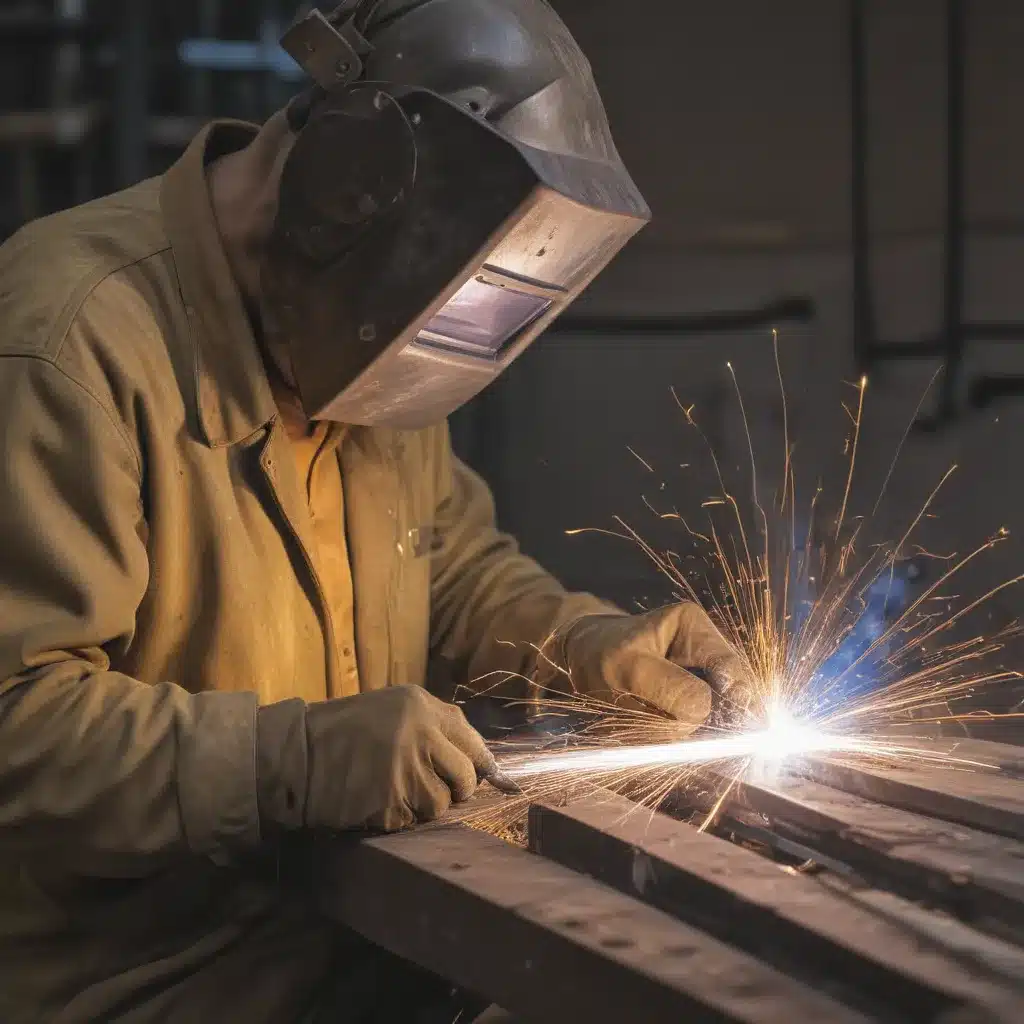
Introduction: Unraveling the Mysteries of Welding Flaws
As a seasoned welder, I’ve seen my fair share of challenges on the job. One of the most vexing issues we often face is the pesky presence of welding defects. These annoying little buggers can really put a damper on even the most carefully executed welding project. But fear not, my friends! In this comprehensive guide, I’ll take you on a deep dive into the world of welding defects – how to identify them, understand their root causes, and most importantly, prevent them from occurring in the first place.
So, buckle up and get ready to don your safety goggles, because we’re about to embark on a welding odyssey that will leave you feeling like a pro…or at least a little less like a hapless amateur. Let’s do this!
