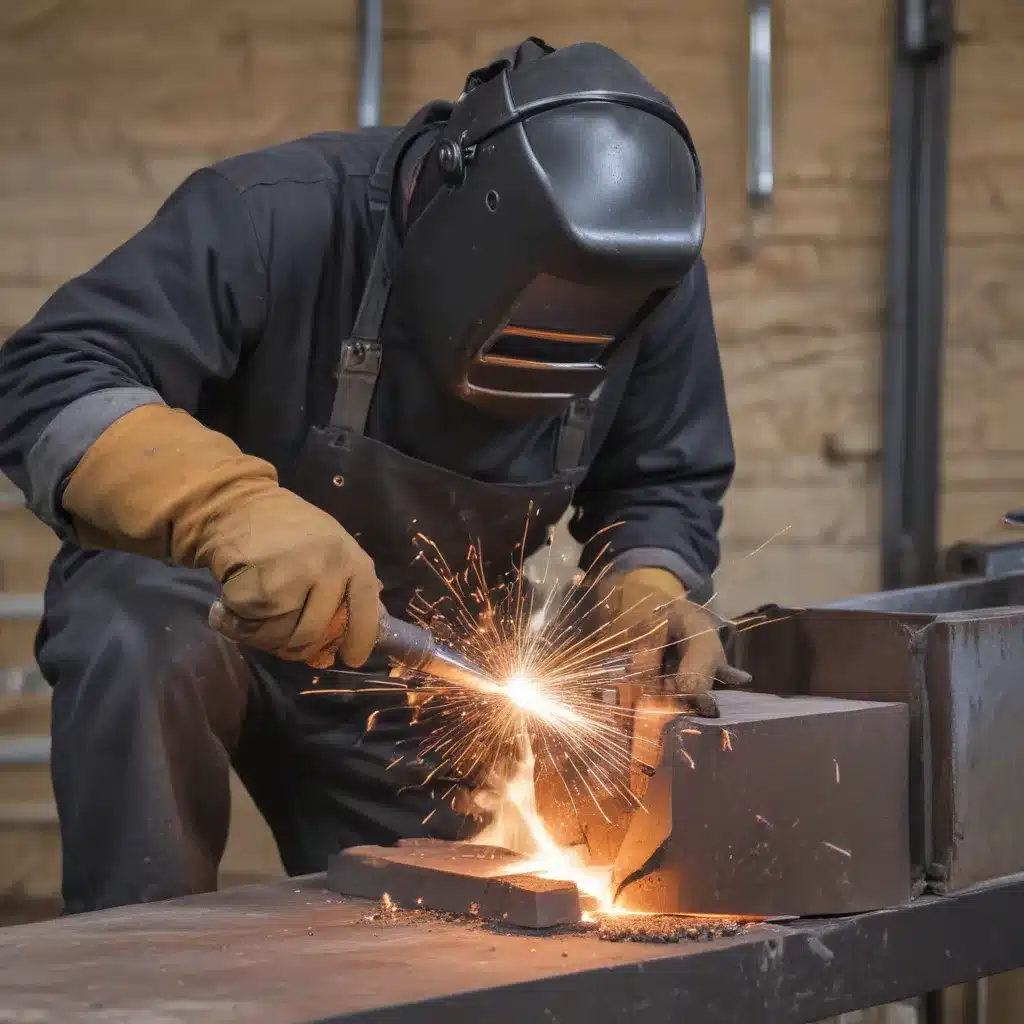
The Mystique of Cast Iron Welding
Ah, cast iron – that sturdy, enigmatic material that has captivated DIY enthusiasts and seasoned metalworkers alike. As a beginner, the thought of welding cast iron might seem daunting, conjuring images of sparks flying and molten metal dancing to the rhythm of a skilled welder’s torch. But fear not, my friends! Today, we’re going to dive deep into the world of cast iron welding and uncover the secrets that will have you wielding that welding gun like a true pro.
You see, cast iron is a unique metal that has a mind of its own. It’s stubborn, it’s moody, and it demands respect. But once you understand its quirks and learn the right techniques, you’ll be able to tame the cast iron beast and turn it into a work of art.
So, buckle up, grab your welding gear, and let’s embark on a journey that will have you confidently tackling those cast iron projects in no time. By the end of this guide, you’ll be a cast iron welding aficionado, ready to take on any challenge that comes your way.
The Properties of Cast Iron: Friend or Foe?
Let’s start by understanding the nature of cast iron, shall we? This material is essentially an alloy of iron, carbon, and other elements, and it’s known for its exceptional strength, durability, and resistance to wear and tear. However, these very same properties that make cast iron so desirable can also make it a bit of a diva when it comes to welding.
You see, cast iron has a relatively high carbon content, which can make it prone to cracking and warping during the welding process. It also has a higher melting point compared to other metals, which means that you’ll need to bring out the big guns (or rather, the hot torches) to get it to play nicely.
