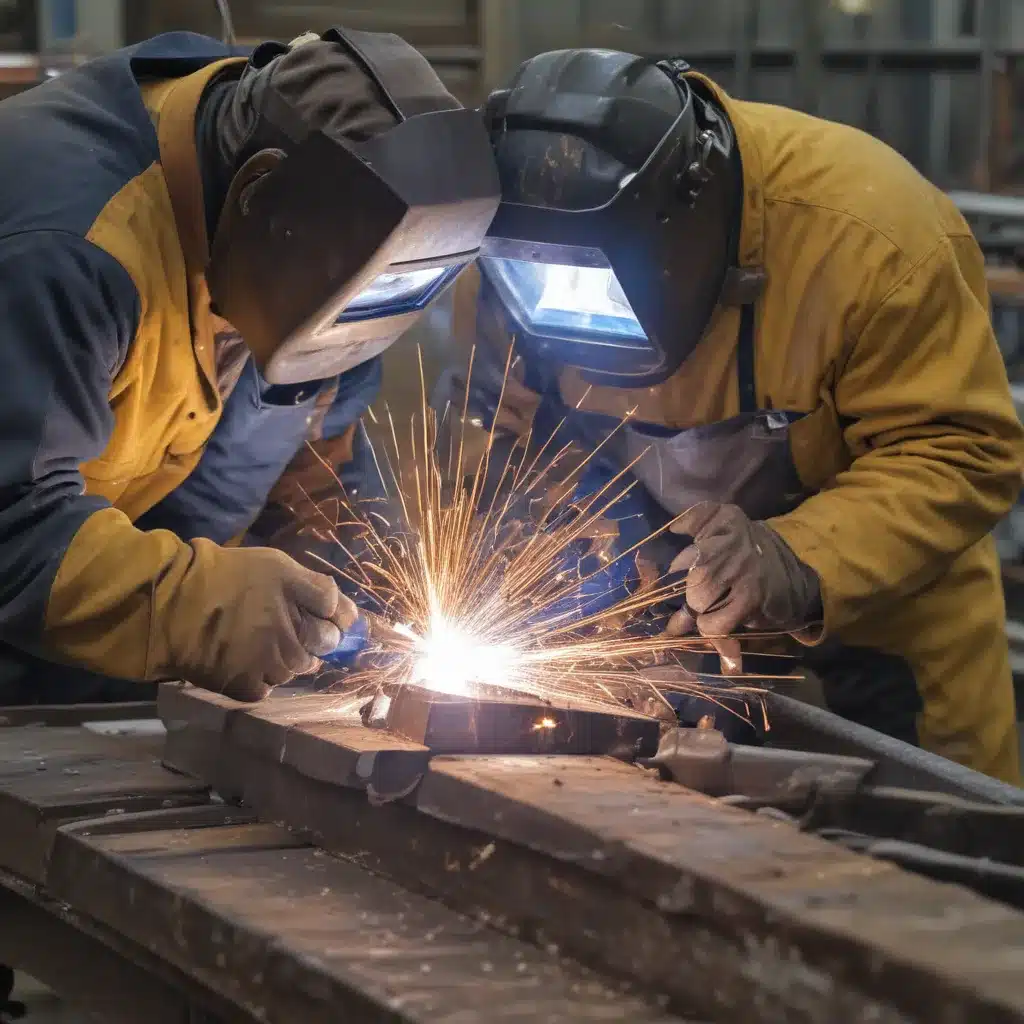
Ah, the world of welding – where sparks fly, metals meld, and the occasional defect can throw a wrench in the works. As someone who’s been in the game for a while, I’ve seen my fair share of welding mishaps. But you know what they say, “knowledge is power,” and that’s precisely what I’m here to share with you today.
Understanding Welding Defects
Let’s start with the basics, shall we? What exactly are these pesky welding defects, you ask? Well, my friends, they’re essentially flaws or imperfections that can arise during the welding process, and they can come in all shapes and sizes. From porosity to undercut, these defects can not only compromise the structural integrity of your welds but also put a serious damper on the overall quality of your work.
But fear not, my fellow welding enthusiasts! I’m about to take you on a journey through the most common welding defects, and more importantly, I’ll share some tried-and-true tips on how to steer clear of them. So, buckle up and get ready to weld your way to perfection.
Common Welding Defects Unveiled
Now, let’s dive into the nitty-gritty of the most prevalent welding defects. First up, we have the notorious porosity. This little bugger manifests as tiny, air-filled cavities within the weld, and it can be a real pain in the you-know-what. Porosity can be caused by all sorts of things, from contaminated filler metal to improper shielding gas flow. But fear not, my friends, because with a little bit of diligence and the right welding techniques, we can nip this problem in the bud.
