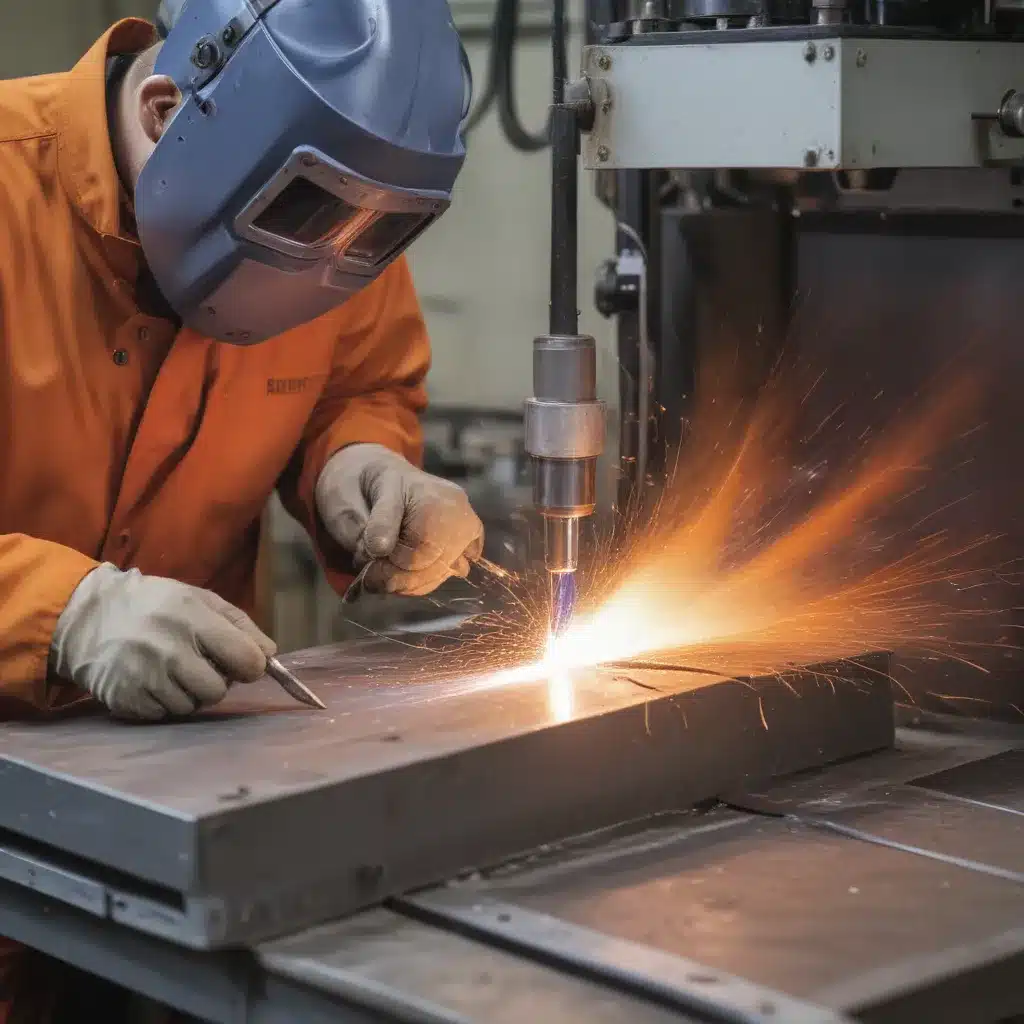
The Balancing Act: Heat Input, Microstructure, and Weld Strength
As a seasoned welder, I’ve learned that the secret to achieving the perfect weld lies not just in the technical know-how, but in the delicate dance between heat input and the underlying chemistry of the metals. It’s a balance akin to a finely tuned symphony, where each element must be carefully orchestrated to produce a harmonious result.
You see, when it comes to welding, the amount of heat input and the chemical composition of the weld metal are the two primary factors that dictate the hardness and strength of the final weld. Get this equation wrong, and you could end up with a joint that’s either too brittle or too soft – a recipe for disaster in the world of precision fabrication.