Defining Welding Defects: The Unruly Villains of the Workshop
First things first, let’s get a firm grasp on what exactly we’re dealing with here. Welding defects are imperfections or discontinuities that arise during the welding process, disrupting the intended structural integrity and appearance of the final product. These pesky little buggers can take on all sorts of shapes and sizes, from porosity and cracks to undercut and incomplete fusion.
And let me tell you, these welding villains can really wreak havoc if left unchecked. They can compromise the strength and durability of the weld, leading to potential catastrophic failures down the line. Imagine your carefully crafted metal masterpiece collapsing under the weight of its own flaws – yikes!
But fear not, my fellow welding warriors, for with a keen eye and a methodical approach, we can identify and address these troublemakers before they can do any real damage. It’s all about understanding the underlying causes and implementing the right preventive measures. Trust me, once you get the hang of it, you’ll be welding like a pro in no time!
Identifying Welding Defects: Separating the Wheat from the Chaff
Alright, now that we’ve got the basics down, let’s dive a little deeper into the world of welding defects. The first step in tackling these pesky problems is being able to spot them in the first place. And let me tell you, these little guys can be sneaky – they’ve got all sorts of tricks up their sleeves.
Take porosity, for example. This one’s a real doozy, with those pesky little gas bubbles hiding out in the weld like tiny little welding gremlins. And then there’s undercut, where the weld bead dips below the surface of the base metal, creating a nasty little groove that can really weaken the joint.
But don’t worry, with a keen eye and a little practice, you’ll be able to spot these defects from a mile away. It’s all about paying close attention to the welding process, inspecting the weld thoroughly, and knowing what to look for. And trust me, once you start getting the hang of it, it’ll be like a fun little game of “Where’s Waldo?” – except the stakes are a little higher than finding a goofy-looking guy in a striped shirt.
So, let’s take a closer look at some of the most common welding defects, shall we? From porosity and cracks to undercut and lack of fusion, we’ll dive deep into the telltale signs and symptoms of these pesky problems. By the time we’re done, you’ll be a regular Sherlock Holmes of the welding world!
Porosity: When Bubbles Ruin the Party
Ah, porosity – the bane of every welder’s existence. This one’s a real doozy, with those pesky little gas bubbles hiding out in the weld like tiny little welding gremlins. And let me tell you, these little buggers can really put a damper on your welding party.
You see, porosity occurs when gas becomes trapped in the weld pool, creating those unsightly little bubbles that can seriously compromise the structural integrity of your weld. And the worst part? They can be a real pain to spot, hiding away in the depths of the weld like little welding ninjas.
But fear not, my friends! With a keen eye and a few handy tools, you can ferret out these pesky problems in no time. First and foremost, it’s all about paying close attention to the welding process itself. Keep an eye out for any irregularities in the weld pool, like sudden changes in size or shape, or the appearance of tiny little bubbles breaking the surface.
And let’s not forget the trusty old visual inspection. Carefully examine the weld bead once it’s cooled, looking for any signs of porosity, like tiny little pits or pinholes dotting the surface. It’s like a game of “Where’s Waldo?” but with higher stakes and way more welding know-how.
But wait, there’s more! You can also use some nifty non-destructive testing techniques to really get to the bottom of this porosity problem. Radiographic testing, for instance, can give you a peek inside the weld, revealing any hidden gas pockets or other defects. And ultrasonic testing? That’s like having a little welding X-ray vision, allowing you to identify and locate those pesky little bubbles with pinpoint accuracy.
So, the next time you’re faced with a weld full of porosity, don’t panic! With a little know-how and the right tools, you can track down those troublemakers and send them packing. After all, a good welder is always ready to face down the toughest welding challenges, porosity included!
Cracks: The Fracture Frontier
Ah, cracks – the bane of every welder’s existence. These little fissures can really put a damper on even the most carefully executed welding project, compromising the structural integrity of the final product and leaving you scratching your head in frustration.
