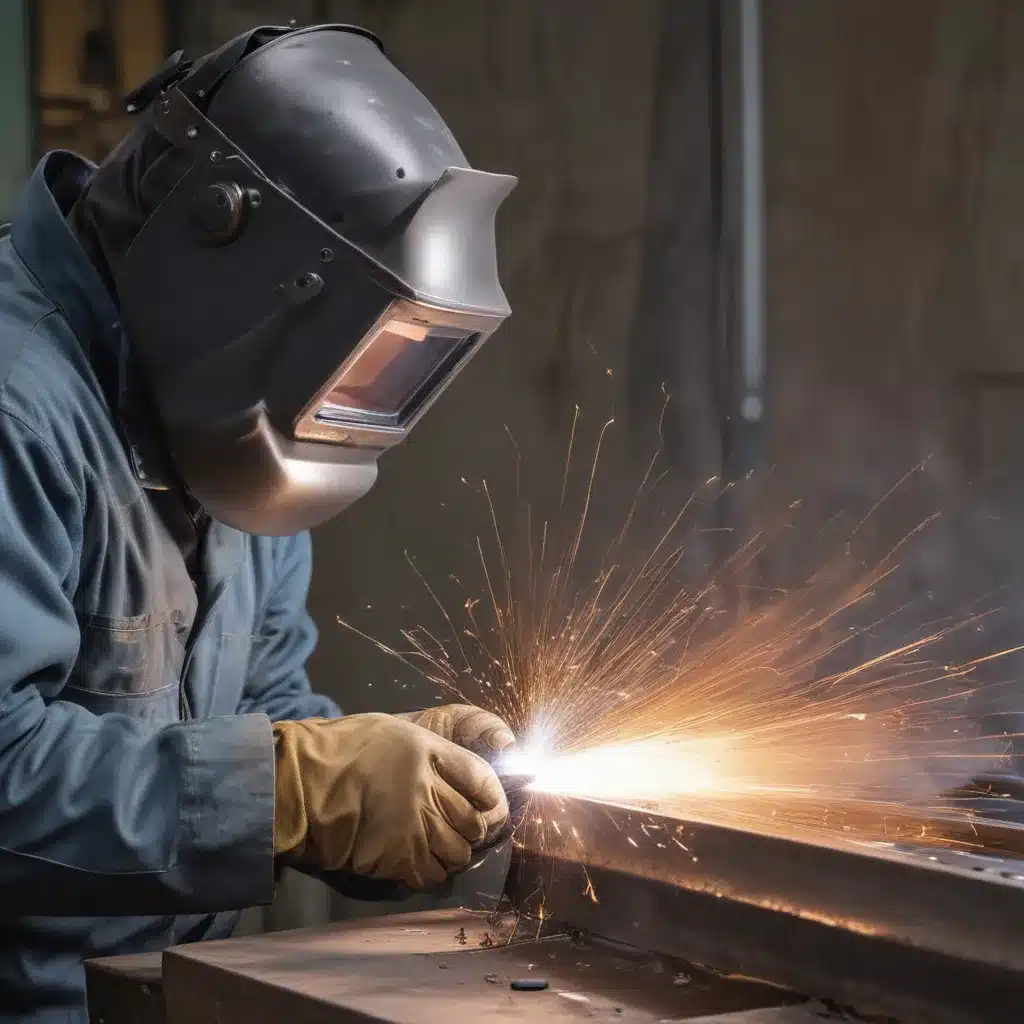
The Importance of Controlling Welding Fumes
As a passionate welder, I’ve spent countless hours perfecting my craft and exploring the nuances of different welding techniques. And let me tell you, one of the most critical aspects of welding that often gets overlooked is the management of fumes. These pesky byproducts of the welding process can pose serious health risks if not properly addressed.
