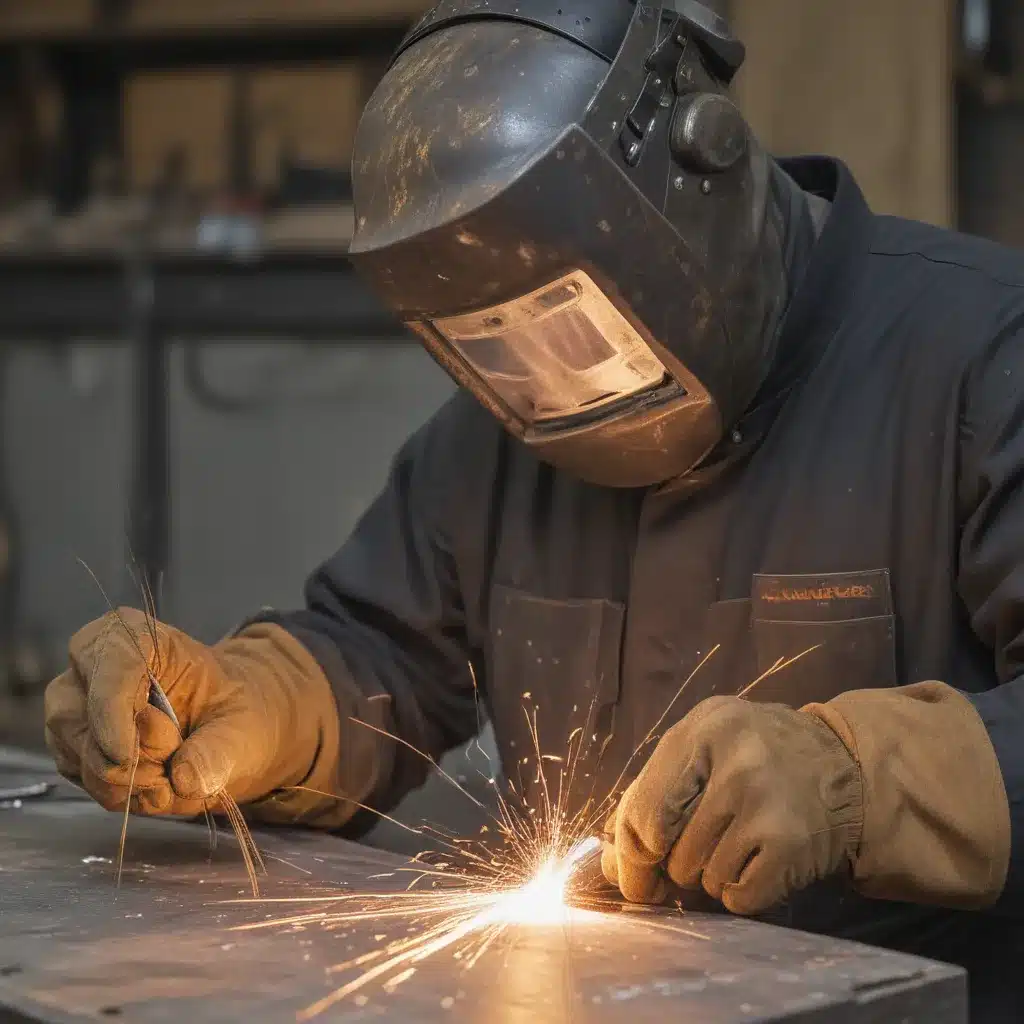
The Humble Origins of Stick Welding
Ah, the humble art of stick welding – where sparks fly, metal fuses, and the very foundations of industry are forged. As a beginner, you might be wondering, “What’s the big deal with this old-school welding technique, anyway?” Well, my friend, let me tell you a tale that will change the way you look at those humble metal sticks forever.
You see, stick welding, also known as shielded metal arc welding (SMAW), has been around since the late 19th century. It all started with a spark of ingenuity when a Norwegian-American inventor named Oscar Kjellberg decided to encase an electrode in a protective coating. This simple innovation revolutionized the world of welding, making it more accessible and versatile than ever before.
Imagine a time before the sleek, modern welding machines we have today. Back then, welders had to rely on bulky, temperamental equipment and crude techniques. But Kjellberg’s invention changed all that. Suddenly, welders could create stronger, more consistent joints with greater ease and control. The age of stick welding had begun, and it would go on to become a cornerstone of industrial progress.
The Basics of Stick Welding
Now, let’s dive into the nitty-gritty of stick welding. At its core, this technique involves using a consumable electrode, which is a metal rod coated in a flux material. When you strike an arc between the electrode and the workpiece, the flux material melts and forms a protective gas shield around the weld pool, shielding the molten metal from the atmosphere and preventing oxidation.
But how does it all work, you ask? Well, let me break it down for you:
-
The Electrode: This is the star of the show – a metal rod with a flux coating. The electrode’s composition and diameter can be tailored to the specific job at hand, allowing for a wide range of applications.
-
The Power Source: Stick welding requires a dedicated power source, typically a transformer-based or inverter-based welding machine. These power sources deliver the necessary current and voltage to create the arc and melt the electrode.
-
The Arc: When you bring the electrode into contact with the workpiece, an electric arc is struck. This arc generates intense heat, melting both the electrode and the base metal, creating a weld pool.
