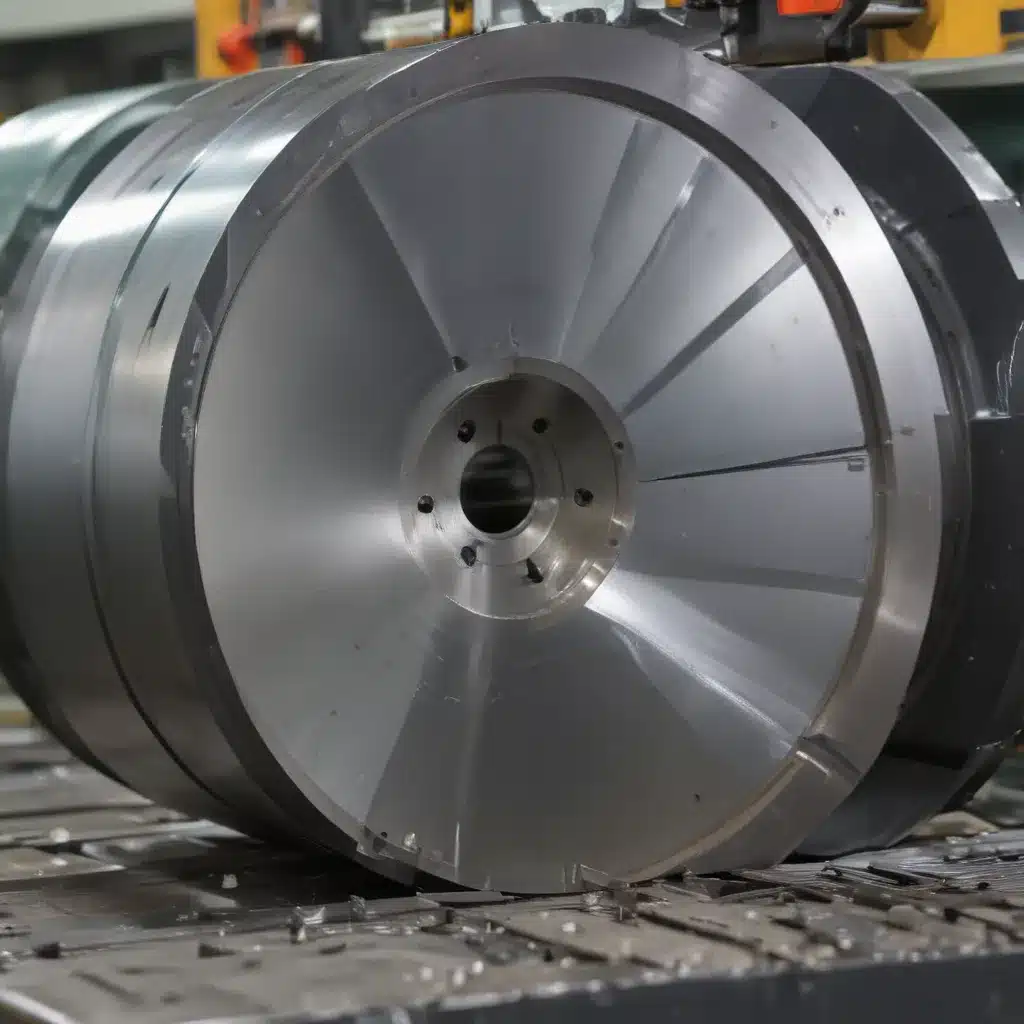
Revolutionizing the Way We Slice Through Metal
Ah, the art of metal cutting – where sparks fly, blades bite, and the thrill of creating something from nothing is palpable. As a seasoned professional in the world of welding and fabrication, I’ve had the privilege of witnessing the incredible advancements that have transformed this industry. It’s like being a kid in a candy store, except the candy is a scorching hot, molten metal and the toys are the latest and greatest cutting tools.
Let me take you on a journey through the cutting-edge (pun intended) world of metal cutting technology. Prepare to have your mind blown, your horizons expanded, and your perspective on this industrial art form forever changed.
The Rise of Plasma Cutting: Slicing Through Steel with Precision and Power
Remember the good old days when we had to rely on clunky oxy-acetylene torches to carve through thick slabs of metal? Those days are long gone, my friends. Enter the plasma cutter – the Jedi knight of the metal cutting world. These bad boys use a concentrated, superheated plasma arc to slice through steel, stainless steel, aluminum, and even some exotic alloys with surgical precision.