You see, when we heat up metals during welding, a whole host of nasty particles and gases are released into the air. We’re talking about things like ozone, carbon monoxide, and a slew of heavy metals like manganese, chromium, and cadmium. Breathe too much of this stuff in, and you could be looking at everything from respiratory issues to neurological problems down the line. Yikes!
That’s why it’s so important to choose the right welding methods and filler metals to minimize those fumes from the get-go. It’s kind of like building a house – you don’t want to wait until the end to install the smoke detectors, am I right? Nip those fumes in the bud, and you’ll be well on your way to a healthier, safer welding environment.
Exploring Different Welding Processes
Now, when it comes to welding processes, we’ve got a whole smorgasbord of options to choose from. And each one has its own unique set of pros and cons when it comes to fume production.
Take shielded metal arc welding (SMAW), for example. Also known as stick welding, this is one of the most common and versatile welding methods out there. The process involves using a consumable electrode that melts and fuses the base metal together. While it’s relatively simple and cost-effective, stick welding can also be a bit of a fume factory, what with all that molten metal and flux sizzling away.
On the other hand, we’ve got gas metal arc welding (GMAW), or MIG welding as it’s more commonly known. In this process, a solid wire electrode is fed through a welding gun, and the entire thing is shielded by an inert gas like argon or carbon dioxide. The result? A cleaner, more controlled weld with fewer fumes. Plus, MIG welding is pretty darn fast and efficient, making it a popular choice for all sorts of industrial applications.
And let’s not forget about gas tungsten arc welding (GTAW), or TIG welding. This technique uses a non-consumable tungsten electrode to create the arc, with the filler metal being fed in separately. TIG welding is known for its precision and superior weld quality, but it can also be a bit more time-consuming and require more skill to master. The good news? TIG welding generally produces fewer fumes than its stick and MIG counterparts.
Heck, we could go on all day about the different welding processes and their fume-related pros and cons. The key is to really understand the unique characteristics of each method and how they might impact the air quality in your workspace.
Choosing the Right Filler Metals
But it’s not just the welding process that affects fume production – the type of filler metal you use can make a big difference too. You see, different metals and alloys have different melting points, burn rates, and chemical compositions, all of which can influence the types and quantities of fumes that are released.
Take mild steel, for example. It’s a common and widely used base metal, but the filler metals typically used for welding mild steel can be real fume factories. Think about the flux-cored arc welding (FCAW) process, where the filler metal is actually a hollow wire filled with flux. As that wire melts, it releases all sorts of nasty particulates and gases into the air.
On the other hand, stainless steel is a bit of a different beast. The filler metals used for stainless steel welding often contain high amounts of chromium and nickel, which can produce their own unique set of fumes. But the good news is that there are some lower-fume stainless steel filler options out there, like the austenitic-ferritic (duplex) stainless steel electrodes.
And let’s not forget about aluminum welding. This lightweight metal is super popular in all sorts of industries, from automotive to aerospace. But the filler metals used for aluminum can also be real fume-heavy, with elements like magnesium and manganese that can cause some serious health issues if not properly managed.
The moral of the story? When it comes to choosing filler metals, you’ve got to do your homework. Look for options that are specifically designed to minimize fume production, even if they cost a bit more upfront. Trust me, your health (and your team’s) is worth the investment.
Implementing Effective Fume Control Strategies
Okay, so we’ve covered the importance of controlling welding fumes and the different factors that influence fume production. Now, let’s talk about how to actually put that knowledge into practice and create a safer, healthier welding environment.
First and foremost, it’s crucial to have a robust ventilation system in place. This could be anything from a simple local exhaust system that captures fumes right at the source, to a full-blown industrial-grade air filtration system that purifies the entire workshop. The key is to make sure you’ve got adequate airflow and filtration to keep those nasty particles from lingering in the air.
But ventilation is just one piece of the puzzle. You also need to make sure your welders are using the proper personal protective equipment (PPE). We’re talking about things like high-quality respirators, welding helmets with integrated filters, and even specialized welding jackets and gloves. This PPE creates an extra layer of protection against fume exposure.
