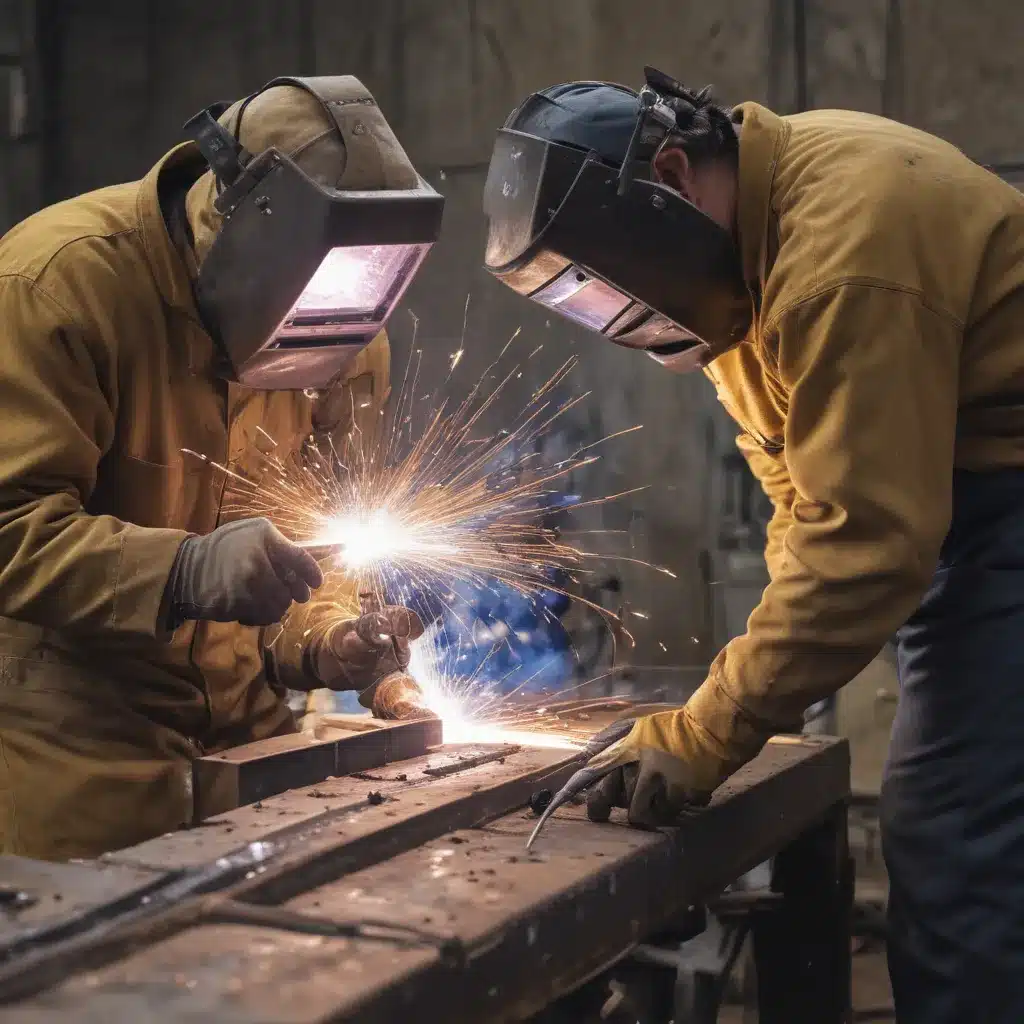
Ah, the wonderful world of welding – where sparks fly, metal fuses, and the magic of fabrication comes to life. As a seasoned welder, I’ve seen it all, from perfect beads that shine like a polished gemstone to… well, let’s just say, the less-than-desirable kind. That’s right, folks – we’re talking about welding defects, the bane of every welder’s existence.
Identifying the Culprits: Common Welding Defects
Now, let’s dive right in, shall we? The first step in tackling any welding challenge is to understand the enemy, so to speak. What are the most common welding defects, you ask? Well, buckle up, because we’ve got quite a list:
-
Porosity: Those pesky little holes that seem to pop up out of nowhere, like unwanted guests at a party. They can be caused by all sorts of things, from contaminated filler metal to improper shielding gas coverage.