The beauty of plasma cutting lies in its sheer power and versatility. I’ve used these machines to cut through steel plates up to 1 inch thick with ease, and the level of detail and intricacy we can achieve is simply mind-boggling. Gone are the days of ragged, uneven edges and laborious grinding – plasma cutting delivers clean, straight cuts every time.
But the real game-changer is the CNC (Computer Numerical Control) plasma cutting machines. These computerized marvels allow us to program complex cutting patterns and shapes, transforming the most intricate designs into stunning metal masterpieces. I’ve seen my team create everything from laser-cut logo designs to intricately detailed, custom-fabricated architectural elements using these CNC plasma cutters. It’s like having a digital sculptor in the shop, except this one wields a blazing-hot plasma beam instead of a chisel.
Laser Cutting: The Precision Surgeon of the Metal Fabrication World
If plasma cutting is the Jedi knight, then laser cutting is the surgeon – precise, focused, and capable of the most delicate of procedures. These cutting-edge (pun fully intended) machines use a high-powered laser beam to slice through metal with an accuracy that’s simply mind-blowing.
I still remember the first time I saw a laser cutter in action. It was like watching a hot knife through butter, except the “butter” was a 1/4-inch thick stainless steel plate. The laser beam cuts with such precision that it can create intricate patterns, complex shapes, and even micro-level details that would be impossible to achieve with traditional cutting methods.
But the real magic happens when we pair these laser cutters with advanced CAD (Computer-Aided Design) software. Our team can now take a digital design, import it into the laser cutter’s control system, and watch as the machine effortlessly translates that vision into a physical, metal masterpiece. It’s like having a digital genie that can grant our every metal-cutting wish.
Water Jet Cutting: The Gentle Giant of Metal Fabrication
While plasma and laser cutting are the rock stars of the metal cutting world, water jet cutting is the quiet, unassuming giant that deserves its moment in the spotlight. These machines use a high-pressure stream of water, often mixed with an abrasive material, to slice through even the toughest of metals with incredible precision and minimal heat distortion.
One of the key advantages of water jet cutting is its ability to handle a wide range of materials, from stainless steel and titanium to ceramics and even glass. And the level of detail and complexity we can achieve is simply breathtaking. I’ve watched our water jet cutter carve out intricate patterns, delicate curves, and even three-dimensional shapes with a level of precision that still amazes me.
But the real beauty of water jet cutting lies in its gentle touch. Unlike the intense heat and sparks of plasma and laser cutting, water jet cutting is a relatively cool process that leaves the surrounding metal virtually unaffected. This makes it the ideal choice for delicate parts, thin materials, or applications where heat-affected zones are a concern.
The Marriage of Tech and Tradition: CNC Machining and Manual Cutting
As much as I love the shiny, high-tech cutting machines, I have a deep appreciation for the timeless art of manual metal cutting. There’s something almost meditative about the careful, precise movements of a skilled metal worker wielding a plasma torch or oxy-acetylene torch, skillfully guiding the flame to create intricate, custom-fabricated parts.
But the real magic happens when we combine the best of both worlds – the precision and efficiency of CNC machining with the artistic flair and problem-solving skills of manual metal cutting. Our team has developed a seamless workflow where we leverage the power of CNC technology to handle the heavy lifting, and then use our skilled welders and fabricators to add the finishing touches, refine the details, and create truly one-of-a-kind metal masterpieces.
It’s like a symphony, with the CNC machines providing the driving rhythm and our skilled metal workers adding the expressive, improvisational flourishes. The result? Consistently high-quality parts that also capture the unique character and personality of the craftsman’s touch.
The Future of Metal Cutting: Endless Possibilities
As I look to the horizon, I can’t help but feel a sense of excitement and anticipation for the future of metal cutting technology. The pace of innovation in this industry is simply staggering, and I can’t wait to see what the next few years (or even months) will bring.
Will we see the rise of even more powerful, precision-focused laser cutting systems? Perhaps the emergence of hybrid cutting technologies that seamlessly combine the best of plasma, laser, and water jet cutting? Or maybe the integration of advanced robotics and artificial intelligence to push the boundaries of what’s possible in metal fabrication?
One thing I’m certain of is that the future of metal cutting will be defined by a relentless pursuit of precision, efficiency, and innovation. And as a passionate advocate for this industry, I can’t wait to be a part of that journey. So keep your eyes peeled, my friends, because the metal cutting revolution is just getting started.
And remember, if you’re ever in need of top-notch welding, metal cutting, or custom fabrication services, be sure to check out Corrconnect.org. Our team of skilled professionals is always here to bring your metal-working dreams to life.