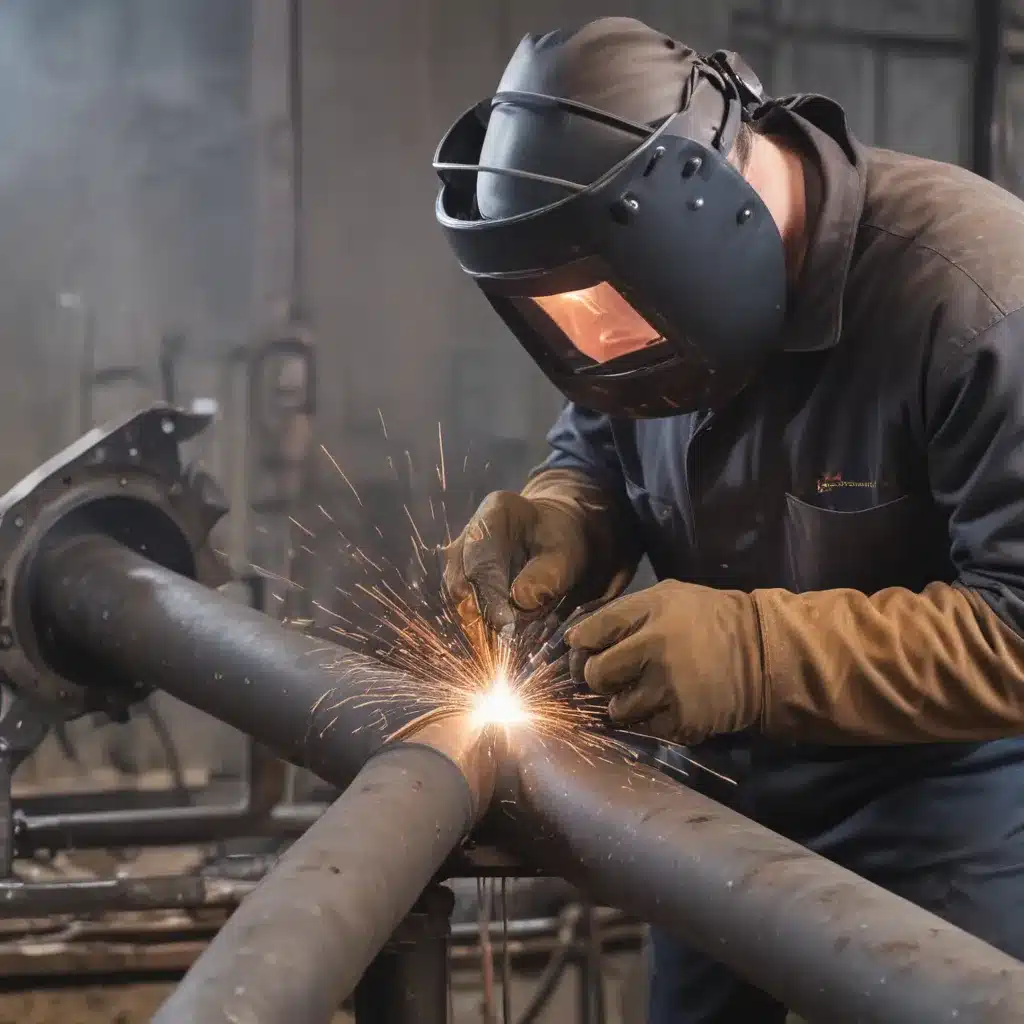
The Importance of Proper Pipe Welding Techniques
Ah, the age-old art of pipe welding – where the fusion of metal becomes a symphony of sparks, heat, and precision. As a seasoned welder, I can attest to the sheer satisfaction that comes from mastering the various positions and techniques required for this specialized craft. Whether you’re tackling a simple straight-run or navigating the intricate angles of a complex elbow joint, the skills involved in welding pipe are truly a testament to the ingenuity of the human mind.
But let’s not get ahead of ourselves here. Pipe welding is no walk in the park, my friends. It requires a keen eye, a steady hand, and a deep understanding of the materials and processes involved. From the selection of the proper filler metal to the execution of the weld, every step must be carefully planned and executed to ensure a strong, durable, and aesthetically pleasing result.
Exploring the Diverse Positions of Pipe Welding
Now, let’s dive into the heart of the matter – the various positions in which pipe welding can be performed. Each position presents its own unique challenges and considerations, and mastering them all is the mark of a true welding virtuoso.
The Flat Position: A Solid Foundation
Let’s start with the flat position, which is often considered the easiest and most straightforward of the pipe welding positions. In this orientation, the pipe is positioned horizontally, with the weld joint facing upwards. The gravitational forces at play make it easier to control the molten metal, resulting in a more consistent and smooth weld bead. This position is particularly well-suited for straight-run pipe installations, where the welder can simply work their way around the circumference of the joint.