Let me paint you a picture. Imagine you’re tasked with welding a critical component for a high-performance racing engine. The tolerances are tight, and the weld needs to be strong enough to withstand the immense stresses of a turbocharged motor. But if you crank up the heat too much, the weld metal could become too hard and brittle, making it susceptible to cracking under pressure. On the other hand, if you don’t apply enough heat, the weld might not penetrate deep enough, compromising the overall strength.
It’s a delicate balancing act, my friends, and one that requires a keen understanding of the underlying science. That’s why I’m here to share my insights and guide you through the intricacies of controlling weld metal hardness through heat input and chemistry. By the end of this article, you’ll be armed with the knowledge to tackle even the most demanding welding projects with confidence.
The Science Behind Weld Metal Hardness
So, let’s dive in and explore the science behind weld metal hardness. At its core, the hardness of a weld is determined by the microstructure of the weld metal – the arrangement and composition of the individual grains and phases within the material.
Now, you might be wondering, “What does this have to do with heat input and chemistry?” Well, my friend, it’s all interconnected. You see, the amount of heat input during the welding process directly influences the cooling rate of the weld metal, which in turn affects the microstructure that ultimately forms.
Faster cooling rates, typically achieved with lower heat inputs, tend to produce a finer, more uniform microstructure. This can result in a harder, stronger weld that is less prone to cracking. Conversely, slower cooling rates, often associated with higher heat inputs, can lead to a coarser microstructure with larger grains, resulting in a softer, more ductile weld.
But wait, there’s more! The chemical composition of the weld metal also plays a crucial role in determining its hardness. Certain alloying elements, such as carbon, chromium, and molybdenum, can significantly enhance the hardness of the weld by promoting the formation of hard, complex microstructures like martensite and bainite.
Imagine you’re working with a high-strength steel alloy. The addition of just a small amount of carbon can transform the weld metal from a relatively soft, ductile state to a much harder, more brittle one. This is where the delicate balance comes into play – you need to carefully control both the heat input and the chemical composition to achieve the perfect blend of hardness and ductility.
Optimizing Heat Input for Desired Weld Metal Hardness
Now that we’ve explored the underlying science, let’s dive into the practical aspects of optimizing heat input for the desired weld metal hardness.
One of the key factors to consider is the welding process itself. Different welding techniques, such as shielded metal arc welding (SMAW), gas metal arc welding (GMAW), and flux-cored arc welding (FCAW), can deliver varying levels of heat input, which can ultimately impact the weld metal hardness.
For example, SMAW, also known as stick welding, typically has a lower heat input compared to GMAW or FCAW. This lower heat input can produce a finer, harder weld microstructure, making it a suitable choice for applications that require high strength and wear resistance.
On the other hand, GMAW, or MIG welding, often has a higher heat input, which can result in a more ductile weld with a coarser microstructure. This might be the preferred choice for applications where some flexibility and deformability are desired, such as in the fabrication of structural steel frames.
But it’s not just the welding process that matters – the welding parameters also play a crucial role. Things like amperage, voltage, travel speed, and electrode size can all be fine-tuned to adjust the heat input and achieve the desired weld metal hardness.
Imagine you’re working on a project that requires a weld with exceptional hardness to withstand heavy impact loads. By increasing the amperage and reducing the travel speed, you can boost the heat input, which in turn can promote the formation of a harder, more martensitic microstructure in the weld metal.
On the flip side, if you’re dealing with a project that calls for a more ductile weld, you might want to reduce the heat input by lowering the amperage and increasing the travel speed. This can result in a softer, more forgiving weld microstructure that’s less prone to cracking or brittle failure.
The Chemistry Factor: Alloying Elements and Weld Metal Hardness
As we’ve discussed, the chemical composition of the weld metal is another crucial factor in determining its hardness. And let me tell you, the world of weld metal chemistry is a fascinating one, filled with all sorts of alloying elements that can be leveraged to fine-tune the properties of the final weld.
Take carbon, for example. This humble element is a true workhorse when it comes to enhancing weld metal hardness. By carefully controlling the carbon content, you can tailor the microstructure of the weld to achieve the perfect balance of strength and ductility.
Imagine you’re working on a project that requires a weld with exceptional hardness to withstand heavy impact loads. By increasing the carbon content of the weld metal, you can promote the formation of a hard, martensitic microstructure, which can provide the necessary strength and wear resistance.