Next on the list is the dreaded undercut. This one’s like a pesky little trench that forms at the toes of the weld, and it can weaken the overall strength of the joint. Undercut can be caused by a variety of factors, including excessive welding current, improper weld bead placement, or even just plain old fatigue. But don’t worry, with a keen eye and a steady hand, we can steer clear of this tricky little defect.
Ah, and let’s not forget about lack of fusion, the scourge of welders everywhere. This one happens when the weld pool fails to fuse properly with the base metal, leaving a nasty gap behind. Causes can range from insufficient heat input to improper joint preparation, but with the right approach, we can ensure a seamless fusion every time.
Of course, no discussion of welding defects would be complete without mentioning slag inclusions. These pesky little buggers are essentially bits of solidified slag that get trapped within the weld, and they can seriously compromise the strength and integrity of your work. Improper welding technique, contaminated filler metal, or even just plain old human error can all contribute to this problem, but with a little bit of diligence and attention to detail, we can keep those slag inclusions at bay.
And finally, let’s talk about distortion, the bane of every welder’s existence. This one’s all about the warping and bending of the base metal due to the intense heat and stresses of the welding process. Causes can range from uneven heat input to improper clamping, but with the right strategies, we can minimize this pesky problem and keep our welds as straight as an arrow.
Mastering Welding Defect Prevention
Now that we’ve covered the most common welding defects, it’s time to talk about how to avoid them like the plague. And let me tell you, my friends, it’s all about mastering the art of prevention.
First and foremost, it’s crucial to ensure that your welding equipment is in tip-top shape. Regular maintenance and calibration of your machines can go a long way in preventing a whole host of welding defects. And let’s not forget about the importance of using the right consumables, from high-quality filler metals to pristine shielding gases. Trust me, skimping on the essentials can be a surefire way to invite defects into your workshop.
But equipment and materials are just the tip of the iceberg. The real magic happens when you master the welding process itself. Proper joint preparation, optimized welding parameters, and a keen eye for detail can all play a pivotal role in steering clear of those pesky defects. And let’s not forget about the importance of proper post-weld cleaning and finishing – trust me, a little elbow grease can go a long way in ensuring a flawless final product.
Of course, no discussion of welding defect prevention would be complete without a nod to the power of professional training and certification. As someone who’s been in this game for a while, I can attest to the immense value of ongoing education and skill development. Whether it’s mastering the latest welding techniques or brushing up on industry best practices, investing in your own growth can be a surefire way to elevate your welding game and keep those defects at bay.
Embracing a Defect-Free Future
So, there you have it, my friends – a comprehensive guide to the most common welding defects and the secrets to avoiding them. But you know, as much as I love to wax poetic about the technical side of things, I believe that the true key to success in the world of welding lies in something a little more intangible.
It’s all about cultivating a deep passion for your craft, a relentless dedication to quality, and an unwavering commitment to continuous improvement. Because let’s be real, welding isn’t just a job – it’s a way of life. And when you approach it with that kind of fervor, there’s no challenge too great, no defect too daunting.
So, my fellow welding enthusiasts, I challenge you to embrace this defect-free future with open arms. Dive headfirst into the world of welding, hone your skills, and never stop striving for perfection. Because trust me, the rewards of a flawless weld – the pride, the satisfaction, the sheer joy of a job well done – well, they’re worth their weight in gold.
And who knows, maybe one day, you’ll be the one sharing your own hard-earned wisdom with the next generation of welding rockstars. After all, the future of our industry is in our hands, and it’s up to us to shape it – one perfect weld at a time.
Conclusion: A Welding Journey Unbound
Well, there you have it, folks – a deep dive into the world of welding defects and the secrets to avoiding them. But you know, as I reflect on this journey, I can’t help but feel that there’s something even more profound at play here.
You see, the art of welding isn’t just about technical prowess and precision – it’s about the human experience. It’s about the thrill of the spark, the satisfaction of a flawless joint, and the camaraderie that comes with being part of a community of passionate, dedicated individuals. And when you approach welding with that kind of holistic mindset, well, the possibilities are truly endless.
So, my friends, I encourage you to embrace this welding adventure with all your heart. Dive headfirst into the world of defect-free welds, and let your passion be your guide. Because trust me, the rewards of a job well done – the pride, the accomplishment, the sheer joy of it all – they’re worth more than any accolade or certification could ever hope to capture.
And who knows, maybe one day, you’ll be the one inspiring the next generation of welding rockstars, sharing your hard-earned wisdom and helping them navigate the ever-evolving landscape of our industry. Because after all, the future of welding is ours to shape, and it’s up to us to leave our mark – one perfect weld at a time.
So, what are you waiting for, my friends? The welding journey awaits, and the possibilities are as boundless as the sparks that dance across the metal. So, let’s dive in, embrace the challenge, and forge a future where defects are nothing more than a distant memory. After all, when it comes to welding, the only limits are the ones we set for ourselves.