But fear not, my friends! With a keen eye and a deep understanding of the underlying causes, we can tackle these pesky problems head-on. You see, cracks can arise from all sorts of culprits, from residual stresses in the base metal to poor weld bead profile and everything in between.
Let’s start with the classic hot crack, shall we? These little buggers form right in the weld pool as the metal solidifies, often the result of high-sulfur content in the base material or an improper welding technique. It’s like a tug-of-war between the solidifying metal and the surrounding molten pool, and sometimes, the metal just can’t take the strain and splits right down the middle.
And then there’s the cold crack, which rears its ugly head after the weld has cooled. These can be even trickier to spot, as they can lurk beneath the surface, slowly weakening the joint over time. Often, they’re the result of hydrogen embrittlement or residual stresses in the base metal, just waiting to pounce.
But don’t worry, my fellow welding warriors, we’ve got a few tricks up our sleeves to keep these cracks at bay. It’s all about paying close attention to the welding parameters, using the right filler materials, and carefully controlling the cooling process. And when it comes to inspection, don’t be afraid to break out the big guns – ultrasonic testing, dye penetrant, and even good old-fashioned visual inspection can all help you sniff out those pesky cracks before they cause any real damage.
So, the next time you’re faced with a weld that’s looking more like a spiderweb than a sturdy joint, don’t panic! With a little know-how and the right tools, you can tackle those cracks head-on and come out on top. After all, a good welder is always ready to face down the toughest welding challenges, cracks and all!
Undercut: When the Weld Bead Falls Short
Ah, undercut – the bane of every welder’s existence. This one’s a real doozy, where the weld bead dips below the surface of the base metal, creating a nasty little groove that can really weaken the joint. It’s like a welding version of a pothole, just waiting to trip up your carefully crafted metal masterpiece.
But fear not, my friends! With a little bit of know-how and some diligent attention to detail, we can put a stop to these pesky undercut problems once and for all. You see, undercut can be caused by all sorts of factors, from improper welding technique to the wrong choice of filler material.
Let’s start with the welding technique, shall we? If you’re not keeping that arc nice and tight, or if you’re moving the torch too quickly, you can end up with a weld bead that just can’t seem to keep up with the base metal. It’s like trying to run a marathon in high heels – not gonna end well.
And then there’s the filler material. If you’re not using the right stuff for the job, you can end up with a weld that just can’t quite fill in those gaps and depressions. It’s like trying to plaster a wall with toothpaste – sure, it might work in a pinch, but it’s not gonna hold up in the long run.
But fear not, my fellow welding warriors! With a few simple tweaks, you can banish undercut for good. It’s all about finding the right balance of welding parameters, using the appropriate filler material, and keeping a close eye on that weld pool. And when it comes to inspection, don’t be afraid to break out the good old-fashioned straight edge – it’s like a welding version of a carpenter’s level, helping you spot those pesky undercutting issues from a mile away.
So, the next time you’re faced with a weld that’s looking more like a canyon than a sturdy joint, don’t panic! With a little bit of welding know-how and a keen eye for detail, you can nip those undercut problems in the bud and come out on top. After all, a good welder is always ready to face down the toughest welding challenges, undercut and all!
Lack of Fusion: When the Weld Just Doesn’t Stick
Ah, lack of fusion – the ultimate welding frustration. It’s like the weld just can’t seem to make up its mind, refusing to properly fuse with the base metal and leaving you with a joint that’s about as sturdy as a stack of soggy pancakes.
But fear not, my friends! With a keen eye and a deep understanding of the underlying causes, we can tackle this pesky problem head-on. You see, lack of fusion can arise from all sorts of culprits, from improper joint preparation to insufficient heat input and everything in between.
Let’s start with the joint preparation, shall we? If those surfaces aren’t properly cleaned and prepped, you’re just asking for trouble. It’s like trying to glue two pieces of wood together without sanding them first – the bond just ain’t gonna hold.