-
Lack of Fusion: When the weld just doesn’t seem to, well, fuse with the base metal. It’s like the two just can’t seem to get along, and the result is a weak, inconsistent joint.
-
Undercut: Imagine a little ravine running along the edge of your weld, and you’ve got undercut. This one can be a real pain, as it can weaken the overall structure of the joint.
-
Slag Inclusion: You know those pesky little bits of solidified slag that just won’t seem to go away? Yeah, those are slag inclusions, and they can seriously compromise the strength of your weld.
-
Cracking: The dreaded crack – it can occur in the weld metal, the base metal, or even the heat-affected zone, and it’s a surefire way to ruin your day (and your weld).
Whew, that’s quite a list, isn’t it? But don’t worry, my friends, because I’ve got some tricks up my sleeve to help you avoid and correct these common welding woes.
Preventive Measures: Avoiding Welding Defects
Now, as the old saying goes, “an ounce of prevention is worth a pound of cure.” And when it comes to welding defects, this couldn’t be more true. So, let’s dive in and explore some tried-and-true preventive measures:
Proper Preparation
Remember, the key to a successful weld starts long before you even strike that arc. Ensuring that your base metal is clean, free of contaminants, and properly fit-up can go a long way in preventing those pesky defects.
Optimal Welding Parameters
Ah, the sweet science of welding parameters – get them right, and you’re well on your way to defect-free bliss. We’re talking things like current, voltage, travel speed, and shielding gas flow rate. Dialing in these variables to the manufacturer’s recommendations is crucial.
Skilled Workmanship
As they say, “practice makes perfect.” And when it comes to welding, that couldn’t be more true. Investing in proper training and honing your skills can make all the difference in the world when it comes to avoiding those dreaded defects.
Quality Control
Last but not least, implementing a robust quality control program is essential. Regular inspections, non-destructive testing, and meticulous record-keeping can help you identify issues early and nip them in the bud before they become a bigger problem.
Corrective Action: Addressing Welding Defects
Alright, let’s say you’ve done everything right, but somehow, those pesky defects still manage to rear their ugly heads. Fear not, my friends, because we’ve got some tricks up our sleeves to help you address them.
Porosity
Ah, porosity – the bane of every welder’s existence. To tackle this one, we’ll need to start by identifying the root cause. Is it contaminated filler metal? Improper shielding gas coverage? Once we’ve pinpointed the issue, we can take corrective action, such as changing out the filler metal or adjusting the gas flow.
Lack of Fusion
When it comes to lack of fusion, it’s all about proper joint preparation and welding technique. Make sure your joint is clean, fit-up is tight, and you’re using the right welding parameters. If the problem persists, it might be time to adjust your welding technique or consider a different joint design.
Undercut
Undercut can be a tricky one to address, as it can be caused by a variety of factors, from improper travel speed to incorrect torch angle. The key is to carefully analyze the defect and make targeted adjustments to your welding technique. This might involve slowing down your travel speed, adjusting your torch angle, or even changing the joint design.
Slag Inclusion
When it comes to slag inclusions, the name of the game is thorough cleaning and proper welding technique. Make sure you’re doing a thorough job of removing any slag between passes, and pay close attention to your welding speed and technique to minimize the risk of trapping slag in the weld.
Cracking
Cracking is perhaps one of the most serious welding defects, as it can seriously compromise the structural integrity of your weld. To address this one, you’ll need to carefully analyze the type of crack (hot, cold, or lamellar) and the underlying cause. This might involve adjusting your welding parameters, preheating the base metal, or even using a different filler material.
Now, I know what you’re thinking – that’s a lot of information to take in! But trust me, my friends, mastering the art of avoiding and correcting welding defects is a journey worth taking. After all, the satisfaction of a flawless weld is truly unparalleled.
And, hey, if you ever find yourself in a bit of a welding pickle, remember – the team at Corr Connect is always here to lend a helping hand. Whether you need top-notch welding services or just some good old-fashioned welding advice, we’re your one-stop shop for all things fabrication.
So, there you have it, folks – the lowdown on common welding defects and how to tackle them. Now go forth, wield that welding torch with confidence, and create some truly stunning, defect-free masterpieces. Happy welding!