But don’t let these challenges intimidate you! With the right techniques and a bit of practice, you can absolutely master the art of cast iron welding. It’s all about understanding the material’s unique characteristics and tailoring your approach accordingly.
For instance, did you know that cast iron has a tendency to form a hard, brittle surface layer when it’s heated and cooled too quickly? This can make it tricky to achieve a smooth, even weld. To combat this, you might need to preheat the cast iron before welding, and then slowly cool it down afterward to prevent those pesky cracks and warps.
Choosing the Right Welding Process for Cast Iron
Now that we’ve got a better understanding of the properties of cast iron, let’s talk about the different welding processes you can use to tame this beast.
One of the most popular methods for welding cast iron is shielded metal arc welding, commonly known as stick welding. This technique uses a consumable electrode that melts and fuses with the cast iron, creating a strong, durable weld. The key with stick welding cast iron is to use a low-hydrogen electrode, which can help minimize the risk of cracking and porosity.
Another option to consider is gas metal arc welding, or GMAW (also known as MIG welding). This process uses a continuously fed wire electrode and a shielding gas to create the weld. GMAW can be a great choice for cast iron, as the shielding gas helps to protect the molten metal from oxidation and contamination.
But wait, there’s more! If you’re feeling particularly adventurous, you could also try gas tungsten arc welding (GTAW), or TIG welding. This process uses a non-consumable tungsten electrode and a shielding gas to create a high-quality weld. TIG welding can be especially useful for precision work on cast iron, as it allows for excellent control and accuracy.
Ultimately, the best welding process for your cast iron project will depend on factors like the thickness of the material, the complexity of the weld, and your own personal experience and skill level. Don’t be afraid to experiment and find the method that works best for you.
Preparing the Cast Iron for Welding
Alright, now that we’ve covered the basics of cast iron welding, it’s time to talk about the all-important preparation step. Trust me, this is where the magic happens, and it can make or break your final weld.
First and foremost, you’ll need to clean the cast iron surface like your life depends on it. Any dirt, grease, or rust can seriously compromise the integrity of your weld, so it’s crucial to get that metal squeaky clean. You can use a wire brush, sandpaper, or even a degreasing solvent to remove any contaminants.
But wait, there’s more! Once the surface is sparkling clean, you’ll also want to preheat the cast iron before welding. This step helps to reduce the risk of cracking and warping, as it allows the metal to expand and contract more evenly during the welding process.
The ideal preheating temperature will depend on the thickness of your cast iron, but as a general rule of thumb, you’ll want to aim for around 400-500°F (200-260°C). You can use a torch, a furnace, or even an oven to achieve this, just be sure to monitor the temperature carefully and avoid overheating.
And let’s not forget about the importance of proper joint preparation. Depending on the type of weld you’re going for, you may need to bevel the edges of the cast iron, create a groove, or even add a backing material to support the weld. This step can take a bit of practice, but trust me, it’s worth the effort.
By taking the time to properly prepare your cast iron, you’re setting yourself up for welding success. It’s like the old saying goes: “Measure twice, cut once.” In this case, it’s “Prepare well, weld better.”
Mastering the Weld: Techniques and Tips for Cast Iron
Alright, now that we’ve got the prep work out of the way, it’s time to dive into the nitty-gritty of actually welding that cast iron. Get ready, because this is where the real magic happens.
One of the key things to keep in mind when welding cast iron is the importance of maintaining a tight, controlled arc. You see, cast iron has a tendency to want to “suck in” the molten metal, which can lead to uneven weld beads and even the dreaded porosity. To combat this, you’ll want to keep your arc length short and your travel speed consistent.
Another important technique to master is the art of multi-pass welding. Because cast iron is prone to cracking and warping, it’s often necessary to lay down multiple weld passes to build up the joint and distribute the heat more evenly. This can be a bit tricky, as you’ll need to carefully time your passes and monitor the temperature of the cast iron to prevent distortion.
But don’t worry, with a little practice, you’ll be laying down those perfect multi-pass welds like a pro. And let’s not forget about the importance of post-weld heat treatment. Once you’ve finished the welding, it’s a good idea to slowly cool the cast iron to help minimize the risk of cracks and other defects.
And let’s not forget about the importance of troubleshooting. As you’re welding, keep an eye out for any signs of trouble, like excessive spatter, porosity, or cracking. If you notice anything amiss, don’t be afraid to stop and assess the situation. Sometimes a slight adjustment to your technique or the welding parameters can make all the difference.
Remember, cast iron welding is an art form, and it takes time and practice to truly master it. But with the right techniques, a bit of patience, and a whole lot of determination, you’ll be turning out flawless cast iron welds in no time.
Real-World Examples: Conquering Cast Iron Welding Challenges
Now, I know what you’re thinking: “This all sounds great, but how do I apply these techniques in the real world?” Well, my friends, let me share a few real-life examples that will have you feeling like a cast iron welding superhero.