However, don’t let the relative simplicity of the flat position fool you. Maintaining a steady hand and a consistent travel speed is crucial to ensuring a high-quality weld. The welder must also be mindful of the potential for sagging or distortion, which can occur if the heat input is not properly managed.
The Horizontal Position: A Lateral Challenge
Moving on, we have the horizontal position, where the pipe is oriented with the weld joint facing to the side. This position can be a bit trickier, as the welder must contend with the effects of gravity pulling the molten metal downwards. Proper body positioning and control of the welding torch become even more critical in this scenario, as the welder must work against the natural tendency of the weld pool to sag or drip.
One of the key considerations when welding in the horizontal position is the need to maintain a consistent bead width and penetration. The welder must carefully manipulate the torch angle and travel speed to ensure that the molten metal is evenly distributed along the joint. Overcoming the challenges of this position requires a great deal of practice and a keen understanding of the underlying principles of pipe welding.
The Vertical Position: Defying Gravity
Now, let’s talk about the vertical position, where the pipe is oriented with the weld joint facing upwards or downwards. This position can be particularly demanding, as the welder must contend with the forces of gravity working against them. When welding in the vertical up position, the molten metal has a tendency to drip or sag, requiring the welder to carefully control the travel speed and torch angle to maintain a consistent weld bead.
Conversely, in the vertical down position, the welder must be mindful of the potential for excessive penetration and undercut, as the molten metal can easily accumulate and create undesirable irregularities in the weld profile. Striking the right balance between travel speed, heat input, and torch manipulation is essential for ensuring a high-quality vertical weld.
The Overhead Position: The Pinnacle of Pipe Welding
Finally, we come to the overhead position, which is often considered the most challenging of all the pipe welding orientations. In this scenario, the pipe is positioned with the weld joint facing downwards, forcing the welder to work against the forces of gravity and the tendency of the molten metal to drip or sag.
Mastering the overhead position requires a exceptional level of control and dexterity. The welder must carefully manage the heat input, travel speed, and torch angle to ensure that the molten metal is evenly distributed and solidifies into a strong, uniform weld bead. Proper body positioning and the use of specialized welding techniques, such as the stringer bead or the weave bead, can also be crucial in overcoming the challenges of the overhead position.
Navigating the Complexities of Pipe Welding
As you can see, the world of pipe welding is a veritable minefield of technical challenges and considerations. But fear not, my fellow welding enthusiasts! With the right mindset, the proper training, and a healthy dose of perseverance, you can conquer these obstacles and become a true master of the craft.
One of the key things to remember when tackling pipe welding is the importance of continual learning and practice. The more diverse the welding positions and joint configurations you’ve encountered, the better equipped you’ll be to handle whatever challenges come your way. And let’s not forget the value of hands-on experience – nothing can truly prepare you for the real-world complexities of pipe welding like actually getting out there and putting your skills to the test.
Of course, it’s not just about the technical aspects of the job. As a welder, you must also possess a keen eye for detail, a strong sense of problem-solving, and the ability to work efficiently and safely in a variety of environments. Whether you’re battling the elements on a construction site or navigating the tight confines of a cramped industrial space, your adaptability and problem-solving skills will be put to the test time and time again.
But the true reward in all of this? The sense of accomplishment that comes from a job well done. There’s nothing quite like the satisfaction of seeing a beautifully executed weld, knowing that your hard work and dedication have resulted in a strong, durable, and visually stunning final product. And let’s not forget the camaraderie and sense of community that comes with being part of the welding trade – a brotherhood (and sisterhood!) of skilled artisans who take immense pride in their craft.
Putting it All Together: A Holistic Approach to Pipe Welding
So, where does all of this leave us? Well, my friends, it means that becoming a true master of pipe welding is no easy feat. It requires a deep understanding of the underlying principles, a keen eye for detail, and a willingness to constantly learn and adapt. But with the right mindset, the proper training, and a healthy dose of perseverance, the rewards of this challenging yet immensely rewarding craft can be truly profound.
And let’s not forget the importance of the right tools and equipment for the job. At Corrconnect.org, we pride ourselves on providing the highest-quality welding supplies and accessories to help you tackle even the most complex pipe welding projects with confidence and efficiency. From specialized welding machines to cutting-edge personal protective equipment, we’ve got you covered every step of the way.
So, whether you’re just starting out on your welding journey or you’re a seasoned pro looking to hone your skills, I encourage you to embrace the challenges and complexities of pipe welding. After all, the true joy of this craft lies in the journey – the constant learning, the problem-solving, and the sense of accomplishment that comes from a job well done. So, let’s get out there and start welding!