But it’s not just carbon that holds the key to weld metal hardness. Other alloying elements, such as chromium, molybdenum, and vanadium, can also play a significant role in enhancing the hardness and strength of the weld.
Chromium, for instance, is a versatile alloying element that can increase the hardenability of the weld metal, making it more resistant to wear and corrosion. Molybdenum, on the other hand, can help stabilize the hard, martensitic microstructure, improving the overall toughness of the weld.
And let’s not forget about vanadium, which can refine the weld metal microstructure, leading to a finer grain size and increased strength. It’s like having a whole toolbox of alloying elements at your disposal, each with its own unique capabilities to help you craft the perfect weld.
But here’s the catch – the interplay between these alloying elements and their effects on weld metal hardness can be quite complex. It’s not as simple as just adding more of one element and expecting a linear increase in hardness. You have to carefully balance the chemistry, taking into account the synergistic and sometimes antagonistic effects of these alloying elements.
Imagine you’re working on a high-stakes project that requires a weld with exceptional strength and toughness. You might decide to incorporate a blend of alloying elements, such as carbon, chromium, and vanadium, to create a weld metal that’s hard enough to withstand the demands of the application, yet ductile enough to prevent catastrophic failure.
Real-World Examples: Controlling Weld Metal Hardness in Action
Now that we’ve delved into the science and theory behind controlling weld metal hardness, let’s take a look at some real-world examples to see how it all comes together.
One of the projects I’m particularly proud of was a custom fabrication job for a high-performance motorcycle manufacturer. They needed a set of specialized engine mounts that could withstand the extreme vibrations and stresses of a turbocharged V-twin engine. The challenge was to create a weld that was both incredibly strong and ductile, to prevent cracking or fatigue failure.
To achieve this, we carefully selected a high-strength steel alloy with a moderate carbon content, and then fine-tuned the welding parameters to deliver the optimal heat input. By combining a lower amperage with a higher travel speed, we were able to achieve a weld microstructure that was just the right balance of hardness and ductility.
The result? A set of engine mounts that not only passed the rigorous stress testing, but also managed to shave a few precious pounds off the overall weight of the motorcycle, thanks to the high strength-to-weight ratio of the weld.
But it’s not just high-performance applications where controlling weld metal hardness is crucial. I once worked on a project for a large-scale construction company that was building a new state-of-the-art office complex. The structural steel frames required welds that were strong enough to support the immense loads, yet flexible enough to withstand the dynamic forces of wind and seismic activity.
In this case, we opted for a higher heat input welding process, such as GMAW, to achieve a more ductile weld microstructure. By carefully managing the amperage, voltage, and travel speed, we were able to create welds that were strong enough to support the structure, yet flexible enough to absorb the dynamic stresses without cracking or failing.
And let’s not forget about the precision welding services we offer here at [Company Name]. Recently, we had a client come to us with a unique challenge – they needed a series of custom-fabricated components for a cutting-edge medical device, and the welds had to be absolutely perfect, both in terms of strength and appearance.
In this case, we leveraged our expertise in controlling weld metal hardness to deliver a solution that exceeded our client’s expectations. By using a lower heat input SMAW process and carefully selecting the right combination of alloying elements, we were able to create welds that were incredibly strong, yet maintained a clean, uniform appearance that met the stringent aesthetic requirements of the medical device industry.
These are just a few examples of how we’ve been able to harness the power of heat input and weld metal chemistry to deliver exceptional results for our clients. And let me tell you, it’s not just about the technical know-how – it’s about having a deep, intuitive understanding of the science behind it all, and the creativity to apply it in innovative ways.
Unlocking the Full Potential of Your Welding Projects
As you can see, controlling weld metal hardness through heat input and chemistry is a complex, yet fascinating topic. But with the right knowledge and expertise, it’s a powerful tool that can unlock the full potential of your welding projects, whether you’re working on high-performance engines, heavy-duty construction, or precision medical devices.
At [Company Name], we pride ourselves on our ability to navigate this delicate balance, leveraging our deep understanding of the underlying science to deliver exceptional results time and time again. So, if you’re looking to take your welding game to the next level, I encourage you to [check out our services] (https://www.corrconnect.org/) and let us show you what we can do.
Who knows, maybe your next project will be the one that really pushes the boundaries of what’s possible in the world of welding. And with our help, you just might be able to create something truly extraordinary.