Take, for example, the case of our client, Jane, who came to us with a cast iron antique stove that she wanted to restore. The poor thing had seen better days, with cracks and pits all over the surface. But with our expert cast iron welding skills, we were able to carefully fill those imperfections, preserving the stove’s original charm while making it as good as new.
Or how about the time we worked with a local blacksmith to create a stunning cast iron sculpture for a public park? This project required precision welding to join the intricate, delicate components, and we had to be extra careful to maintain the desired aesthetic. But with our pre-heating techniques and multi-pass welding expertise, we were able to produce a work of art that left the community in awe.
And let’s not forget about the time we were called in to repair a cast iron farm implement that had been damaged in a freak accident. The client was worried that the piece was beyond repair, but we knew better. With our deep understanding of cast iron welding, we were able to carefully restore the implement to its former glory, saving the client a significant amount of money and preventing the need for a costly replacement.
These are just a few examples of how our cast iron welding expertise has made a real difference for our clients. And let me tell you, the satisfaction of taking on a seemingly impossible challenge and emerging victorious is simply unparalleled.
So, whether you’re restoring a cherished antique, creating a one-of-a-kind piece of art, or repairing a crucial piece of equipment, don’t be afraid to put your cast iron welding skills to the test. With the right techniques and a bit of determination, you can conquer any challenge that comes your way.
The Power of Collaboration: Enhancing Your Cast Iron Welding Journey
Now, as much as I’d love to claim that I’ve mastered the art of cast iron welding all on my own, the truth is that I’ve had a lot of help along the way. And that’s the beauty of this craft – it’s a collaborative effort that brings together a wealth of knowledge, experience, and expertise.
You see, cast iron welding is a bit like a dance, and you need to be in sync with your partners to truly make it work. That’s why I’ve always made it a point to collaborate with other welding professionals, from seasoned veterans to up-and-coming stars in the field.
Take, for instance, the time I had the privilege of working with a renowned metallurgist who specialized in cast iron. Together, we delved deep into the science behind this enigmatic material, exploring the intricacies of its chemical composition and microstructure. This collaboration not only expanded my own understanding of cast iron welding but also allowed me to develop more targeted and effective techniques for my clients.
And then there was the time I teamed up with a team of fabricators who had years of experience working with cast iron. These guys had seen it all, from the most intricate architectural pieces to the rugged industrial equipment that keeps our world running. By tapping into their wealth of knowledge, I was able to refine my skills and tackle even the most challenging cast iron welding projects with confidence.
But it’s not just about learning from the experts – sometimes, the best insights come from unexpected sources. I’ll never forget the time I had a chance to chat with a passionate cast iron collector who shared their deep appreciation for the history and craftsmanship behind these iconic pieces. That conversation opened my eyes to the cultural significance of cast iron, and it inspired me to approach each welding project with a newfound sense of reverence and respect.
You see, the world of cast iron welding is a tapestry woven with the stories, experiences, and perspectives of countless individuals. And by embracing the power of collaboration, we can not only elevate our own skills but also contribute to the rich and ever-evolving legacy of this remarkable craft.
So, if you’re on your own cast iron welding journey, don’t be afraid to reach out and connect with others who share your passion. You never know what sparks of inspiration might fly, or what new techniques you might discover. After all, the true power of cast iron welding lies not just in the metal itself, but in the shared knowledge and camaraderie that brings us all together.
Unleash Your Inner Cast Iron Welder: Final Thoughts and Next Steps
Well, my friends, we’ve covered a lot of ground in this beginner’s guide to cast iron welding, haven’t we? From understanding the unique properties of this enigmatic material to mastering the techniques that will have you wielding that welding gun like a pro, I hope you’re feeling more confident and excited about tackling your own cast iron projects.
But remember, the journey of a cast iron welder is never truly complete. There’s always something new to learn, a new challenge to conquer, or a new artistic expression to unveil. And that’s the beauty of it – the endless possibilities that await those who are willing to embrace the mysteries of cast iron.
So, where do you go from here? Well, the first step is to get out there and start practicing. Experiment with different welding processes, play around with various techniques, and don’t be afraid to make a few mistakes along the way. After all, that’s how we learn and grow as cast iron welders.
And don’t forget to stay curious and open-minded. Seek out opportunities to collaborate with other welding enthusiasts, attend industry events, and immerse yourself in the rich history and culture of cast iron craftsmanship. The more you engage with this vibrant community, the more you’ll discover about the true depth and breadth of this remarkable material.
Remember, the road to becoming a cast iron welding master may be long and winding, but it’s a journey that’s well worth taking. So, grab your gear, fire up that torch, and get ready to unleash your inner cast iron welder. The possibilities are endless, my friends, and the rewards are truly beyond measure.
Now, if you’ll excuse me, I’ve got a few cast iron projects of my own to tackle. But I’ll be here, waiting to hear all about your own cast iron welding adventures. So, what are you waiting for? Let’s get to work!