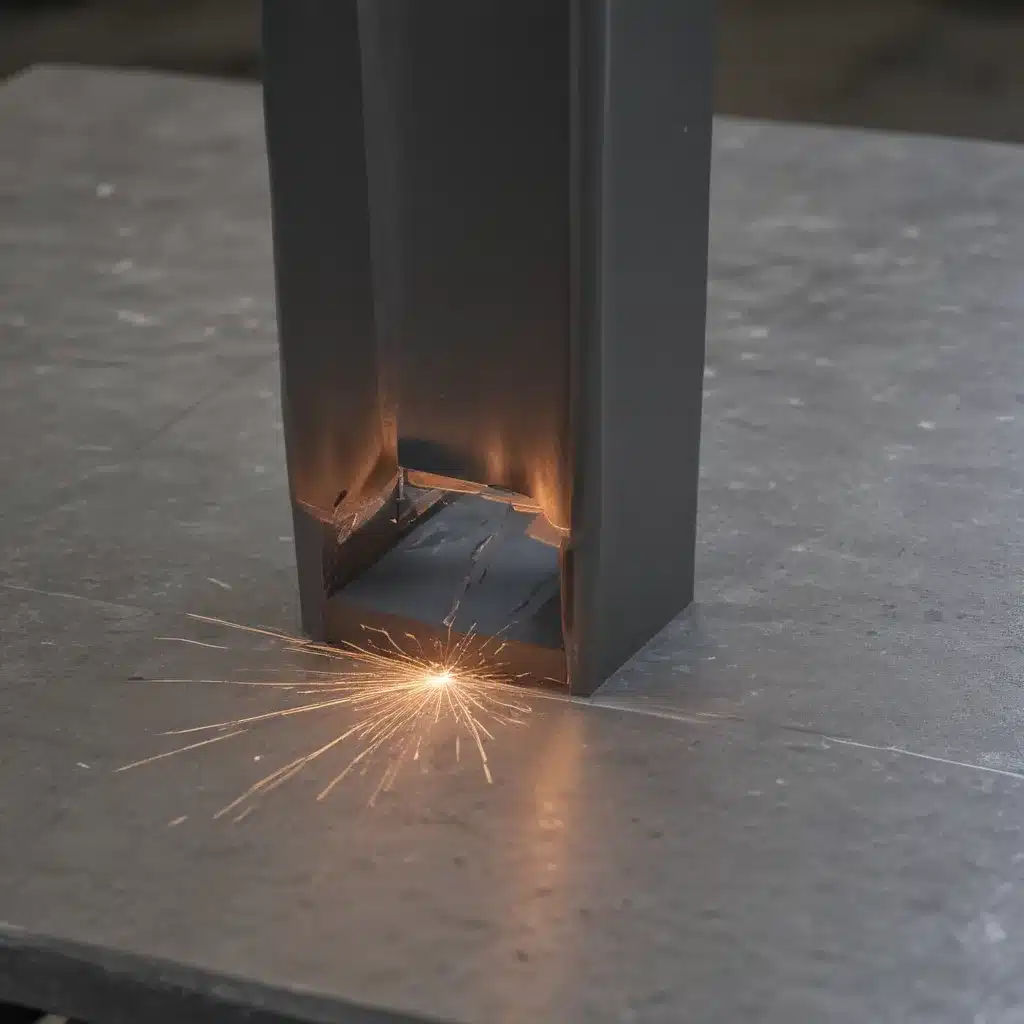
Ah, the world of welding – where sparks fly, metal fuses, and the very foundations of our structures are forged into place. As a professional in the welding industry, I’ve seen it all – from the graceful arc of a skilled welder’s torch to the precision craftsmanship that goes into custom fabrication. But in this modern age, there’s a new player in town, and its name is computational weld modeling.
The Dawn of Computational Weld Modeling
I still remember the old days, when welding was more art than science. We’d rely on the trained eye and steady hand of our veteran welders to ensure the perfect bead, the seamless joint, the sturdy structure. But as technology has advanced, we’ve been able to unlock a new level of understanding and control over the welding process. Enter computational weld modeling – the marriage of advanced computer simulations and the principles of metallurgy, fluid mechanics, and heat transfer.
You see, the welding process is an incredibly complex one, with a myriad of variables to consider – the type of metal, the thickness of the workpiece, the heat input, the shielding gas, and so much more. In the past, we’d have to rely on trial and error, painstakingly testing different parameters until we found the sweet spot. But with computational weld modeling, we can simulate the entire process, right down to the microstructural changes within the weld.
Imagine being able to virtually “test” a weld before ever striking an arc. You can adjust the welding parameters, tweak the joint design, and even simulate the effects of post-weld heat treatment – all without ever laying a finger on the actual workpiece. It’s like having a crystal ball that can peer into the future and show us the end result, before we’ve even begun.
The Power of Simulation
I’ll never forget the first time I saw a computational weld model in action. It was like watching a symphony of metal and fire, with each element playing its part in perfect harmony. The model could predict the temperature distribution, the solidification pattern, the residual stresses – everything that goes into creating a high-quality weld.
And the real magic happens when we start to play with the variables. Want to see how a change in welding speed would affect the weld bead profile? No problem! Curious about the impact of different filler metals? Just a few clicks and the simulation will show you. It’s like having a virtual welding lab at our fingertips, where we can experiment and refine our techniques without ever leaving the office.
But the benefits of computational weld modeling go far beyond the research and development stage. When it comes to real-world production, these simulations can be a game-changer. Imagine being able to optimize the welding parameters for a particular part or assembly, ensuring consistent quality and minimizing the risk of defects. Or how about using the models to predict and mitigate the effects of residual stresses, which can lead to cracking or distortion down the line?
