing (NDT), with new techniques like ultrasonic testing and eddy current inspection allowing us to peer deep into the weld with unprecedented accuracy. And let me tell you, the [Company Name] team is well-versed in the latest NDT methodologies, ensuring that we can identify and address even the most elusive of weld defects.
And let’s not forget the role of digital technology in the welding industry. From cloud-based data management systems to augmented reality-powered training tools, the [Company Name] team is embracing the digital revolution to streamline our operations, improve our workflow, and deliver even greater value to our clients.
So, my fellow welding enthusiasts, the future of the industry is bright, and the [Company Name] team is leading the charge. By staying on the cutting edge of welding technology, we’re able to consistently deliver exceptional results, push the boundaries of what’s possible, and showcase the true power of this dynamic and ever-evolving craft.
The [Company Name] Difference: Unparalleled Welding Services
At [Company Name], we take great pride in our unwavering commitment to excellence in the world of welding. As a team of seasoned professionals with decades of collective experience, we’ve honed our skills to a razor’s edge, tackling even the most complex welding challenges with unparalleled precision and expertise.
But what sets us apart, you ask? Well, my friends, it’s a combination of factors that make the [Company Name] difference truly stand out. First and foremost, we’re driven by a relentless pursuit of perfection – a never-ending quest to push the boundaries of what’s possible in the world of welding.
Whether it’s a delicate precision welding project or a large-scale custom fabrication job, we approach every task with the same level of dedication and attention to detail. From meticulous material selection and preparation to the flawless execution of the welding process, we leave no stone unturned in our pursuit of weld quality excellence.
And let’s not forget the importance of our preventive maintenance program. By regularly inspecting and calibrating our state-of-the-art welding equipment, we’re able to ensure that our tools are always in tip-top shape, ready to deliver consistent, high-quality results time and time again.
But the real secret to our success, my friends, lies in the incredible talent and expertise of our team. We’ve handpicked the finest welding professionals in the industry, each with their own unique set of skills and specialties. From our seasoned welding technicians to our cutting-edge NDT experts, every member of the [Company Name] family is dedicated to providing our clients with the very best in welding services.
And let’s not forget the importance of our commitment to safety. After all, welding can be a hazardous profession, and we take the well-being of our team and our clients incredibly seriously. That’s why we’ve implemented the strictest safety protocols, ensuring that every project is completed with the utmost care and attention to detail.
So, if you’re in the market for unparalleled welding services, look no further than [Company Name]. With our unwavering dedication to quality, our cutting-edge technology, and our world-class team of welding experts, we’re poised to deliver the kind of results that will leave you in awe. So, what are you waiting for? [Hyperlink to https://www.corrconnect.org/] and let’s get started on your next welding project!