And let’s not forget about good old-fashioned housekeeping. Regularly cleaning and maintaining your welding equipment, as well as the surrounding work area, can go a long way in reducing fume buildup. Sweep up those metal shavings, keep your consumables organized, and make sure everything is in tip-top shape.
Oh, and speaking of consumables, don’t forget to carefully select and manage your welding filler metals. As we discussed earlier, choosing lower-fume options can make a huge difference in the air quality of your workspace. And be sure to store and handle those filler metals properly to minimize any accidental fume release.
Finally, don’t be afraid to get a little creative with your fume control strategies. Maybe you could experiment with different welding techniques, like pulsed MIG welding, which can help reduce fume production. Or perhaps you could look into specialized welding enclosures or local exhaust hoods to capture those pesky fumes at the source.
The key is to never stop learning and experimenting. Welding fumes are a complex and ever-evolving challenge, but with the right combination of knowledge, technology, and good old-fashioned elbow grease, we can absolutely minimize their impact and create a safer, healthier welding environment for all.
Embracing a Culture of Fume Safety
At the end of the day, managing welding fumes is not just about implementing the right technical solutions – it’s also about cultivating a strong culture of safety and awareness within your organization.
I mean, think about it – even the best ventilation systems and PPE in the world won’t do much good if your welders don’t understand the importance of using them properly. That’s why it’s so crucial to provide comprehensive training and education to your team, covering everything from the health risks of fume exposure to the proper use and maintenance of all your fume control equipment.
And it’s not just about the welders, either. Everyone in your organization, from the project managers to the procurement specialists, needs to be on board with your fume safety initiatives. After all, decisions made upstream can have a huge impact on the air quality in your workshop – things like material selection, job planning, and even scheduling can all play a role.
That’s why it’s so important to foster a collaborative, cross-functional approach to fume management. Encourage open communication, share best practices, and make sure everyone understands their role in keeping those nasty fumes at bay. Because at the end of the day, we’re all in this together, and a little bit of teamwork can go a long way.
But it’s not just about the internal team, either. As a welding service provider, you also have a responsibility to educate and engage your clients on the importance of fume control. After all, the work we do can have a direct impact on the health and safety of the people using the products we create.
So don’t be afraid to be a fume safety evangelist, both within your organization and out in the world. Share your knowledge, promote best practices, and demonstrate the value of proactive fume management. Who knows, you might just inspire others to follow in your footsteps and create a cleaner, healthier welding industry for all.
Conclusion: Embracing a Holistic Approach to Fume Control
At the end of the day, managing welding fumes is not just about finding the right technical solutions – it’s about embracing a holistic, multifaceted approach that encompasses everything from process selection and material choice to training, collaboration, and cultural change.
By carefully considering the fume-related pros and cons of different welding methods and filler metals, and then coupling that with robust ventilation systems, personal protective equipment, and good housekeeping practices, we can dramatically reduce the health risks associated with welding fumes.
But it doesn’t stop there. We also need to cultivate a strong culture of safety and awareness within our organizations, ensuring that everyone – from the welders on the shop floor to the project managers in the boardroom – understands the importance of fume control and is empowered to play a role in its success.
And as welding service providers, we have a responsibility to go even further, sharing our knowledge and best practices with our clients and the broader industry. After all, the work we do has the potential to impact the health and safety of countless individuals, so we owe it to them to be proactive, innovative, and unwavering in our pursuit of fume-free welding.
So let’s embrace this challenge head-on, shall we? Let’s roll up our sleeves, put on our thinking caps, and work together to create a cleaner, healthier, and safer welding industry for all. Who’s with me?
If you’re looking for a welding service provider that takes fume control as seriously as we do, be sure to check out Corr Connect. Their team of experienced professionals is dedicated to using the latest techniques and technologies to minimize fumes and keep their customers safe. Give them a call today and let them show you how they can help take your welding projects to new heights!