-
The Flux Coating: As the electrode melts, the flux coating decomposes, releasing gases that shield the weld pool from the surrounding air. This helps prevent oxidation and produces a slag that protects the weld as it cools.
-
The Weld Bead: The molten metal from the electrode and the base metal combine to form the weld bead – the solid, fused joint that holds everything together.
Sounds simple, right? Well, don’t be fooled – mastering the art of stick welding takes time, patience, and a keen eye for detail. But with a little practice and the right techniques, you’ll be laying down beautiful, high-quality welds in no time.
When to Use Stick Welding
Ah, the million-dollar question: when should you reach for the trusty stick welder? Well, my friends, the answer lies in the unique advantages and versatility of this welding method.
First and foremost, stick welding shines when it comes to working with thicker materials and joint preparation. The intense heat and penetration of the arc make it an excellent choice for welding heavy steel plates, structural beams, and other thick components. And let’s not forget the incredible versatility – stick welding can be performed in all positions, from flat to vertical to overhead, making it a go-to choice for those tricky, hard-to-reach areas.
But the benefits don’t stop there. Stick welding is also a champ when it comes to handling rusty, dirty, or painted surfaces. The flux coating on the electrode acts as a cleaning agent, melting through those pesky impurities and creating a strong, reliable weld. And let’s not forget the portability factor – stick welders are relatively lightweight and can be easily transported to jobsites, making them a favorite among construction crews and field welders.
Of course, stick welding isn’t without its limitations. The flux-coated electrodes can produce more smoke and spatter than other welding methods, and the weld bead may not be as smooth and uniform as those produced by more advanced techniques. But for many industries, the benefits of stick welding far outweigh the drawbacks.
Real-World Applications of Stick Welding
Now, let’s take a look at some real-world examples of where stick welding shines. One of the classic applications is in the construction and repair of heavy machinery and equipment. Think massive cranes, bulldozers, and mining rigs – the kind of rugged, high-stress equipment that needs the strength and reliability of a stick weld.
But it doesn’t stop there. Stick welding is also a go-to choice for shipbuilding and marine applications. The ability to weld in all positions, combined with the resistance to saltwater and other harsh environments, make it an essential tool for constructing and repairing ships, offshore platforms, and other maritime structures.
And let’s not forget the world of metal fabrication and custom work. Whether it’s crafting intricate sculptures, restoring vintage automobiles, or building custom farm equipment, stick welding provides the perfect blend of strength, versatility, and accessibility that many fabricators and artisans crave.
But perhaps one of the most inspiring applications of stick welding is in the world of community-driven projects and DIY endeavors. Imagine a group of passionate volunteers coming together to build a playground for underprivileged children, or a team of hobbyists restoring a vintage tractor for their local fair. In these cases, the humble stick welder becomes a tool of empowerment, bringing people together to create something truly remarkable.
Mastering the Art of Stick Welding
Alright, so you’re convinced – stick welding is the way to go. But how do you go about mastering this time-honored technique? Well, my friends, it’s all about practice, patience, and a willingness to learn.
First and foremost, you’ll need to invest in the right equipment. A reliable stick welder, a selection of high-quality electrodes, and the proper personal protective equipment (PPE) are all essential. And don’t forget to familiarize yourself with the settings and controls on your welder – understanding the relationship between amperage, voltage, and electrode size is key to achieving consistent, high-quality welds.
Next, it’s time to hit the practice booth (or your own backyard, if you’re feeling adventurous). Start with simple flat welds, mastering the art of striking and maintaining a stable arc. Then, progress to more challenging positions, like vertical and overhead, honing your technique and developing a keen eye for proper weld appearance and penetration.
But the journey to stick welding mastery doesn’t end there. Continual learning and skill-building are essential. Attend workshops, read welding manuals, and watch instructional videos to expand your knowledge and stay up-to-date with the latest techniques and industry trends. And don’t be afraid to experiment – try different electrode types, adjust your parameters, and push the boundaries of what’s possible.
Remember, the road to becoming a stick welding virtuoso is paved with perseverance and a willingness to learn from your mistakes. But trust me, the journey is well worth it. As you become more confident and proficient, you’ll unlock a whole new world of possibilities, from tackling complex fabrication projects to contributing to community-driven initiatives that make a real difference.
So, what are you waiting for? Grab your trusty stick welder, don your PPE, and let the sparks fly! The world of stick welding is calling, and it’s time to answer the call.
Unlocking the Potential of Stick Welding with Precision Services
At Corrconnect.org, we understand the power and versatility of stick welding. As a leading provider of precision welding services, we’ve harnessed the best of this time-honored technique to deliver exceptional results for our clients.
Our team of highly skilled welders have mastered the art of stick welding, utilizing the latest equipment and techniques to create strong, reliable welds on a wide range of materials and project types. From heavy-duty construction and fabrication to intricate custom work, we have the expertise and attention to detail to ensure every weld meets the highest standards of quality and safety.
But our commitment to excellence goes beyond just the welding itself. We also offer a range of complementary services, such as metal cutting, custom fabrication, and a wide array of precision welding options, to provide our clients with a one-stop-shop for all their welding and fabrication needs.
So, if you’re looking to harness the power of stick welding for your next project, whether it’s a large-scale industrial undertaking or a custom DIY creation, be sure to visit our website and explore the possibilities. Together, let’s unlock the full potential of this time-honored welding technique and create something truly remarkable.