And then there’s the matter of heat input. If you’re not delivering enough juice to that weld pool, the metal just can’t seem to melt and fuse together properly. It’s like trying to light a campfire with a single match – you might get a little spark, but it ain’t gonna roar to life.
But don’t worry, my fellow welding warriors, we’ve got a few tricks up our sleeves to keep those fusion problems at bay. It’s all about paying close attention to the welding parameters, using the right filler materials, and making sure that joint is prepped to perfection. And when it comes to inspection, don’t be afraid to break out the big guns – dye penetrant, X-ray, and even good old-fashioned visual inspection can all help you sniff out those pesky fusion issues before they cause any real damage.
So, the next time you’re faced with a weld that just doesn’t seem to be sticking, don’t panic! With a little bit of know-how and the right tools, you can tackle those fusion problems head-on and come out on top. After all, a good welder is always ready to face down the toughest welding challenges, lack of fusion and all!
Preventing Welding Defects: A Proactive Approach
Alright, my fellow welding warriors, now that we’ve taken a deep dive into the murky waters of welding defects, it’s time to talk about the really juicy stuff – prevention! Because let’s be honest, it’s always better to nip these problems in the bud before they can even rear their ugly heads, am I right?
So, where do we start? Well, it all begins with a solid understanding of the underlying causes. As we’ve already seen, these welding defects can be the result of a whole host of factors, from improper welding technique to poor joint preparation. And the key to prevention is tackling those root causes head-on.
Take porosity, for instance. We know that those pesky little gas bubbles can be the result of contaminants in the base metal or the filler material, or even issues with the shielding gas. So, what’s the solution? Well, it’s all about dialing in those welding parameters, carefully selecting your materials, and maintaining a clean, well-ventilated work environment.
And when it comes to cracks, it’s all about managing those residual stresses and controlling the cooling rate. By using the right welding technique, preheating the base metal, and employing post-weld heat treatment, we can help those cracks stay far, far away.
But it’s not just about the technical stuff, my friends. Proper training and ongoing education are also key to preventing welding defects. After all, a well-informed welder is a welder who can spot and address those problems before they even have a chance to rear their ugly heads.
And let’s not forget about the good old-fashioned visual inspection. By taking the time to carefully examine those welds, both during and after the process, we can catch those pesky defects early on and nip them in the bud. It’s like a game of “Where’s Waldo?” but with way higher stakes and a whole lot more welding know-how.
So, there you have it, folks – the key to preventing welding defects is a proactive, multi-pronged approach that addresses the root causes, leverages the right tools and techniques, and keeps those welds in tip-top shape. And with a little bit of elbow grease and a whole lot of welding know-how, you’ll be churning out defect-free masterpieces in no time!
Conclusion: Mastering the Art of Welding Defect-Free
Well, there you have it, my fellow welding warriors – a comprehensive guide to the ins and outs of welding defects, from identification to prevention. We’ve tackled the toughest of the tough, from those pesky porosity problems to the dreaded lack of fusion, and I hope you’re feeling a little bit more prepared to take on these welding villains head-on.
But remember, the journey to becoming a welding maestro doesn’t end here. It’s an ongoing process of learning, experimenting, and honing your skills. And let me tell you, the more you dive into this welding world, the more you’ll realize just how much there is to discover.
So, keep your safety goggles on, your welding torch at the ready, and your mind open to new possibilities. Because trust me, the world of welding is full of surprises – and who knows, you might just stumble upon the next big breakthrough in defect prevention.
And if you ever find yourself facing down a particularly pesky welding challenge, remember, you’re never alone. There’s a whole community of welding enthusiasts and experts out there, just waiting to lend a hand (or a welding tip or two). So, don’t be afraid to reach out, ask questions, and learn from the best.
Because at the end of the day, being a welder isn’t just about the technical skills – it’s about a passion for creation, a love of problem-solving, and a never-ending thirst for knowledge. And if you can master those elements, my friends, the possibilities are endless.
So, go forth, wield your welding torch with pride, and conquer those defects like the true welding warrior you are. The future is bright, the metal is hot, and the opportunities are waiting. Let’s do this!