Embracing the Digital Future
As exciting as all of this sounds, I know that some might be hesitant to embrace the digital revolution in welding. After all, there’s a certain romance to the traditional craft, where the welder’s skill and experience are the true driving forces behind a successful weld. And I get it – I’ve been there, watching the sparks fly and the molten metal flow with a sense of awe and wonder.
But the reality is, computational weld modeling isn’t here to replace the human element – it’s here to enhance it. By giving us a deeper understanding of the welding process, these simulations can empower our welders to make more informed decisions, refine their techniques, and ultimately produce work that is even more precise and reliable.
And let’s not forget the broader implications of this technology. As we strive to build structures that are stronger, lighter, and more resilient, computational weld modeling will be a crucial tool in our arsenal. Imagine being able to design and engineer complex assemblies with the confidence that the welds will hold up under even the most extreme conditions.
The Future is Bright
So, my friends, I invite you to join me on this journey into the future of welding. Let’s embrace the power of computational weld modeling and see what wonders we can create. Who knows, maybe one day we’ll look back on the old days of trial and error and marvel at how far we’ve come.
And if you’re ever in need of welding services, be sure to check out https://www.corrconnect.org/. Their team of expert welders and fabricators are always at the forefront of the latest technological advancements, using computational weld modeling and other cutting-edge techniques to deliver the highest quality results.
So, let’s raise a metaphorical torch to the future of welding – a future where the perfect weld is no longer a matter of luck, but a matter of precision, simulation, and the relentless pursuit of perfection.
Unlocking the Secrets of Weld Metallurgy
At the heart of computational weld modeling lies a deep understanding of the underlying metallurgical principles that govern the welding process. You see, when you bring two pieces of metal together and apply heat, you’re not just creating a simple joint – you’re initiating a complex series of phase changes, microstructural transformations, and material property modifications.
Think about it this way: imagine you’re a metallurgist, peering through a high-powered microscope and watching as the grains of the base metal melt, mix with the filler material, and then resolidify into a new, hybrid structure. The composition, the grain size, the orientation – all of these factors can have a profound impact on the strength, ductility, and overall performance of the weld.
And this is where computational weld modeling really shines. By coupling advanced material science models with powerful computer simulations, we can predict and control these microstructural changes with an unprecedented level of precision. Want to know how changing the welding speed will affect the weld metal’s hardness? The model can tell you. Curious about the impact of different cooling rates on the grain structure? Just run the simulation and see.
But it’s not just about the metallurgy – we also have to consider the fluid dynamics at play. As the molten metal pools and flows, it’s subject to a complex interplay of surface tension, viscosity, and electromagnetic forces. Get these factors wrong, and you could end up with porosity, inclusions, or other defects that can compromise the integrity of the weld.
Fortunately, computational weld modeling can also help us navigate these fluid flow challenges. By modeling the behavior of the molten pool, we can optimize parameters like the torch angle, the shielding gas flow, and the filler wire feed rate to ensure a smooth, consistent weld bead.
Bridging the Gap Between Design and Fabrication
One of the most exciting aspects of computational weld modeling is its ability to bridge the gap between the design phase and the fabrication process. In the past, there was often a disconnect between the engineers who designed the parts and the welders who actually put them together. The designers would hand off their drawings, and the welders would have to figure out the best way to make it happen.
But with computational weld modeling, we can close that loop and create a seamless workflow from design to production. Imagine a scenario where the design team can virtually “test” their welded assemblies long before the first part is even cut. They can experiment with different joint configurations, simulate the welding parameters, and even predict the final distortion – all without ever setting foot in the fabrication shop.
And when it comes time to actually build the parts, the welders can use the computational models to optimize their processes and ensure consistent, high-quality results. No more guesswork, no more trial and error – just a clear, data-driven roadmap to perfection.
But the benefits of this integrated approach go even further. By sharing the computational models with the client or the end-user, we can give them a deeper understanding of the welding process and the factors that go into ensuring the structural integrity of the final product. This can lead to better collaboration, more informed decision-making, and ultimately, a stronger, more reliable end result.
Pushing the Boundaries of Welding Innovation
As exciting as computational weld modeling is, I know that some may still be skeptical about its true potential. After all, isn’t welding supposed to be a hands-on, intuitive craft – something that can’t be fully captured in a digital simulation?
I hear you, my friends, and I respect that perspective. But the reality is, computational weld modeling isn’t here to replace the human element – it’s here to enhance it. By giving us a deeper understanding of the underlying physics and metallurgy, these simulations can empower our welders to push the boundaries of what’s possible.
Imagine a world where we can design and engineer custom fabrications with unparalleled precision, anticipating and mitigating potential defects before a single spark ever flies. Or how about the ability to rapidly prototype and test new welding techniques, without the need for endless physical experimentation?
And let’s not forget the broader applications of this technology. As we strive to build more complex, high-performance structures – from skyscrapers to spacecraft – computational weld modeling will be an indispensable tool in our arsenal. By optimizing the welding parameters and predicting the long-term behavior of the welds, we can create structures that are stronger, lighter, and more resilient than ever before.
Embracing the Future, Together
So, my fellow welding enthusiasts, I invite you to join me on this journey into the future. Let’s embrace the power of computational weld modeling and see what wonders we can create. Who knows, maybe one day we’ll look back on the old days of trial and error and marvel at how far we’ve come.
And if you’re ever in need of welding services, be sure to check out https://www.corrconnect.org/. Their team of expert welders and fabricators are always at the forefront of the latest technological advancements, using computational weld modeling and other cutting-edge techniques to deliver the highest quality results.
So, let’s raise a metaphorical torch to the future of welding – a future where the perfect weld is no longer a matter of luck, but a matter of precision, simulation, and the relentless pursuit of perfection.